As complicated as it may appear to the average customer, plastic injection molding processing is a typical manufacturing technique used to make a wide range of commonplace objects. Various plastic injection molding companies like Prototool offer this service to assist in the manufacturing of plastic objects that have become a part of our daily lives, regardless of their complexity, craftsmanship, size, or dimensions.
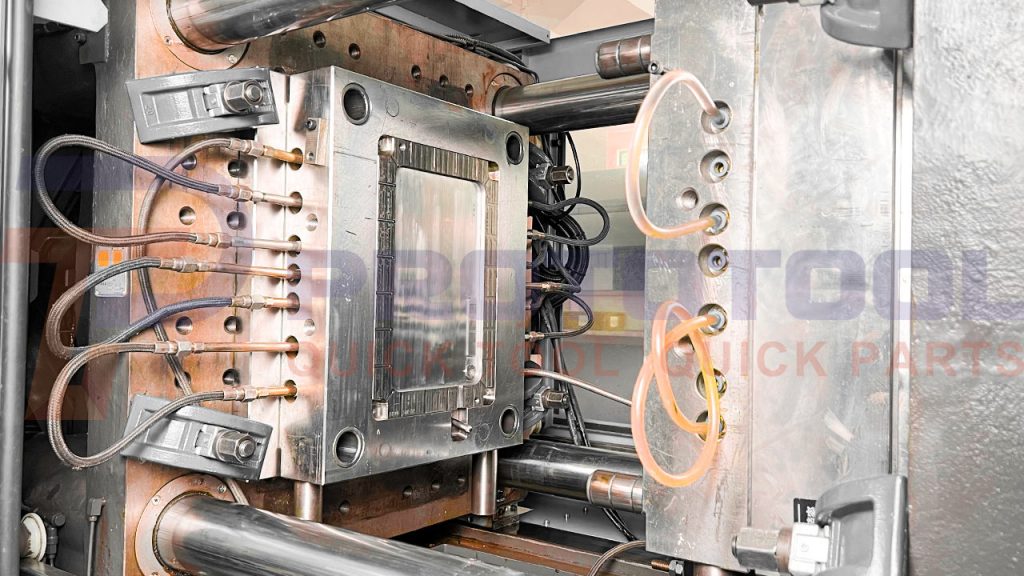
Now for anyone opting to invest in such a service without any know-how about plastic injection molding, this detailed guide will enlighten you with all the essential details. So without further ado, let’s dive into the details of this efficient manufacturing process.
Process Characteristics
The processing of a plastic injection molding machine begins with the injection of plastic into the mold, followed by continuous rotation and heating along the two vertical axes. Under the influence of gravity and heat, the plastic in the injection mold is uniformly covered, melted, and attached to the whole cavity surface. Eventually, the desired plastic shape is then obtained by cooling and setting the material.
For a more precise idea, below are the characteristics of a plastic injection mold that should be considered for attaining quality outcomes through the plastic injection molding process.
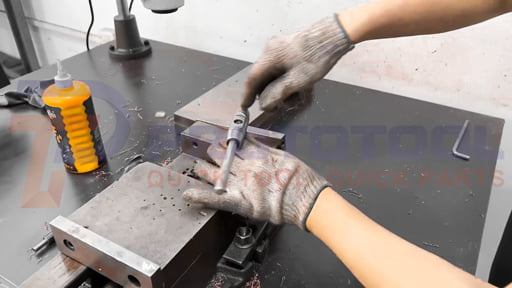
- The production of plastic injection molds is not mass-produced in large quantities. Instead, to complete the appropriate processing of plastic components, it is frequently essential to produce a pair of plastic injection molds.
- In the creation of plastic injection molds, it is vital to do profile processing in accordance with the actual object in an attempt to ensure that the plastic injection mold is highly precise and not distorted.
- Various procedures are involved in producing plastic injection molds used for custom plastic injection molding. These procedures include milling, drilling, reaming, and tapping.
- The usage life of plastic injection molds is also limited. Therefore, when the life of a pair of plastic injection molds ends, we must replace them. Due to this reason, the production of plastic injection molds is frequently repetitious.
- Some plastic products, such as automotive covers, aviation parts, toys, and home appliances, have curved surfaces. However, since the cavity surface of a plastic injection mold is intricate, the production of products with these kinds of surfaces should be handled using mathematical formulas.
- The ideal and standard material used for producing plastic injection molds is high-quality alloy steel. What makes this material for proceeding with the plastic injection molding process is its long-lasting quality, especially during the heat treatment deformation process that the mold goes through during the injection molding process.
Equipment: What They Are and How They Work?
There is a wide array of equipment involved in the injection molding process. And when it comes to injection molding, whether it is of plastic or metal, the types of equipment used in this process are pretty similar. However, if any of the essential equipment isn’t present, it can be said that the plastic injection molding processing may not proceed efficiently and produce the ideal plastic product that you need. Needless to say that professional injection molding service-providing companies do comprise all the essential types of equipment for handling the production process as per your demands.
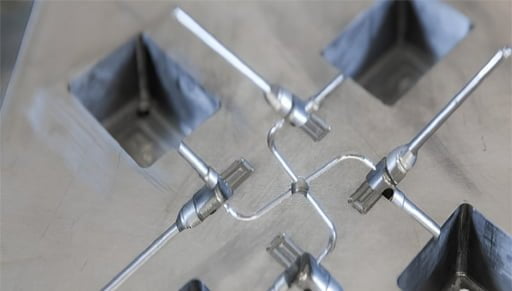
Here is a detailed guide on the types of equipment that may be involved in the process:
1. The injection unit is one of the injection molding equipment. This injection molding device heats and injects the injection molding material into the mold.
2. Second on the list is the clamping unit, which is another piece of injection molding equipment. Before injecting molten plastic into the plastic mold to proceed with the plastic injection molding process, the clamping device must first securely close the two parts of the mold.
3. As the plastic injection mold and molding equipment, additional molds are constructed with steel or aluminum. The mold comprises numerous components but may be divided in half. Each half is joined within the plastic injection molding machine, and the rear half is left to slide so that the mold can be opened and closed along the parting line. Additionally, the mold’s two primary components are the mold core and the mold cavity.
4. When this injection molding equipment is closed, the space between the mold core and mold cavity becomes the part cavity, which is then filled with molten plastic to produce the desired component.
5. The mold base is also considered an injection molding equipment that serves as a mounting point for the plastic mold core and cavity.
6. Finally, the rear half of the mold base contains the ejection system and a support plate. Here, the ejector bar activates the ejection system, whereas the clamping unit separates mold halves. Apart from this, the mold channels are also injection molding equipment that allows molten plastic to flow into mold cavities.
What Plastic is Used for Injection Molding Processing?
With the vast amount of beneficial properties of plastic, the usage of plastic in different industries is widespread today. Every other product we use or see around us is made of plastic. But did you know that there is not one but a total of 7 plastic types that are commonly used in the production processes of different products nowadays?
Speaking of which, when we talk about plastic injection molding processing, the type of plastic used in this process can also vary from usage to usage and the type/shape of the product you plan to manufacture in the end. Likewise, depending on the type of plastic you use, the processing method and the product’s end result also differ. Below are a few of the most standard types of plastics that are used in plastic injection molding:
Polyethylene
This type of plastic employed in the plastic injection molding process belongs to the thermoplastic family. Having said that, it is one of the two most prominent types of materials that manufacturers most frequently choose for plastic injection molding.
Polycarbonate
Polycarbonates are the best and most popular alternatives when it comes to the most mechanically resistant plastics utilized in the plastic injection molding process. This feature distinguishes this particular type of plastic material utilized in plastic injection molding machines. In addition, it also offers extensive transparency and resistance to impact, electricity, and heat.
Polypropylene
Third, polypropylene is arguably the most prevalent form of plastic utilized by plastic injection molding companies – used in items ranging from manufacturing fibers to consumer goods. It is also effective in the production of food and cosmetics packaging, like ice cream packets, ketchup, condiments, shampoos, conditioners, drinking straws, etc.
Nylon
Lastly, nylon is the fourth type of plastic that is frequently selected for custom plastic injection molding. Nylon, or, to be more specific, polyamide, is known to be an extremely tough semi-crystalline plastic. As per the chemical features of this plastic, it comes from a group of robust materials with exceptional thermal qualities.
Products Made from Injection Molding and their Applications:
Since you’re well aware of everything about the plastic injection molding equipment, the types of plastics used in the process, and the characteristics of the mold used during a plastic injection molding service, it’s time to explore the products that are manufactured through this standard and highly trusted process and their applications.
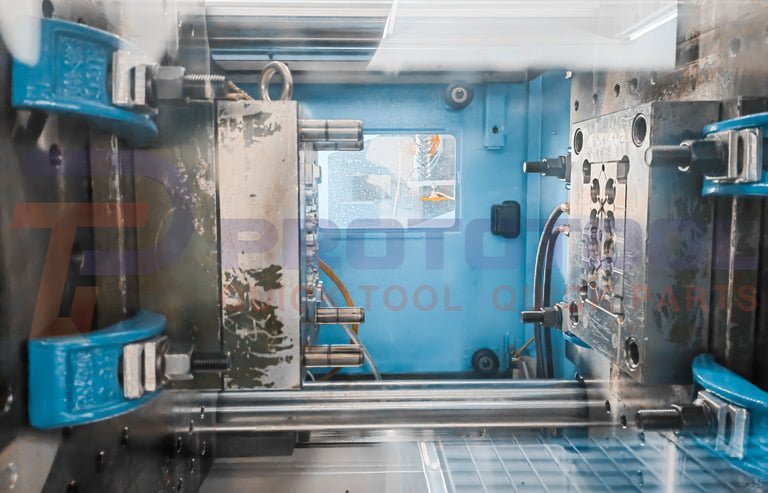
Types of Products:
- Vehicle interiors
- Electric switches and sockets
- Computers
- Children’s toys
- Agricultural equipment
- Medical equipment
- Plastic bottles
- Household items, etc.
Typical Applications of such products:
- Electronics Industry
- Healthcare Industry
- Manufacturing Industry
Benefits of Plastic Injection Molding Processing
Custom plastic injection molding is the best way to make a large number of different plastic parts quickly and with good results. Since this manufacturing process can make complex plastic parts, it is the most common process that is highly trusted by many different industries. Compared to other manufacturing solutions, it is also a reliable and cheaper way to manufacture plastic products. But are the benefits of plastic injection molding services just as substantial as their process and product outcomes? Definitely! Here are a few of the most common benefits of plastic injection molding you can consider:
§ High-speed production
The plastic injection molding process’s efficiency and speed are the most substantial advantages over other production methods. Because of this, they can create the bulk of material quickly. As a result, plastic injection molding service produces high-complexity plastic and larger molds in approx. 15-120 seconds.
§ Complexity of design
We can also use the plastic injection molding process to build intricate pieces. Significantly, the high pressure incorporated in the plastic injection molding machine helps create complex structures.
§ Cost-Effective
Above all, injection molding machine usage is also cost-effective. From assembly through finishing, every phase keeps costs down and boosts efficiency.
Conclusion:
That’s all to the detailed guidelines on the basics, usage, and advantages of a plastic injection molding process. If you have any further queries, we are always available to help you out.