Die casting molds are one of the four essential elements in die casting production (alongside casting materials, equipment, and processes). Cracking in the die casting mold cavity is a common and severe failure mode, directly impacting production scheduling. The primary causes of mold cavity cracking include direct contact with high-temperature metal liquids, erosion during the filling stage by high-speed flowing metal, and the impact of high pressure during the pressurization stage. Additionally, the severe fluctuation of mold steel temperature in each casting cycle contributes to this issue.
A proficient die casting company embraces the challenges in various processes. Addressing and resolving different process issues enriches manufacturing experience, enabling the production of satisfactory parts for diverse clients.
Factors Related to Die Casting Mold Cracking
1.1 Mold Design
1.1.1 Material Selection
For the forming parts of die casting molds, specific hot work mold steels are commonly chosen. Grades like 1.2343 and 1.2344 are suitable for large molds, while 1.2367 is preferred for parts where erosion is severe. However, due to processing difficulty and hardenability issues, 1.2367 is not ideal for very large forming parts. It’s recommended to use high-grade varieties processed with electroslag remelting technology, as they have lower impurity content and less variation between core and surface, reducing the risk of cracking.
Model | High-Temperature Strength | High-temperature toughness | High-temperature wear resistance | Machinability |
1.2343/8402/H11/SKD6 | ⭐⭐ | ⭐⭐⭐⭐ | ⭐⭐ | ⭐⭐⭐⭐⭐ |
1.2344/8407/H13/SKD61 | ⭐⭐⭐ | ⭐⭐⭐ | ⭐⭐⭐ | ⭐⭐⭐⭐ |
1.2367/8418 | ⭐⭐⭐⭐ | ⭐⭐⭐⭐ | ⭐⭐⭐⭐ | ⭐⭐⭐ |
1.1.2 Product Geometric Shape
Common risks include:
- a. Deep groove structures with small draft angles or excessive length-to-diameter ratios;
- b. Insufficient local radii causing stress concentration;
- c. Inadequate draft angles in areas eroded by molten aluminum;
All of these common risks need to be improved from a product design perspective, as follows
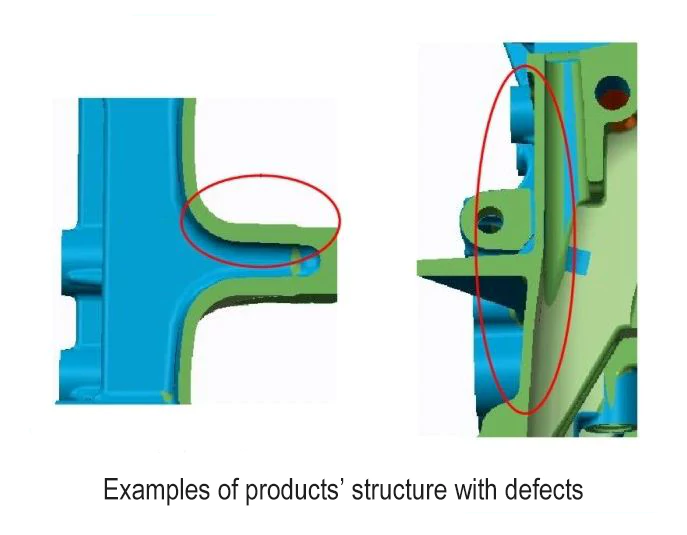
1.1.3 Mold Geometric Shape
Common risks include:
- a. Insufficient local radii leading to stress concentration;
- b. Sharp angles and knife edges caused by insert structures;
- c. Weak structures in mold filling channels;
All of these common risks need to be avoided from a parting design perspective.
1.1.4 Gating System Design
Common risks include:
- a. Insufficient radii in gate design;
- b. Gates facing weak structural areas;
These common risks need to be avoided from the gating system design point of view, see the following figure:
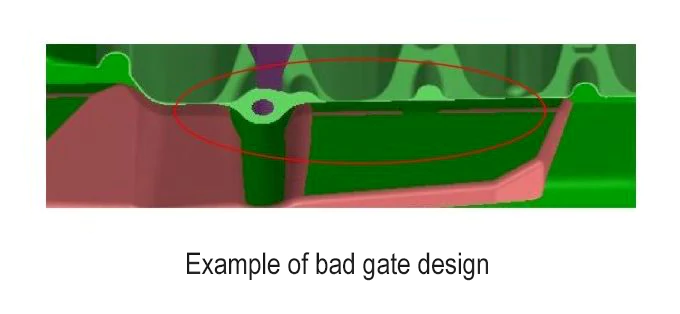
1.1.5 Cooling System Design
Common risks include:
- a. Excessively deep cooling holes leading to insufficient local strength;
- b. Poor cooling layout causing significant temperature distribution differences and stress;
These common risks need to be balanced from a cooling system design perspective, as below:
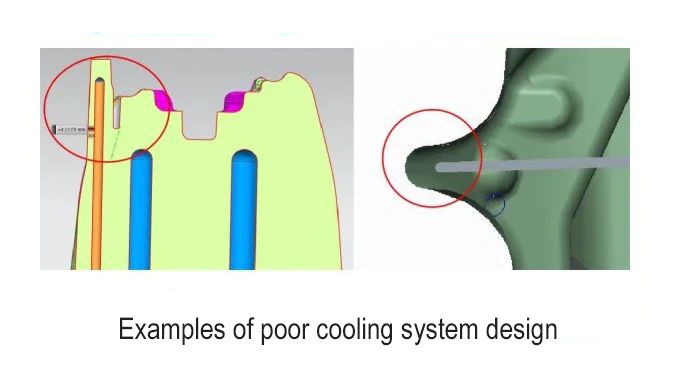
1.2 Mold Manufacturing
1.2.1 Material Control
As per the North American Die Casting Association (NADCA) standards, high-quality materials from mainstream suppliers typically meet or exceed these standards, reducing the likelihood of defects.
1.2.2 Machining Methods
Electrical Discharge Machining (EDM) can affect the surface composition and structure of the mold, leading to micro-cracks and stress concentration. Minimizing the use of EDM can significantly reduce the risk of mold cracking.
1.2.3 Machining Parameters
Adhering to the recommended machining parameters for the selected material, such as cutting speed, feed per revolution, cutting depth, and tool type, is essential. Deviating from these guidelines can result in residual stress and potential stress cracks.
1.2.4 Stress Relief Grinding
EDM is often unavoidable in large die casting mold processing. Post-EDM, it’s crucial to grind and polish the affected areas as per the material guidelines to remove harmful structures and alleviate stress.
1.2.5 Heat Treatment Process
The heat treatment of mold materials includes softening, stress relieving, and hardening. Following the detailed requirements for quenching media, cooling rate, and tempering intervals in the material guidelines ensures the internal and external structure of the material meets expectations.
1.2.6 Nitriding Control
Nitriding enhances the mold’s surface wear resistance, delaying the erosion caused by molten aluminum. However, it also makes the surface more brittle and increases the risk of cracking. The depth and conditions of nitriding must be strictly controlled, especially for large parts (0.03-0.07 depth).
Process Design and Its Impact
1.3.1 Hot Mold Process
The method of starting production with a cold mold greatly affects the life of the mold, especially due to thermal stress caused by alternating cold and hot impacts. It’s recommended to preheat the mold using a mold temperature machine rather than starting directly with a low-pressure hot mold. During a cold mold start, typically 5-10 low-pressure, low-speed injection cycles are needed to raise the mold temperature. Therefore, it’s crucial to avoid initiating high-speed, high-pressure injection cycles too early.
1.3.2 Cooling Techniques
The chosen cooling process in production significantly impacts the thermal stress on the mold surface. This is evident in the maximum and minimum temperature differences during the die casting cycle and on the mold surface. The former often leads to cracking and crack development, while the latter can cause stress cracks.
A good cooling process should consider controlling the cooling water time, cooling during the solidification stage, and avoiding constant cooling throughout the cycle. It’s also important to control the temperature drop from spraying and rely less on spraying for cooling. Ensuring a compact cycle time is crucial to avoid large fluctuations in mold temperature differences within the cycle.
1.3.3 Injection Speed
Erosion from molten aluminum significantly damages the mold. A lower gate speed is more beneficial for mold life. To balance filling quality, it’s advised to keep the gate filling speed within 30-50m/s. If possible, try to control the filling speed of each branch gate below 45m/s.
1.3.4 Boost Pressure
Reducing casting pressure is beneficial for extending mold life. The recommended injection pressure should be below 100MPa. Choosing the right timing for boosting pressure is also crucial for mold longevity, so avoid boosting too early or too late.
Maintenance and Care for Prolonging Mold Life
1.4.1 Production Scheduling Habits
Production scheduling habits significantly affect mold life, mainly due to temperature fluctuations caused by intermittent production. Continuous 24-hour production leads to a dynamic equilibrium in mold temperature, reducing the temperature difference in each cycle and across different mold areas. Intermittent production, leading to frequent cold mold startups, increases thermal stress, causing cracks and crazing, negatively impacting mold life.
1.4.2 Mold Spot Checks
Timely removal of aluminum adhesion on the mold surface can reduce demolding resistance and delay crack development. For areas severely eroded by molten aluminum, electro-discharge coating is recommended to enhance local wear resistance and delay the onset and development of crazing.
1.4.3 Mold Maintenance
Periodic stress-relief annealing can eliminate thermal stress to some extent. Cleaning the mold surface of aluminum adhesion and dirt reduces erosion. Regular checks for proper mold closing can prevent excessive squeezing and damage during operation.
Conclusion and Preventative Measures
To prevent die casting mold cracking, it’s essential to:
- Minimize occurrences of sharp angles, insufficient fillets, and inadequate draft angles in mold design. Collaborate with product design early to mitigate risks.
- Be cautious in selecting steel materials with poor through-hardening properties for large molded parts. Avoid excessively high hardness and deep nitriding layers to prevent significant hardness differences within the workpiece.
- Opt for lower gate speeds, reduced boost pressures, and appropriate boosting timing in the process design. Shorten the die casting cycle to minimize temperature variations.
- Reduce downtime and strictly control the cold mold startup process. Preheating molds with a mold temperature machine can help stabilize temperature fluctuations during startup.