Los moldes de fundición a presión son uno de los cuatro elementos esenciales en la producción de fundición a presión (junto con los materiales, el equipo y los procesos de fundición). El agrietamiento de la cavidad del molde de fundición a presión es un modo de fallo común y grave, que afecta directamente a la programación de la producción. Las causas principales de la fisuración de la cavidad del molde incluyen el contacto directo con líquidos metálicos a alta temperatura, la erosión durante la etapa de llenado por el metal que fluye a alta velocidad y el impacto de la alta presión durante la etapa de presurización. Además, la fuerte fluctuación de la temperatura del acero del molde en cada ciclo de fundición contribuye a este problema.
Una empresa de fundición a presión competente afronta los retos que plantean diversos procesos. Abordar y resolver los diferentes problemas de los procesos enriquece la experiencia de fabricación, lo que permite la producción de piezas satisfactorias para diversos clientes.
Factores relacionados con la rotura de moldes de fundición a presión
1.1 Diseño de moldes
1.1.1 Selección de materiales
Para las piezas de conformación de los moldes de fundición a presión, se suelen elegir aceros específicos para moldes de trabajo en caliente. Calidades como el 1.2343 y el 1.2344 son adecuadas para moldes grandes, mientras que el 1.2367 se prefiere para piezas en las que la erosión es severa. Sin embargo, debido a la dificultad de procesamiento y a problemas de templabilidad, el 1.2367 no es ideal para piezas de moldeo muy grandes. Se recomienda utilizar variedades de alto grado procesadas con tecnología de refundición por electroescoria, ya que tienen menor contenido de impurezas y menor variación entre el núcleo y la superficie, lo que reduce el riesgo de agrietamiento.
Modelo | Resistencia a altas temperaturas | Resistencia a altas temperaturas | Resistencia al desgaste a altas temperaturas | Maquinabilidad |
1.2343/8402/H11/SKD6 | ⭐⭐ | ⭐⭐⭐⭐ | ⭐⭐ | ⭐⭐⭐⭐⭐ |
1.2344/8407/H13/SKD61 | ⭐⭐⭐ | ⭐⭐⭐ | ⭐⭐⭐ | ⭐⭐⭐⭐ |
1.2367/8418 | ⭐⭐⭐⭐ | ⭐⭐⭐⭐ | ⭐⭐⭐⭐ | ⭐⭐⭐ |
1.1.2 Forma geométrica del producto
Los riesgos más comunes son:
- a. Estructuras de ranuras profundas con ángulos de calado pequeños o relaciones longitud/diámetro excesivas;
- b. Radios locales insuficientes que provocan concentración de tensiones;
- c. Ángulos de tiro inadecuados en zonas erosionadas por aluminio fundido;
Todos estos riesgos comunes deben mejorarse desde la perspectiva del diseño del producto, como se indica a continuación
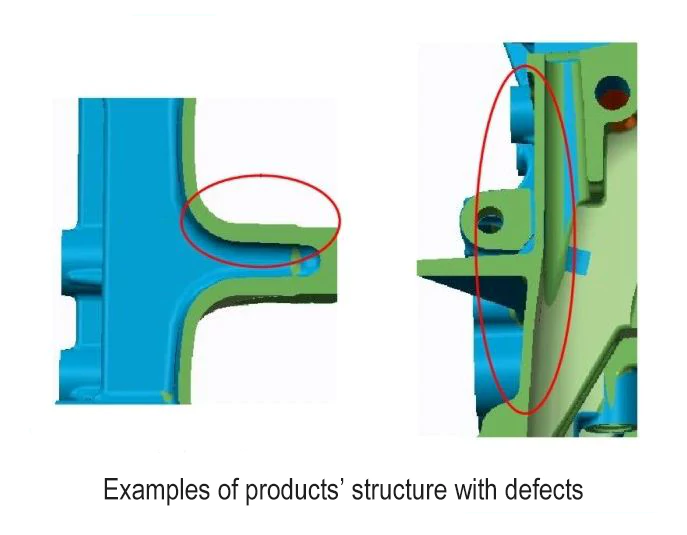
1.1.3 Forma geométrica del molde
Los riesgos más comunes son:
- a. Radios locales insuficientes que provocan concentración de tensiones;
- b. Ángulos agudos y bordes cortantes causados por estructuras de inserción;
- c. Estructuras débiles en los canales de llenado del molde;
Todos estos riesgos comunes deben evitarse desde una perspectiva de diseño de separación.
1.1.4 Diseño del sistema de compuertas
Los riesgos más comunes son:
- a. Radios insuficientes en el diseño de la puerta;
- b. Puertas orientadas hacia zonas estructurales débiles;
Estos riesgos comunes deben evitarse desde el punto de vista del diseño del sistema de compuertas, véase la figura siguiente:
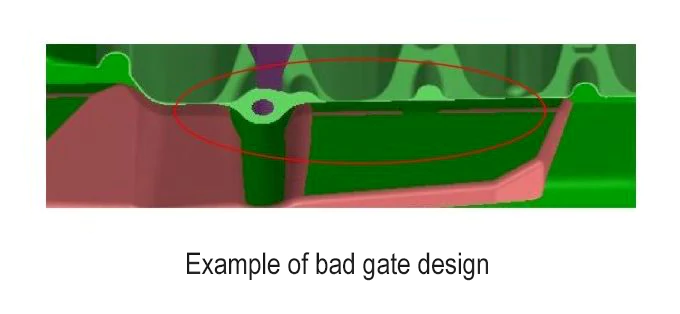
1.1.5 Diseño del sistema de refrigeración
Los riesgos más comunes son:
- a. Orificios de enfriamiento excesivamente profundos que provocan una resistencia local insuficiente;
- b. Disposición deficiente de la refrigeración que provoca importantes diferencias de distribución de la temperatura y tensiones;
Estos riesgos comunes deben equilibrarse desde la perspectiva del diseño del sistema de refrigeración, como se indica a continuación:
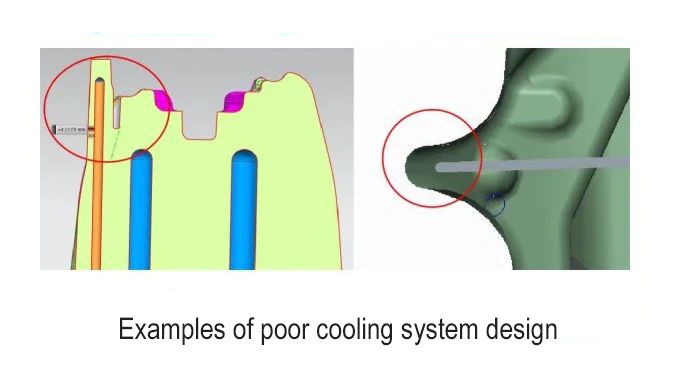
1.2 Fabricación de moldes
1.2.1 Control de materiales
Según las normas de la Asociación Norteamericana de Fundición a Presión (NADCA), los materiales de alta calidad de los principales proveedores suelen cumplirlas o superarlas, lo que reduce la probabilidad de defectos.
1.2.2 Métodos de mecanizado
El mecanizado por descarga eléctrica (EDM) puede afectar a la composición de la superficie y a la estructura del molde, provocando microfisuras y concentración de tensiones. Minimizar el uso de EDM puede reducir significativamente el riesgo de agrietamiento del molde.
1.2.3 Parámetros de mecanizado
Es esencial respetar los parámetros de mecanizado recomendados para el material seleccionado, como la velocidad de corte, el avance por revolución, la profundidad de corte y el tipo de herramienta. Desviarse de estas directrices puede provocar tensiones residuales y posibles grietas por tensión.
1.2.4 Molienda antiestrés
La electroerosión es a menudo inevitable en el procesamiento de grandes moldes de fundición a presión. Tras la electroerosión, es fundamental esmerilar y pulir las zonas afectadas según las directrices del material para eliminar las estructuras dañinas y aliviar la tensión.
1.2.5 Proceso de tratamiento térmico
El tratamiento térmico de los materiales para moldes incluye el ablandamiento, la eliminación de tensiones y el endurecimiento. El cumplimiento de los requisitos detallados sobre medios de temple, velocidad de enfriamiento e intervalos de templado de las directrices de materiales garantiza que la estructura interna y externa del material cumpla las expectativas.
1.2.6 Control de la nitruración
La nitruración mejora la resistencia al desgaste de la superficie del molde, retrasando la erosión causada por el aluminio fundido. Sin embargo, también hace que la superficie sea más quebradiza y aumenta el riesgo de agrietamiento. La profundidad y las condiciones de la nitruración deben controlarse estrictamente, sobre todo en piezas grandes (0,03-0,07 de profundidad).
Diseño de procesos y su impacto
1.3.1 Proceso de moldeo en caliente
El método de iniciar la producción con un molde frío afecta en gran medida a la vida útil del molde, especialmente debido al estrés térmico causado por la alternancia de impactos fríos y calientes. Se recomienda precalentar el molde utilizando una máquina de temperatura de moldes en lugar de empezar directamente con un molde caliente de baja presión. Durante el arranque de un molde frío, suelen ser necesarios entre 5 y 10 ciclos de inyección a baja presión y baja velocidad para elevar la temperatura del molde. Por lo tanto, es crucial evitar iniciar ciclos de inyección de alta velocidad y alta presión demasiado pronto.
1.3.2 Técnicas de refrigeración
Los elegidos proceso de enfriamiento en la producción repercute significativamente en la tensión térmica de la superficie del molde. Esto es evidente en las diferencias de temperatura máxima y mínima durante el ciclo de fundición a presión y en la superficie del molde. Las primeras suelen provocar la aparición de grietas y fisuras, mientras que las segundas pueden causar grietas por tensión.
Un buen proceso de enfriamiento debe tener en cuenta el control del tiempo de agua de enfriamiento, el enfriamiento durante la fase de solidificación y evitar el enfriamiento constante durante todo el ciclo. También es importante controlar la caída de temperatura de la pulverización y depender menos de la pulverización para el enfriamiento. Garantizar un tiempo de ciclo compacto es crucial para evitar grandes fluctuaciones en las diferencias de temperatura del molde dentro del ciclo.
1.3.3 Velocidad de inyección
La erosión del aluminio fundido daña considerablemente el molde. Una velocidad más baja de la compuerta es más beneficiosa para la vida del molde. Para equilibrar la calidad de llenado, se aconseja mantener la velocidad de llenado de la compuerta entre 30-50m/s. Si es posible, tratar de controlar la velocidad de llenado de cada puerta de rama por debajo de 45m / s.
1.3.4 Presión de sobrealimentación
Reducir la presión de inyección es beneficioso para alargar la vida del molde. La presión de inyección recomendada debe ser inferior a 100 MPa. Elegir el momento adecuado para aumentar la presión también es crucial para la longevidad del molde, así que evite hacerlo demasiado pronto o demasiado tarde.
Mantenimiento y cuidados para prolongar la vida del moho
1.4.1 Hábitos de programación de la producción
Los hábitos de programación de la producción afectan significativamente a la vida útil del molde, principalmente debido a las fluctuaciones de temperatura causadas por la producción intermitente. La producción continua de 24 horas conduce a un equilibrio dinámico de la temperatura del molde, reduciendo la diferencia de temperatura en cada ciclo y en las distintas zonas del molde. La producción intermitente, que provoca frecuentes arranques en frío del molde, aumenta el estrés térmico y provoca grietas y fisuras, lo que afecta negativamente a la vida útil del molde.
1.4.2 Comprobaciones puntuales del moho
La eliminación oportuna de la adherencia de aluminio en la superficie del molde puede reducir la resistencia al desmoldeo y retrasar el desarrollo de grietas. Para las zonas muy erosionadas por el aluminio fundido, se recomienda el recubrimiento por electrodescarga para mejorar la resistencia al desgaste local y retrasar la aparición y el desarrollo de grietas.
1.4.3 Mantenimiento de moldes
El recocido periódico de alivio de tensiones puede eliminar en cierta medida las tensiones térmicas. Limpiar la superficie del molde de adherencias de aluminio y suciedad reduce la erosión. Los controles periódicos de cierre correcto del molde puede evitar un apriete excesivo y daños durante el funcionamiento.
Conclusión y medidas preventivas
Para evitar el agrietamiento del molde de fundición a presión, es esencial:
- Minimizar la aparición de ángulos agudos, filetes insuficientes y ángulos de desmoldeo inadecuados en el diseño de moldes. Colabore desde el principio con el diseño del producto para mitigar los riesgos.
- Tenga cuidado al seleccionar materiales de acero con escasas propiedades de endurecimiento pasante para piezas moldeadas de gran tamaño. Evite durezas excesivamente altas y capas de nitruración profundas para evitar diferencias de dureza significativas dentro de la pieza.
- Optar por velocidades de compuerta más bajas, presiones de sobrealimentación reducidas y una sincronización de sobrealimentación adecuada en el diseño del proceso. Acortar el ciclo de fundición a presión para minimizar las variaciones de temperatura.
- Reduzca el tiempo de inactividad y controle estrictamente el proceso de arranque de moldes en frío. El precalentamiento de moldes con una máquina de atemperado de moldes puede ayudar a estabilizar las fluctuaciones de temperatura durante el arranque.