El sistema de control de temperatura de un molde de inyección influye directamente en la calidad del producto moldeado y la eficacia de la producción. Las altas temperaturas en el mantigua cavidad puede provocar rebabas en la línea de separación y marcas de hundimiento en las secciones más gruesas de la pieza de plástico. Por el contrario, las bajas temperaturas pueden provocar un llenado deficiente y líneas de soldadura débiles. Las temperaturas desiguales en la cavidad del molde y las superficies móviles del molde pueden introducir tensiones internas, lo que provoca warpación y deformación en el proceso de moldeo. Por lo tanto, el sistema de control de la temperatura, similar al sistema de inyección, es crucial en el diseño del molde y merece mucha atención.
Principios de diseño para sistemas de refrigeración de moldes de inyección
Para mejorar la eficacia del sistema de refrigeración y garantizar una distribución uniforme de la temperatura en toda la cavidad del molde, deben respetarse los siguientes principios:
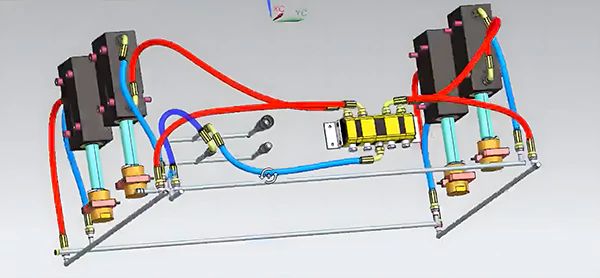
1. Método óptimo de refrigeración y colocación de circuitos:
Durante el diseño del molde, hay que dar prioridad al método de refrigeración y a la colocación del circuito, garantizando espacio suficiente para el flujo turbulento de agua en los canales de refrigeración. El circuito de refrigeración debe cumplir los requisitos del proceso de moldeo, proporcionando una refrigeración amplia, uniforme y equilibrada.
2. Diferencial de temperatura y dinámica del flujo:
Tenga en cuenta el diferencial de temperatura en la entrada y la salida y calcule la caída de presión del flujo para determinar el diámetro y la longitud adecuados de los canales de refrigeración. Procure que el diferencial de temperatura sea bajo (5°C para moldes estándar, 2°C para moldes de precisión). La longitud del circuito de refrigeración debe oscilar entre 1,2 y 1,5 metros, con una velocidad de flujo de 0-1,0 m/s, y el número de codos no debe superar los 15. Para moldes más grandes, considere la posibilidad de múltiples circuitos independientes para aumentar el flujo de refrigerante y reducir la pérdida de presión, mejorando la eficiencia de la transferencia de calor. Es preferible utilizar varios canales de refrigeración estrechos que un único canal de gran diámetro.
3. Número y tamaño de los canales de refrigeración:
Maximizar el número y el tamaño de los canales de refrigeración, cuyo diámetro depende de la forma de la pieza de plástico y de la estructura del molde. El número, el espaciado y la proximidad de los canales al espacio de moldeo influyen significativamente en el control de la temperatura del molde.
4. Enfriamiento estratégico cerca de la puerta:
La zona cercana a la compuerta, a menudo en contacto con la boquilla de la máquina de moldeo por inyección, tiende a tener temperaturas más elevadas y requiere una refrigeración intensificada. Si es necesario, diseñe un canal de refrigeración independiente para esta zona.
5. Evitar el enfriamiento en las líneas de soldadura:
Dado que las líneas de soldadura son las zonas más frías, evite colocar canales de refrigeración cerca de ellas para evitar agravar los defectos de las líneas de soldadura y reducir la resistencia de la pieza de plástico en estos puntos.
6. Colocación de las conexiones de entrada y salida de agua:
Coloque estas conexiones en el lado no operativo del molde.
7. Circuitos de refrigeración separados para moldes móviles y fijos:
Garantizar una refrigeración equilibrada tanto de la cavidad como del núcleo, prestando especial atención a la eficacia de refrigeración del núcleo para garantizar una refrigeración y contracción uniformes de la pieza de plástico.
Consideraciones clave en el diseño de sistemas de refrigeración
1. Métodos de enfriamiento para diferentes moldes:
Utilice el enfriamiento rápido para moldes estándar a fin de acortar el ciclo de moldeo y el enfriamiento gradual para moldes de precisión, incorporando termómetros de molde.
2. Minimizar el uso de anillos de sellado:
Diseñe circuitos de refrigeración con doble paso recto para facilitar el mantenimiento. Asegúrese de que las juntas sean estancas y compruebe si hay fugas de agua en las juntas y las boquillas.
3. Enfriamiento direccional para materiales específicos:
Para materiales como el PE con una contracción significativa, oriente los canales de refrigeración a lo largo de la dirección de contracción para evitar deformaciones. Alinee los canales con la disposición de la cavidad del molde.
4. Configuración del circuito de refrigeración:
Para moldes con una sola entrada y salida, utilice una conexión en serie para los canales de refrigeración. Para conexiones en paralelo, asegúrese de que cada circuito tenga un dispositivo de control de caudal y un caudalímetro para mantener unas condiciones de refrigeración uniformes.
5. Mejora de la refrigeración en zonas difíciles:
En las zonas en las que la refrigeración sea menos eficaz o esté limitada estructuralmente, considere la posibilidad de utilizar materiales con alta conductividad térmica, como el cobre de berilio o aleaciones de cobre, o una estructura de varillas conductoras del calor. Proporcione refrigeración a los núcleos, insertos y deslizadores según sea necesario.
6. Codificación por colores y etiquetado:
Marcar la entrada de agua con rojo y la salida con azul. Rotule las entradas y salidas de agua de refrigeración en las placas de molde móviles y fijas con "IN" y "OUT" en inglés, y agrupe los canales de agua en consecuencia.