Recently, a client emailed us at Prototool, questioning the varying prices of similar products we’ve collaborated on over the years. They wondered if our pricing was arbitrary. Prototool has been in the prototype industry for 12 years, adhering to a policy of integrity and honest pricing. The pricing of prototypes, being custom products, lacks a standard reference. Most factories base their quotes on the perceived difficulty of the manufacturing process, which can be quite subjective.
However, Prototool operates differently. We gather relevant personnel to discuss the process, labor, and analyze costs, risks, and delivery times in detail after organizing the drawings. This approach ensures more accurate pricing. Let’s discuss the factors that influence the cost of a prototype.
1. Choice of Prototyping Method
In the current scenario, common prototyping methods include CNC machining, 3D printing, and small-batch replication. The choice of material often dictates the prototyping method. For materials with higher requirements, CNC machining is preferred despite its higher cost, as it guarantees material stability. For quantities over ten pieces with material requirements similar to ABS, small-batch replication is chosen. This involves creating one or two prototypes with simple silicone molds, significantly saving time and cost compared to CNC machining. 3D printing is less expensive, but the material strength and temperature resistance are much lower than CNC and replication prototypes.
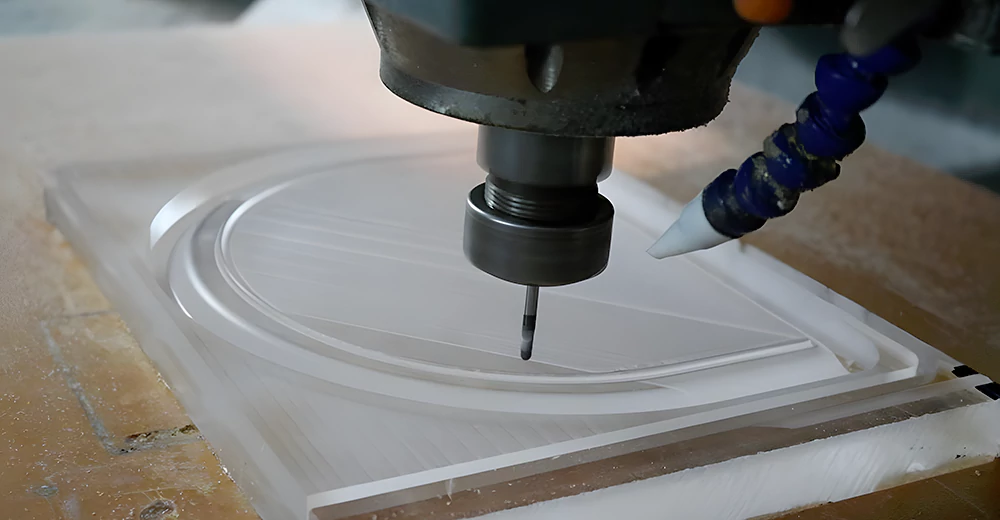
2. Materials Used in the Prototype
Sometimes, choosing different materials can lead to a significant difference in pricing. The reasons are twofold. First, the cost of different materials varies greatly. Special materials like PEEK and Teflon are much more expensive than common materials like ABS, PC, and PMMA. Second, the processing time for different materials varies. Harder materials like aluminum alloy, stainless steel, and POM take longer to process compared to plastics like ABS and PC, as the milling speed is slower and more time-consuming.
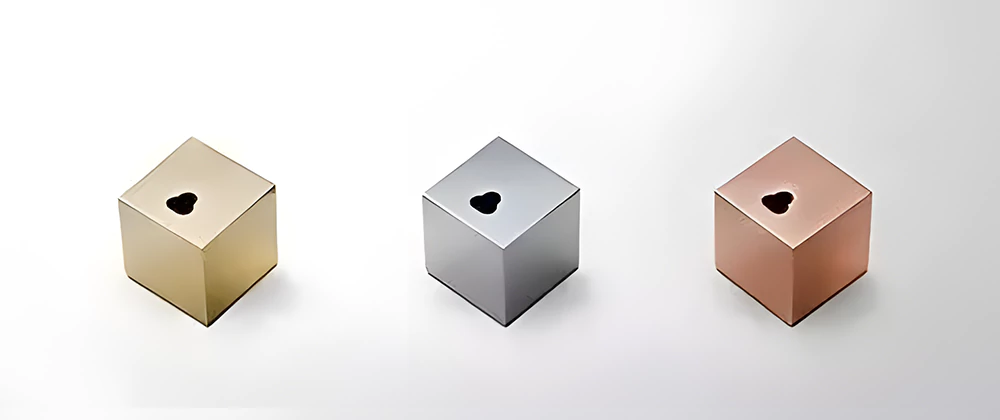
3. Differences in Surface Treatment
For basic or internal components, the process usually involves deburring or rough sanding after machining. However, when advanced finishes like painting, electroplating, or transparency are required, it necessitates meticulous sanding by skilled workers. This increases the labor cost significantly, naturally leading to a higher price for these specialized surface treatments.
4. Risk Factors in Prototype Manufacturing
Many are aware that machining magnesium alloys is expensive. This is due to the high reactivity of magnesium alloy, which has a low ignition point, making it prone to catching fire if not handled carefully during processing. This risk can lead to considerable losses. Similarly, materials with high reactivity or designs with thin structural walls have a higher scrap rate. Therefore, prototype pricing specialists consider these risk factors and adjust their quotes accordingly.
5. Rush Orders and Capacity Saturation
Often, there are situations where a prototype is needed urgently, requiring a turnaround time of two to three days instead of the normal five-day cycle. In such cases, each prototype manufacturer must assess their current order saturation before committing. Prioritizing a rush order inevitably impacts the progress of other orders and may require overtime work from the staff. Therefore, the pricing specialists adjust their quotes based on the current order load and the feasibility of completing other orders smoothly, leading to price fluctuations for rush orders.
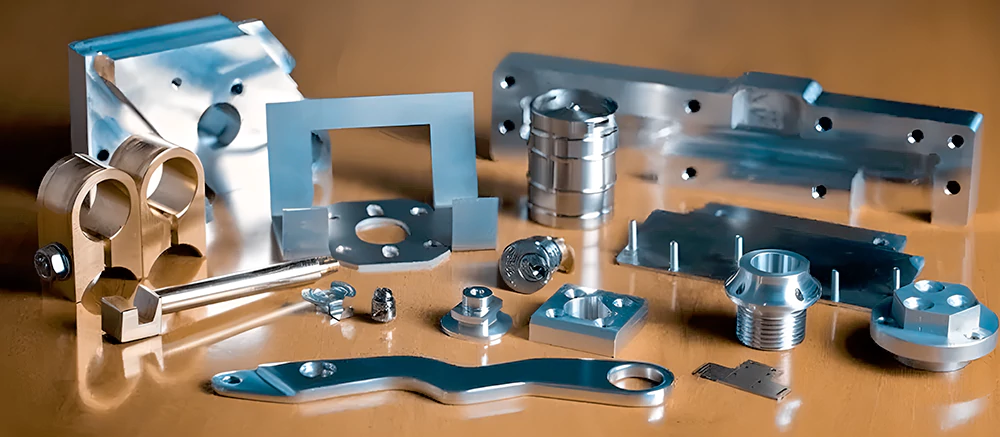