L'épaisseur de la paroi de produits en plastique moulés par injection a un impact significatif sur leur qualité. Si l'épaisseur de la paroi est trop fine, il sera difficile de répondre aux exigences de résistance et de rigidité et de remplir la cavité pour les produits grands et complexes. Une paroi trop épaisse entraîne non seulement un gaspillage de matière première, mais aussi la formation rapide de bulles à l'intérieur des produits en plastique, ce qui se traduit par les problèmes suivants défauts comme les dépressions dans l'apparence du produit. En même temps, le temps de refroidissement s'en trouve allongé. Par conséquent, d'un point de vue économique, il est essentiel d'amincir un produit en plastique.
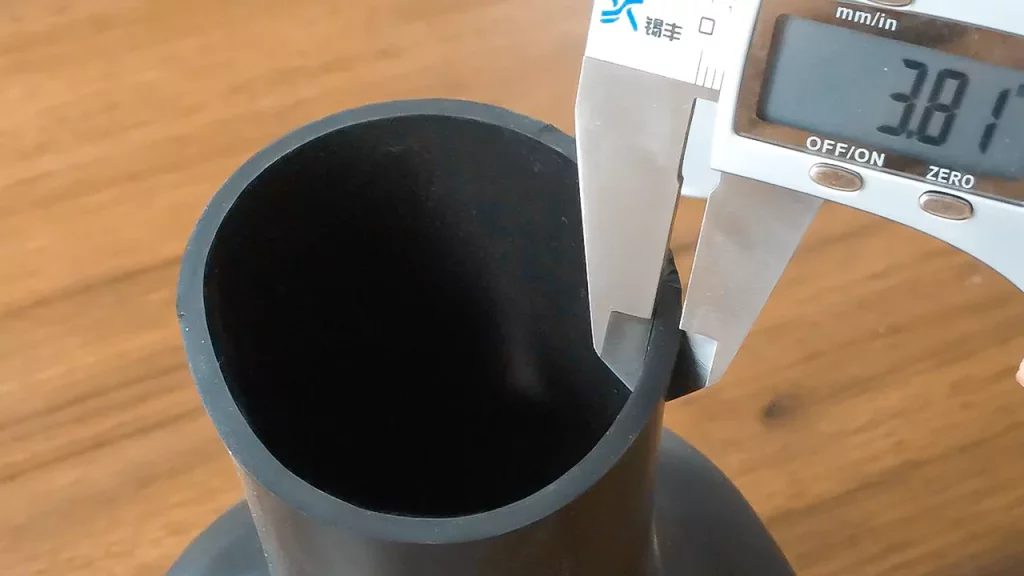
Lors de la construction d'un moule d'injection plastiqueL'épaisseur du produit plastique doit être adaptée aux exigences du processus de moulage. Si le produit est trop fin, la résistance à l'écoulement pendant l'injection est élevée, le moulage par injection est complexe et la cavité ne peut pas toujours être remplie. Si le produit est trop épais, il gaspille des matières premières, allonge le cycle de moulage et génère rapidement des défauts tels que des bulles, des bosses et des déformations.
Voyons cela plus en détail.
Épaisseurs de paroi couramment utilisées dans les produits en plastique :
Il est recommandé que les articles en plastique courants aient une épaisseur de paroi de 1-6mmavec un maximum de 8 mm. L'épaisseur de paroi la plus courante est de 1,8-3mmqui varie en fonction du type et de la taille de l'élément en plastique. Afin de connaître facilement l'épaisseur de la paroi, les spécifications des épaisseurs de paroi couramment utilisées dans différents contextes de moulage par injection de matières plastiques sont indiquées dans le tableau ci-dessous.
Tableau : Épaisseurs de paroi recommandées et minimales pour les pièces thermoplastiques courantes (mm)
Matière plastique | Épaisseur min. Épaisseur | Épaisseur recommandée pour les pièces en plastique de petite taille | Épaisseur recommandée pour les pièces en plastique de taille moyenne | Épaisseur recommandée pour les pièces en plastique de grande taille |
PA | 0.45 | 0.75 | 1.60 | 2.40~3.20 |
PE | 0.60 | 1.25 | 1.60 | 2.40~3.20 |
PS | 0.75 | 1.25 | 1.60 | 3.20~5.40 |
PMMA | 0.80 | 1.50 | 2.20 | 4.00~6.50 |
POM | 0.80 | 1.40 | 1.60 | 3.20~5.40 |
PP | 0.85 | 1.45 | 1.75 | 2.40~3.20 |
PC | 0.95 | 1.80 | 2.30 | 3.00~4.50 |
PSF | 0.95 | 1.80 | 2.30 | 3,00~4.50 |
UPVC | 1.15 | 1.60 | 1.80 | 3.20~5.80 |
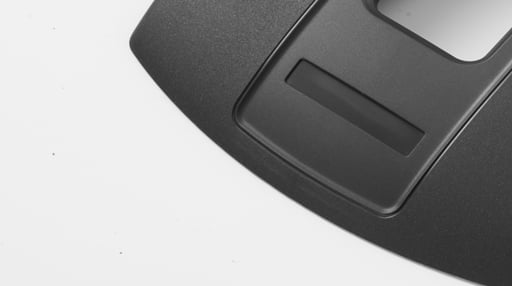
Avantages d'une épaisseur de paroi idéale pour les produits en plastique :
Les parois plus épaisses pour offrir une résistance supplémentaire sont opposées aux parois plus minces pour offrir certains autres avantages. Le maintien d'une pièce plus fine et plus légère permet d'obtenir des avantages supplémentaires lorsque la production est plus longue. Par conséquent, le maintien d'une épaisseur optimale est essentiel, en particulier lorsque vous entreprenez des projets de moulage par injection de plastique avec un volume de production élevé. Si vous maintenez la paroi aussi fine que possible, vous bénéficierez des avantages suivants :
- Meilleure résistance au gauchissement pendant le processus de refroidissement
- Le poids total réduit facilite la manipulation, la gestion, l'emballage et l'expédition.
- Moins de temps passé à refroidir, ce qui permet une production plus rapide et plus efficace
- Réduction des coûts grâce à une consommation moindre de matériaux et à une production plus rapide
L'épaisseur de la paroi d'une pièce n'est soumise à aucune contrainte. Toutefois, l'objectif ultime devrait être de créer une paroi aussi fine que possible tout en tenant compte des exigences structurelles, des dimensions globales et de la géométrie de la pièce. Cet objectif doit être atteint tout en préservant l'intégrité de la pièce. Un autre facteur essentiel à prendre en compte est celui des caractéristiques d'écoulement et des qualités des matériaux en résine.
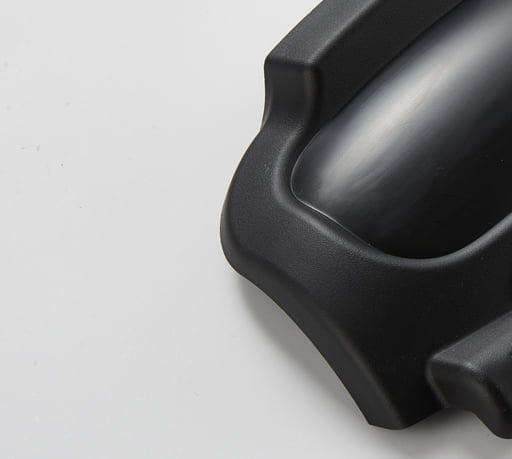
Qu'est-ce qui affecte la conception de l'épaisseur de la paroi des produits en plastique ?
Les exigences d'une application déterminent la structure fondamentale d'un produit plastique, que le fabricant détermine ensuite. Le choix de la matière première influence l'épaisseur totale du produit. Par conséquent, lors de la conception de produits en plastique à parois épaisses dans des conditions typiques, deux éléments doivent être pris en compte, à savoir les conditions d'application et les conditions de production du plastique. La structure, le poids, la résistance et les qualités d'isolation sont des conditions d'application ; les conditions de fabrication du plastique comprennent la fluidité du matériau, le temps de refroidissement, la force d'éjection, la résistance de l'assemblage, l'exactitude des dimensions et d'autres facteurs. Pour plus d'informations, voir les trois points ci-dessous :
- Caractéristiques de la structure :
La structure de base d'un produit en plastique se réfère principalement à sa forme et à sa taille, déterminées par les critères imposés au produit par l'application à laquelle il est destiné. Lorsqu'une pièce métallique est remplacée par une pièce en plastique ou lorsqu'une nouvelle pièce en plastique est conçue, vous devez modifier la structure et l'épaisseur de la paroi de la pièce métallique pour vous conformer au principe d'uniformité de l'épaisseur de la paroi du produit en plastique. En effet, le principe d'uniformité de l'épaisseur de la paroi du produit en plastique s'applique aux pièces métalliques. caractéristiques de rétrécissement L'épaisseur du plastique lors du moulage par injection diffère de celle du métal. Il est recommandé d'évider le composant à paroi épaisse et de l'ajuster de manière à ce que l'épaisseur de la paroi soit constante.
Après avoir été fondues au cours du processus de moulage par injection, les matières plastiques ont une certaine fluidité. Cette fluidité varie toutefois considérablement en fonction des différents types et qualités de plastique. Les facteurs suivants influencent la fluidité des plastiques : généralement, l'indice d'écoulement à chaud (MFI) et le test d'écoulement en spirale d'Archimède sont utilisés pour évaluer la fluidité des plastiques. En général, un indice de fluidité plus élevé indique une plus grande fluidité. Toutefois, ce n'est que parfois le cas.
Par conséquent, l'épaisseur de la paroi des divers produits à base de matériaux doit être conçue de manière à favoriser le plus possible la fluidité. Cela garantit un remplissage adéquat de la cavité, une vitesse d'écoulement du plastique fondu uniforme dans toutes les directions et une résistance minimale dans le sens de l'écoulement. Des parois plus minces peuvent être conçues pour les plastiques à haute fluidité, tels que le nylon, le polyéthylène et le polypropylène. L'épaisseur de la paroi peut être augmentée pour les polymères à faible fluidité, tels que le PC et le PSF. Il en résulte une plus grande intégrité structurelle.
- Facteurs contribuant à la solidité des produits :
Les propriétés physiques et mécaniques de la matière première, combinées à des exigences structurelles spécifiques, déterminent la résistance à la traction d'un produit en plastique. Par rapport au métal, le plastique est mécaniquement plus faible, plus fragile, moins résistant aux chocs et plus léger ; il convient donc d'accorder une attention particulière à la conception de l'épaisseur des parois des produits en plastique afin de répondre aux exigences de résistance. Bien que l'application d'un produit ne nécessite parfois qu'une faible résistance, celui-ci doit résister aux chocs et aux vibrations du mécanisme d'éjection lorsqu'il est libéré de l'appareil. cavité du moule. Il est donc nécessaire de s'assurer que le produit présente une certaine résistance à la force d'éjection.
Impact d'une épaisseur de paroi non uniforme :
- Taux de refroidissement :
Différentes épaisseurs de paroi de moulage par injection peuvent également affecter les vitesses de refroidissement. Comme les parties plus épaisses prennent plus de temps à durcir, la pièce entière doit rester dans l'outil jusqu'à ce qu'elle ait suffisamment refroidi pour être éjectée. Bien que cela ne pose pas de problème de qualité, la durée du cycle s'en trouve allongée. Il serait plus efficace de refroidir l'ensemble de la pièce dans le même laps de temps.
- Défis en matière d'accès :
Lors de l'encapsulation d'une pièce moulée par injection, il est essentiel de commencer par la zone la plus épaisse et de descendre ensuite. Cela est nécessaire pour emballer correctement la pièce après l'avoir remplie. La ligne d'écoulement de la matière fondue doit rester ouverte pendant le processus de refroidissement afin que le plastique puisse continuer à s'écouler dans les détails de la pièce. Des irrégularités d'écoulement peuvent résulter de l'entrée dans une paroi mince ou de l'écoulement à travers une section mince pour acheminer le matériau vers une zone plus épaisse. La partie la plus fine peut geler et se solidifier, empêchant ainsi la matière d'atteindre la partie épaisse de la pièce pendant la phase d'emballage. En raison des circonstances de sous-emballage dans la partie épaisse, cela peut induire une augmentation du retrait, ce qui se traduit par une augmentation de l'épaisseur de la pièce. évier et/ou se déformer en partie.
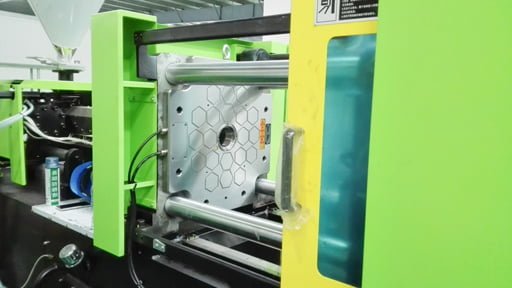
- Apparence :
L'un des effets les plus visibles de la modification de l'épaisseur de la paroi est la façon dont elle modifie l'apparence de l'objet moulé par injection. Une épaisseur de paroi variable peut entraîner des retombées indésirables et des difficultés visuelles telles que des lignes d'écoulement. Il peut également être difficile de maintenir le contact de la cavité pour le refroidissement et d'obtenir la brillance ou la texture de la surface de la cavité.
- Contrainte de cisaillement :
Une épaisseur de paroi non uniforme peut également affecter la contrainte de cisaillement dans le plastique en écoulement. Les régions minces obligent l'écoulement à se déplacer plus rapidement à un taux de remplissage constant, ce qui génère une contrainte de cisaillement. Le gauchissement est causé par des degrés variables de contrainte de cisaillement sur une portion. Cette contrainte de cisaillement contribue également à orienter les renforts en fibres. Les fibres sont sensiblement plus rigides dans le sens de l'écoulement qu'à 90 degrés par rapport à l'écoulement, et le changement de rigidité peut également provoquer un gauchissement.
Conclusion :
En résumé, pour éviter que des problèmes d'épaisseur de paroi non uniforme ne surviennent pendant et après la production de produits en plastique par le biais du processus de moulage par injection, vous devriez faire confiance à un professionnel pour vous aider dans la production. Pour plus d'informations et de détails, n'hésitez pas à consulter notre site web. techniciens professionnels à Prototool.