CNC machining is a phenomenal technology. It meets the ever-changing demands of different manufacturing sectors. Precision technology evolved over the years and has become the backbone of numerous industries. Despite its large role, many people may still want to ask: what is CNC machining? Let’s read on to find out.
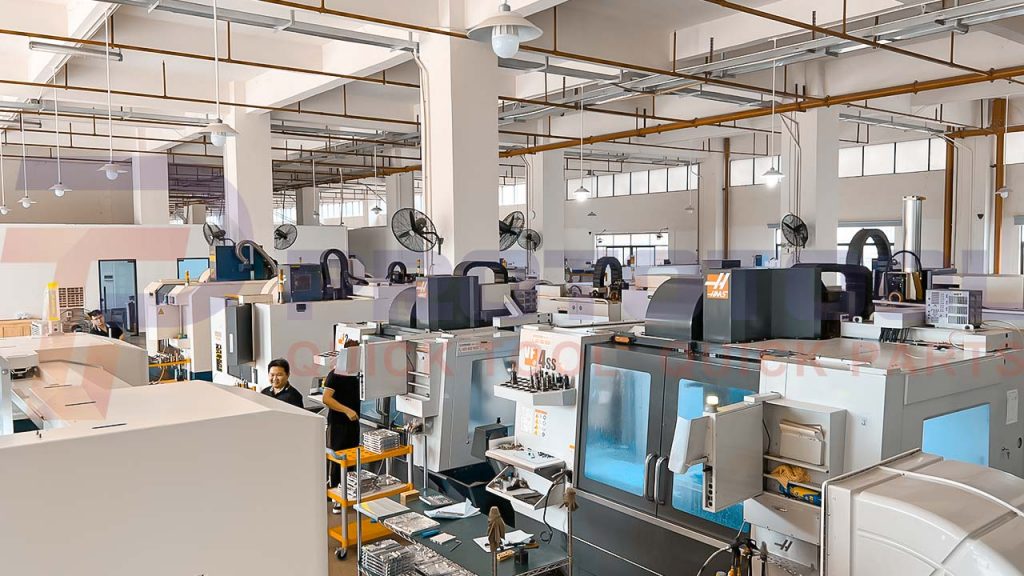
In the modern manufacturing age, old-school machines, such as vertical millers, shaping machines, etc., have been superseded by computer numerical control machines.
Perhaps a chisel and hammer were the best tools people had in the past. But in the present age, these tools seem useless. They will not be productive enough to fulfill production needs in this day and age. If you want to turn your idea into reality and want to be competitive enough in the business, then precision technology is the best option for you.
Before we move on, first, let’s see what a CNC machine is.
What is a CNC Machine?
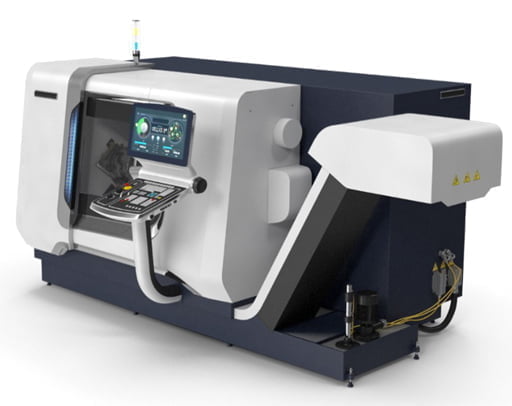
A numerical control machine harnesses computers to render automated control of different machining tools. A raw workpiece is mounted on the machine and is converted into a customized part.
All the process is carried out using pre-programmed instructions from its inception to end. These coded instructions are written according to the design of the part, called a CAD design (Computer Aided Design), and instructions are called CAM (Computer Aided Manufacturing) code.
In the beginning, precision machining was numerical control only. Which used punched tape cards. But after the inclusion of computers, that now has become computer numerical control (CNC).
Today’s CNC machines are technically advanced. In addition, they have revolutionized bulk manufacturing. They offer a great many benefits like high precision, greater processing accuracy, superb efficiency, cost-effectiveness, etc.
But on the other hand, this process is quite complex and intricate. It requires a skilled and expert team to produce parts with your required attributes. When it comes to acquiring CNC machining services, then you can confidently choose PROTOTOOL.
Types of CNC Machines
Besides the 3, 4, and 5-axis, there are six types of CNC machines. They are used for different purposes. The basic function is the same in all these machines that are discussed below.
- CNC Mills
- CNC Lathes
- CNC Plasma Cutters
- CNC Router
- CNC Water Jet Cutters
- Wire Electric Discharge Machines
What is CNC Machining?
CNC machining stands for Computer Numerical Control machining. It is a computer control subtractive manufacturing process. It makes use of pre-programmed software and code to transform a workpiece into a custom-designed product.
These coded instructions direct and control the movement of different equipment, such as mills, lathes, grinders, etc. These machines, in turn, perform the subtractive processes to manufacture any complex shaped parts.
CNC Precision machining enables manufacturers to get their products with any degree of complexity and required characteristics. It offers comparatively cheaper products with tight tolerances as compared to other manufacturing techniques.
CNC Machining Workflow
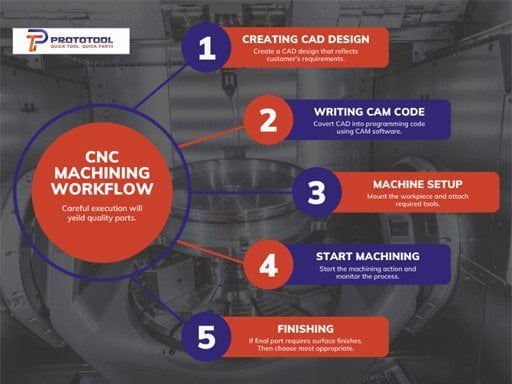
The predominantly CNC machining process consists of five major steps. Successful execution of each step results in an excellent quality part.
- Creating CAD Design
- Writing CAM Code
- Machine Setup
- Machining Operation
- Finishing
The first step includes developing a CAD design. After that, a code is composed that instructs the machine what steps to follow one after the other in a sequence. Then the machine is set up, and machining is started. After completing the process, if a part needs surface finishes to ameliorate aesthetics. Then a most suited finishing technique is selected.
Let’s dive in and see what we need to know about the CNC machining process.
1. Creating CAD Design
CAD is basically software that facilitates designers to create parts digitally with specific dimensions and features. It helps in the development, customization, and optimization of the design. Computer-Aided Design enhances the designer’s productivity and tweaks the quality of the designs. It also provides an opportunity to archive design information for the record and reuse.
CAD can create a 2D vector or 3D solid design of the product. Once the design is completed, then it is exported into CNC-supported file formats. These formats include STEP or IGES extensions. Computer-aided software provides insights that theoretically lead towards an effective way to quality products.
2. Writing CAM Code
Once the design is finalized, next comes writing the code instructions. These programming instructions actually decide the toolpath that directs machines and tools to imitate to manufacture parts.
The software that transforms CAD design into programming code instructions is called Computer-Aided Manufacturing (CAM). We can conceive CAM software as a bridge that links digitally created parts to the world of physical manufacturing.
Two main languages are used in CNC programming. One is G-code, and the other is M-code. G-code refers to general or geometric code. It is responsible for controlling the movement of tools to carve the stock material out. While M-code refers to miscellaneous code. It manages the machine’s miscellaneous actions like initiation and termination of different processes.
3. Machine Setup
As we have created CAD and CAM codes. Now it’s time to set up the machine. Before we start machining the stock material, make sure that the machine is equipped with the necessary tools. Mount the workpiece on the machine. Other facilities, like lubrication, safety measures, etc., are checked for the smooth working of the process.
4. Machining Operation
After proper machine setup, we finally became ready to perform the machining action. Since all the process is automated. Codes direct the machine and determine the tool’s path accordingly. Once all the instructions are successfully executed, then, our process completes, and we get our final product.
5. Finishing
No matter how carefully and delicately you carried out the machining process. But in the end, it might have some unwanted marks on the part’s surface. These unwanted marks can appear even from the tool subtracting the material.
But other than that, there are many other reasons that require surface finishes. Customers may want to enhance surface brightness, sharp aesthetic appeal, protection against rust, corrosion, wear, and additional strength. In this case, a correctly selected surface finish method will be beneficial to achieve customers finishing requirements.
If you want to fabricate your products according to your requirements, then this whole CNC machining workflow needs to be executed in an effective and efficient way. In this regard, you can rely on Prototool, a respectable and trusted name in manufacturing and prototyping. Just reach out to us then we’ll take care of your product for you.
CNC Machining Materials Options
Tips: For more comprehensive knowledge of CNC materials, please click here
One of the biggest advantages of CNC machining is that it offers a huge range of materials to choose from as per your project’s needs. But selecting the right material is critical to the success of your project.
A bad choice of material will affect and disrupt every phase of your product life cycle. It can hinder to meet your deadlines and can cost you time and money. The key to manufacturing a fully optimized finished part leads off with the right selection of your material.
While finalizing a material, just keep in mind that go for that material that meets your product’s characteristics and is cheaper, obviously. Let’s discover what options we have at our disposal.
- Metals
- Plastics
- Wood
- Foam
1. Metals:
When it comes to metals as material for machining, then aluminum is the most commonly used material. Because it has many manufacturing-friendly qualities. Other than aluminum, we have stainless steel, brass, copper, titanium, magnesium, etc.
Each metal has its own distinct set of properties. Customers’ requirements always dictate the selection of one of these as material for their projects.
2. Plastics
Using plastics in CNC machining makes a viable subtractive process for creating complicated plastic products. CNC machined plastics include acrylonitrile butadiene styrene (ABS), acetal, nylon, acrylic, polycarbonate, pom, polyvinyl chloride (PVC), high-density polyethylene (HDPE), polyether ether ketone (PEEK), etc.
Acetal, PEEK, and PVC plastics offer superior machining characteristics like excellent impact resistance, cost-effectiveness, good dimensional stability, and machinability.
3. Wood
Wood can be categorized into hardwood and softwood. Maple, ash, cherry, and walnut are amongst the best hardwoods as materials for precision machining. While cypress and cedar come under the softwood category. The right selection of bits, appropriate feed rate, and speed is very important to process the woods.
4. Foam
CNC machining offers the ability to process different foam types. Carving foam and rigid foam are mainly employed in various applications in many sectors.
Industrial Applications of CNC Machining
Almost every sector in the world takes advantage of CNC machining in one or the other way. Since it offers ultra-high quality mass-scale products at reasonable rates. Therefore, it is getting more and more popular in different industries. Particularly large-scale manufacturers embrace precision technology due to its magnificent advantages that are discussed ahead. But first, have a look at some of the industries that use computer numerical technology.
- Medical Industry
- Military and Defense Industry
- Marine Industry
- Robotics and Automation
- Oil and Gas Industry
- Aerospace Industry
- Electronics Industry
- Transportation Industry
- General Goods
- Automotive Industry
Prototool has served numerous industries. We greatly value our customers and their business needs. To commensurate our workshop with the evolving CNC technology, we invest a huge amount of money in equipping our facility with the latest CNC machines and other technologies. So we can come up with our customer’s expectations.
We have a great team of highly skilled and passionate designers, programmers, engineers, and technicians, who are ready to serve you with the best CNC machining services.
CNC Machining Advantages
The advantages of CNC technology as compared to other conventional and advanced manufacturing processes are great many. Computer numerical machines provide better automation, thus reducing the chances due to human involvement. Also, increased productivity, cost-effectiveness, and large material options are among the benefits. Below is a compilation of some of the main advantages of CNC machining:
High Precision
Precision machining offers highly accurate part creation. As all the process is automated. It is controlled using coding instructions. Once you convert your digital part design into CAM code, then you need to manage the execution carefully. The CNC process can create any complex shaped parts with specific and exact dimensions.
Moreover, CNC machining provides tight tolerances, excellent mechanical efficiency, and superb processing accuracy. That makes it a high-precision product fabrication process.
Productivity
As we can instruct CNC machines through coding to perform a series of different machining actions. So we can easily perform other tasks while the machine has already gone to work. In this way, time becomes flexible and deadlines can be met by working for longer hours that hardly involve human interaction.
Cost Effectiveness
CNC machining offers cost-effective production as compared to other manufacturing methods. Automation through CAM software minimizes errors. Easy CAD design adjustments and lesser chances of errors reduce cost schedule delays and scraping. Furthermore, staff training to manage the workshop facilities is not difficult, and it already requires less labor. These are the key reasons that make the CNC machining process a cheaper one.
Consistency
Precision technology is less prone to manufacturing faults and errors because of the use of computer numerical control, thus yielding accurate and uniform parts for customers. That makes it an ideal choice in sectors where quality and precision are absolutely important and no room for even minor errors is tolerated.
Human Safety
In modern precision machines, it is the machine that is vulnerable to any dangerous safety repercussions. If any jam or tool or stock material breakage happens, then it will only be harmful to the machine, not the operator.
But it is highly recommended that the operator must take proper precautionary measures. He must ensure that he wears proper ear protection and safety glasses while operating the machine. He must check his glasses to be in the proper place when closely observing the cutting tool. Don’t forget to wear safety boots at all times.
Conclusion
CNC machining is a revolutionary manufacturing technology. It offers higher degrees of automation. Precision machining comes with plenty of diverse material options for your products. There are a number of industries that employ computer numerical technology for part fabrication. It provides great advantages that you can get the benefit of to be competitive enough in your business.
If you require high-precision custom-made large-scale products at reasonable rates for your business, then computer numerical machining is the best for you.