El diseño de moldes de engranajes, especialmente para engranajes de plástico, difiere significativamente de los diseños de moldes tradicionales. Parámetros clave como el grosor del diente (la longitud de arco entre dos lados de un diente de engranaje), el módulo (un parámetro que mide el tamaño del engranaje) y el ángulo de presión (el ángulo agudo entre la dirección de la fuerza y la dirección del movimiento, excluyendo la fricción) requieren ajustes basados en datos empíricos.
A diferencia de otros procesos, los moldes de engranajes no pueden procesarse directamente basándose en los índices de contracción. Los fabricantes profesionales de engranajes y cajas de engranajes, aprovechando su larga experiencia y la colaboración con empresas de software informático, han desarrollado software especializado para calcular los parámetros de las cavidades de los moldes de engranajes. Este software puede generar directamente parámetros y perfiles de engranajes, ayudando en la modificación de los engranajes y mejorando la precisión de los dientes. Profundicemos en los entresijos del diseño de moldes para engranajes de plástico.
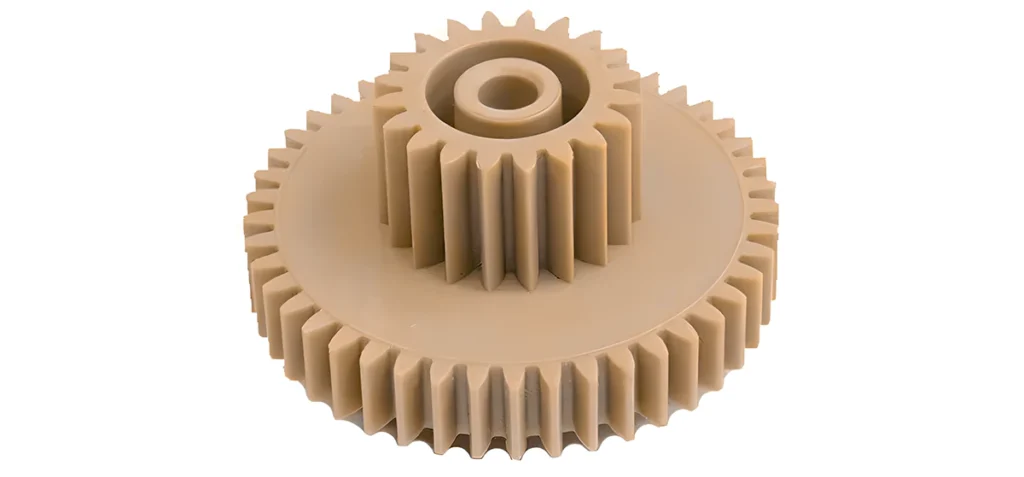
Diseño de cavidades para moldes de engranajes de plástico
El diseño de la cavidad para un molde de engranaje de plástico siempre ha sido un reto técnico en la industria del molde, debido principalmente a dos razones:
1. Precisión en los índices de contracción del plástico:
Durante el proceso de moldeo de engranajes de plástico, los gránulos de plástico se transforman en un estado fundido bajo un calor elevado y luego se enfrían para formar engranajes de plástico sólidos. El índice de contracción del plástico durante este proceso es un valor de rango, lo que dificulta la determinación de índices de contracción precisos.
2. Cálculo no lineal de la contracción en cavidades de moldes:
Para los moldes de engranajes de plástico de módulo pequeño evolventes, la cavidad del molde representa esencialmente un engranaje imaginario. Este engranaje imaginario difiere tanto de los engranajes desplazados como de los engranajes internos. Tras la contracción, se convierte en el engranaje de plástico deseado. La contracción en el perfil del diente evolvente de este engranaje imaginario no es uniforme como la contracción isotrópica que se observa en las piezas de plástico en general. En el plano del engranaje, la contracción en las direcciones x e y es desigual, lo que da lugar a una contracción no lineal, como se muestra en la figura 1. Esta no linealidad aumenta significativamente la resistencia a la deformación. Esta no linealidad aumenta significativamente la complejidad del diseño de cavidades de moldes de engranajes de plástico evolventes.
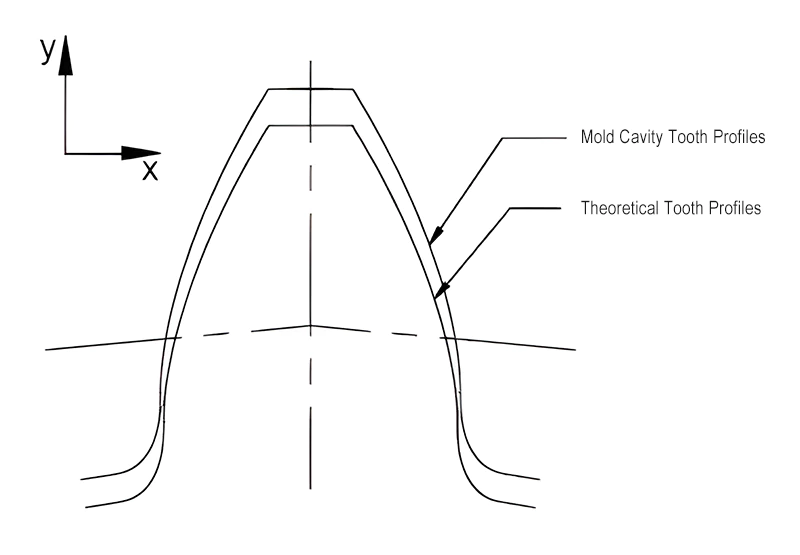
La forma correcta de diseñar la cavidad de un molde para engranajes
Frente a estos retos técnicos, la utilización del método de contracción isotrópica para el diseño de cavidades de moldes suele arrojar resultados subóptimos. Basándonos en años de experiencia práctica y en una estimación precisa de los índices de contracción plástica, recomendamos utilizar el método de módulo variable para el diseño teórico de cavidades de moldes de engranajes, seguido de la corrección del perfil del diente para garantizar la precisión y la racionalidad de la cavidad del molde.
El método de módulo variable parte de la base de que, durante las distintas fases de mecanizado, el diámetro del círculo de base, el diámetro del círculo de paso, el diámetro del círculo de adición y el diámetro del círculo de deducción de un engranaje se mantienen constantes, aumentando o disminuyendo proporcionalmente, de forma similar a los cambios de dimensión radial en piezas simples tipo manguito. El círculo primitivo de un engranaje, determinado por la fórmula d=mz, sólo depende del módulo m y del número de dientes z.
Dado que el número de dientes de un engranaje concreto es constante, podemos considerar el cambio del diámetro del círculo primitivo durante el procesamiento como un cambio del módulo. Este principio implica que el espacio que abarca la cavidad del molde de engranajes de plástico es un engranaje imaginario con número de dientes y ángulo de presión constantes, cuyas ranuras forman el perfil dentado de la cavidad.
Podemos calcular el módulo de este engranaje imaginario utilizando un método proporcional. La fórmula para este cálculo es m' = (1 + η%)m. En esta fórmula, m' representa el módulo del perfil del diente de la cavidad del molde, m es el módulo teórico del engranaje diseñado, y η% es la tasa de contracción del plástico. Sustituyendo el módulo m' en la fórmula de cálculo del engranaje correspondiente, el engranaje resultante representa el engranaje imaginario de la cavidad del molde. La práctica ha demostrado que el método del módulo variable aborda eficazmente el reto de la contracción no lineal en los perfiles de dientes evolventes, como demuestra el producto de la cavidad del molde que se muestra en la figura 2.
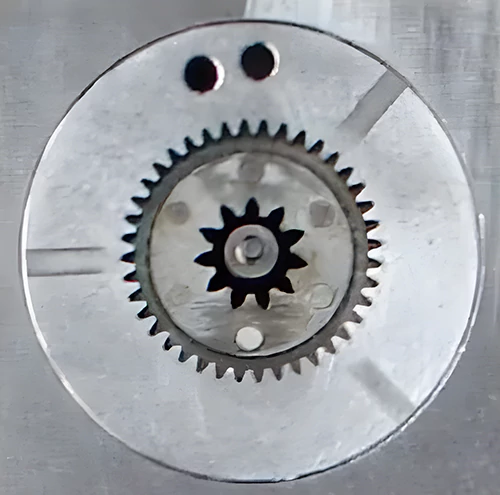
Diseño de compuertas para moldes de engranajes de plástico
En el proceso de moldeado de engranajes de plástico, la ubicación de la compuerta influye significativamente en la precisión de los engranajes, especialmente en su excentricidad radial. La forma de distribución de la compuerta también afecta de manera crucial a las propiedades mecánicas generales de los engranajes de plástico. Cuando se diseñan compuertas para moldes de engranajes de plástico, si el producto lo permite, se recomienda utilizar un sistema de compuerta de tres puntos. Lo ideal es que estos tres puntos estén situados en el mismo arco circular y distribuidos uniformemente, como se muestra en la figura 3.
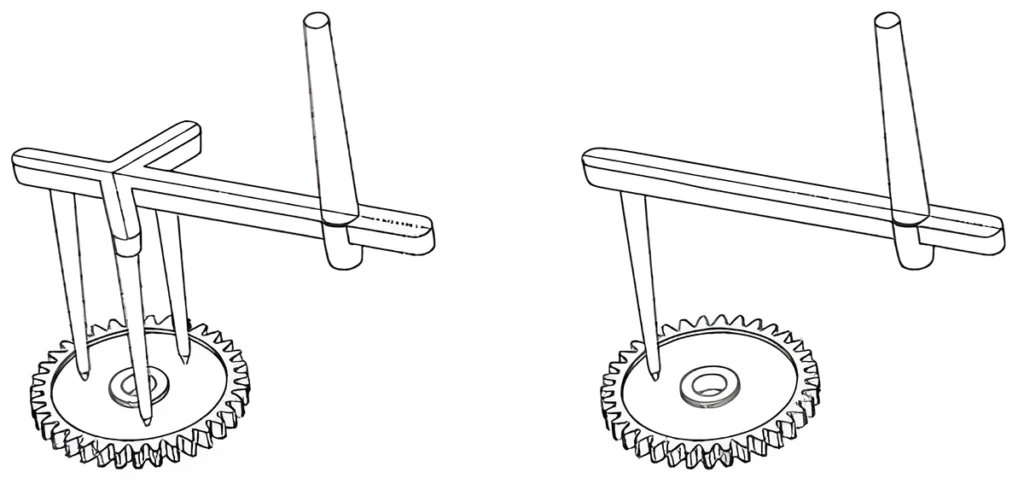
Utilizando un sistema de compuertas equilibrado en tres puntos, la masa fundida de plástico fluye radialmente desde las compuertas, convergiendo en los frentes de flujo para formar tres líneas de soldadura. En estas líneas de soldadura, la orientación de las fibras tiende a ser paralela al frente de flujo. En los engranajes, esto hace que las fibras se distribuyan radialmente en las líneas de soldadura, mientras que se distribuyen aleatoriamente en otras partes del engranaje. Esto crea zonas de baja contracción a lo largo de las líneas de soldadura. La diferencia de orientación de las fibras entre las líneas de soldadura y el resto del engranaje es menos pronunciada que en los engranajes con una sola compuerta, lo que se traduce en una mayor precisión del engranaje. La figura 4 muestra una comparación esquemática de la orientación de las fibras y los patrones de relleno cuando se utiliza una única compuerta excéntrica frente a una compuerta de tres puntos distribuida uniformemente.
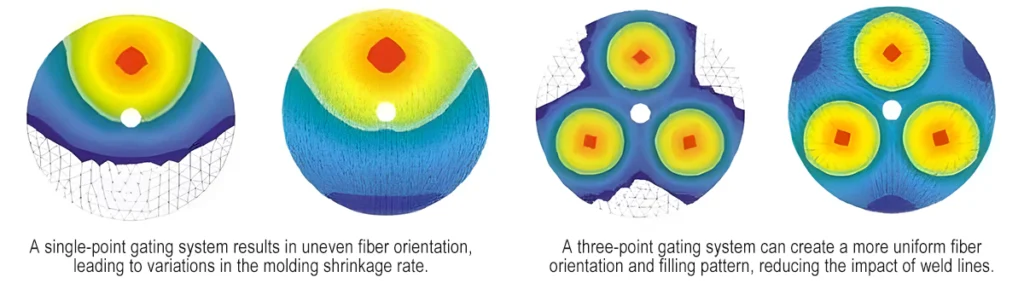
Diseño de ventilación para moldes de engranajes de plástico
La ventilación es un aspecto crucial a tener en cuenta en el diseño de moldes de plástico. En el caso de los moldes de plástico para engranajes, el diseño de la ventilación en las superficies de los dientes es especialmente importante. Mecanizamos la mayoría de las superficies de los moldes de engranajes con una rectificadora. Este proceso garantiza un buen ajuste entre superficies. Sin embargo, tiende a provocar un llenado insuficiente en las últimas zonas durante el proceso de inyección. Para eliminar el aire atrapado, es necesario crear ranuras de ventilación en las superficies de los dientes. Por lo general, el diseño de estas ranuras de ventilación en las superficies de los dientes es el que se muestra en la figura 5.

Diseño estructural de moldes para engranajes de plástico
Dado que el moldeo por inyección de engranajes de plástico a menudo utiliza puertas puntuales, la estructura del molde suele adoptar un diseño de tres placas. La figura 6 muestra el diagrama de diseño de un molde de engranaje, y la figura 7 muestra el molde de engranaje real. El principio de funcionamiento del molde de engranajes es el siguiente:
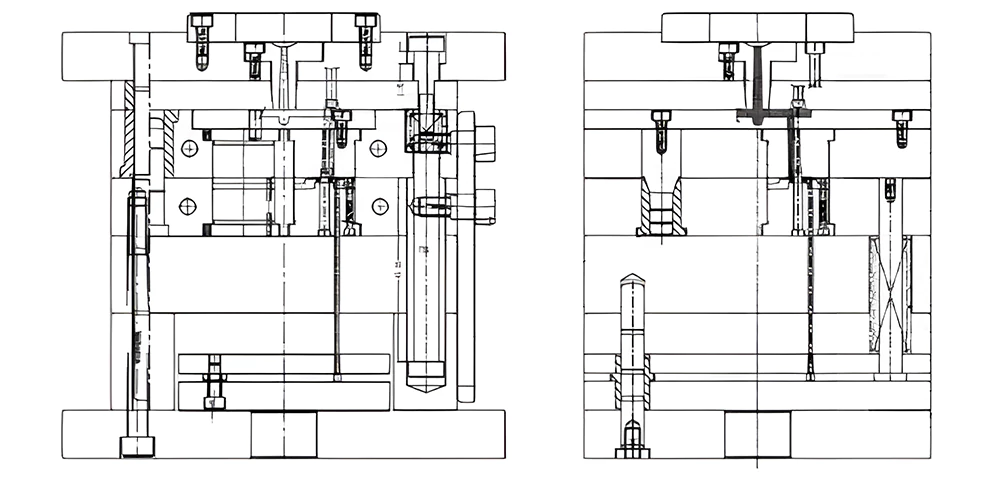
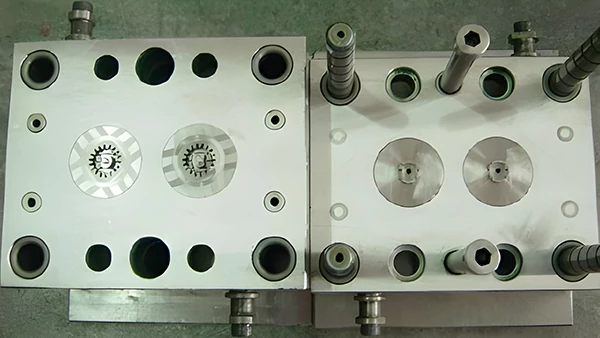
Después de completar la acción de moldeo por inyección, la parte móvil del molde comienza a abrirse bajo el accionamiento de la máquina de moldeo por inyección:
- Primera etapa de la despedida: Debido a la acción del muelle 1, la placa separadora comienza a separarse de la placa A. La acción del pasador de tracción del bebedero fija el canal principal en la placa separadora y hace que la compuerta se separe del producto.
- Segunda fase de Despedida: Después de que el molde se abra 95 mm, bajo la acción del conjunto de la barra de unión, la placa separadora comienza a separarse de la placa frontal, liberando el canal principal del casquillo del bebedero.
- Tercera fase de Despedida: A medida que el molde continúa abriéndose, bajo la acción del conjunto de barras de unión, la placa A comienza a separarse de la placa B. Tras abrirse hasta 90 mm, la placa eyectora comienza a moverse, expulsando el producto. Durante este proceso, los postes guía de la placa eyectora se utilizan para mejorar el equilibrio de la expulsión. La placa eyectora se restablece bajo la acción del muelle 2. De este modo se completa toda la acción de apertura y expulsión del molde.
Fabricación de moldes de plástico para engranajes
En el proceso de moldeado de engranajes de plástico, el molde de engranajes es el equipo clave para dar forma a los engranajes de plástico y garantizar su precisión. El molde de engranajes de plástico puede dividirse en dos partes principales: la cavidad del engranaje y el marco del molde. La cavidad del engranaje, también conocida como anillo del engranaje, es la parte más crítica y que exige mayor precisión de todo el proceso de fabricación del molde de engranajes.
1. Mecanizado de cavidades de engranajes
El mecanizado de la cavidad del engranaje es clave en la fabricación de moldes de plástico para engranajes. El moldeo de engranajes de plástico es una forma de procesamiento de "réplicas". En este proceso, el perfil del diente de la cavidad es una plantilla deformada de la forma del diente del engranaje. Por lo tanto, es esencial controlar estrictamente la precisión dimensional y la rugosidad de la superficie de la cavidad. Es esencial evitar defectos como rebabas, excentricidad y arañazos superficiales. Por lo tanto, debe establecerse un estricto proceso de mecanizado de la cavidad del engranaje para garantizar la precisión de la producción de la cavidad.
Existen principalmente cuatro métodos para mecanizar la cavidad del engranaje: corte por hilo, mecanizado por descarga eléctrica (EDM), electroconformado y fundición de aleación de cobre berilio. Cada uno de estos métodos tiene sus ventajas e inconvenientes para el mecanizado de cavidades de engranajes. Los fabricantes suelen utilizar el corte por hilo para los engranajes cilíndricos rectos evolventes y generalmente prefieren la electroerosión para los engranajes helicoidales. Además, pueden mecanizar los electrodos utilizados para la electroerosión de cavidades de engranajes mediante corte por hilo. Para electrodos de engranajes helicoidales con un ángulo de hélice pequeño (β≤6°), el corte por hilo sigue siendo aplicable.
2. Mecanizado del marco del molde
El marco del molde, también conocido como base del molde, es una pieza auxiliar de conformación del molde de engranajes. El proceso de mecanizado del marco del molde es similar al de los moldes de inyección de plástico comunes. Por lo tanto, en este artículo no se tratará en detalle. La figura 8 muestra la imagen real del mecanizado del marco del molde de engranajes.
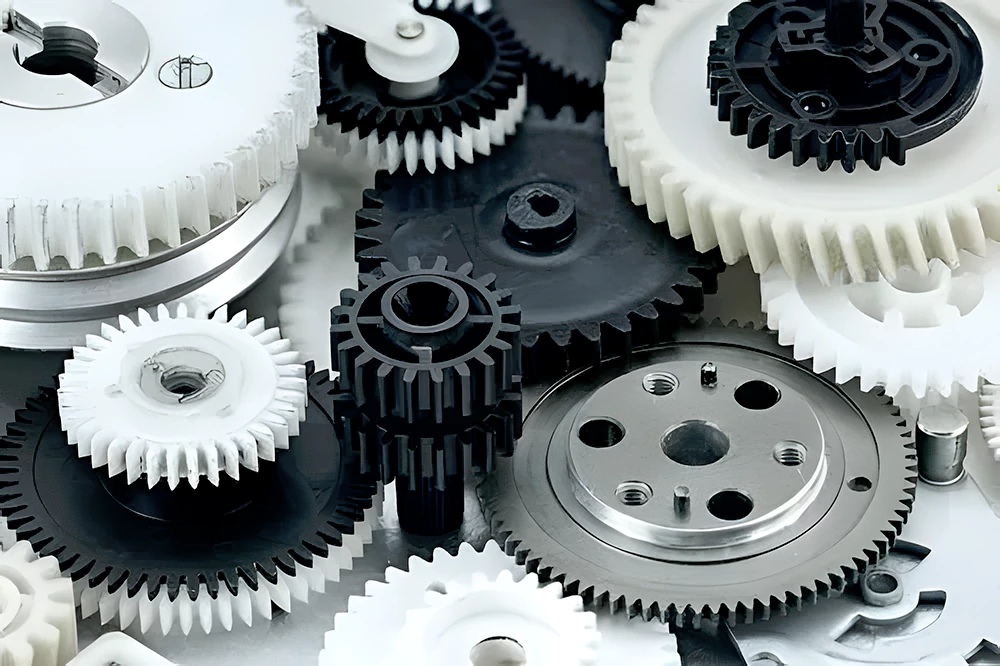