PVC injection molding is a very creative and reliable manufacturing process. It can produce highly efficient, durable and complex parts with high precision and cost-effectiveness. Due to its massive benefits, PVC plastic injection molding is highly preferred for part production in many industries.
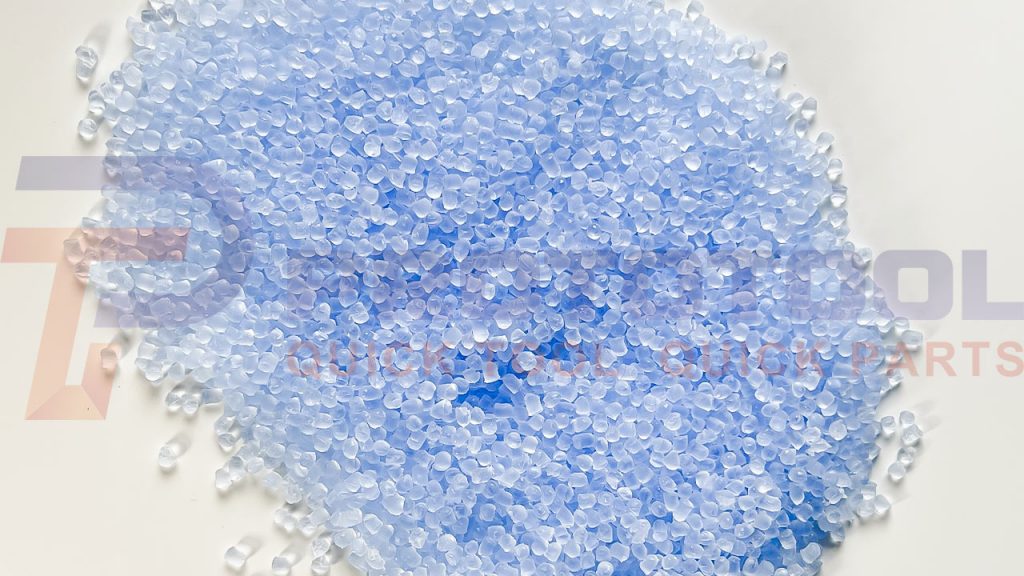
What is Injection Molding?
Injection molding is a versatile manufacturing process. It is used to make several products by injecting molten or liquefied material in a mould. It is perhaps the most widely used method for processing plastics around the globe.
The PVC injection moulding process consists of different phases. These incorporate the liquefication of the plastic material through heating, and then this plastic liquid is injected under high pressure into a temperature-controlled mould. In the end, we solidify the product through cooling.
Injection moulding can host a range of various materials. Which material is to be used depends on the desired product properties. Anyhow, predominantly used injection molding materials are polyvinyl chloride, acrylic, nylon, polypropylene, acrylonitrile butadiene styrene, polystyrene, polycarbonate, polyoxymethylene, polyethene etc.
Now, let’s look at what PVC is and its characteristics.
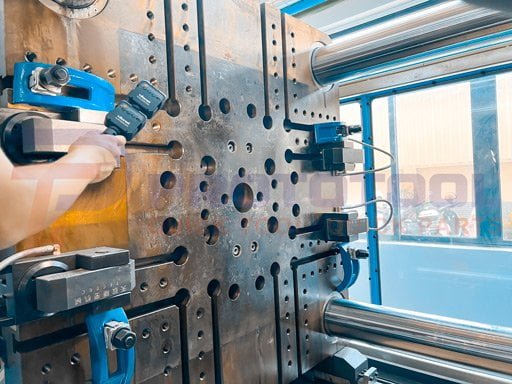
What is PVC (Polyvinyl Chloride)?
PVC is an acronym for polyvinyl chloride, a magnificent PVC injection moulding material. It is the world’s third-most extensively produced synthetic plastic polymer. It is broadly employed to manufacture various injection-moulded plastic goods and parts such as adapters, pipes, R.V. components, computer cases, and components, etc.
PVC polymer was first used in the 1920s on a commercial scale by an American tire company B.F. Goodrich. PVC is available in two forms, i.e., injection molding rigid PVC and injection molding flexible PVC.
Injection molding rigid PVC offers good stiffness, flame performance, and excellent impact resistance. It is used in construction for making doors, windows, pipes, machine housings, etc. Injection molding flexible PVC is also used in abundance in PVC injection molding. The flexibility of flexible PVC can be customized as required by adding a particular amount of different plasticizers. Injection molding flexible PVC is mainly used to make medical tubes, vehicles’ interior trim, garden hoses, etc.
Characteristics of PVC Material
The versatile nature of PVC and its excellent properties make it a fancied choice for PVC injection molding processes. Its properties include high impact strength, lower tensile strength, ease of mold, lower temperature resistance, less rigidness, less chemical resistance, etc.
Injection moulded PVC is economical, easily recyclable, thus environmentally friendly, and has high density and great strength as we can liquefy this polymer that serves as a well-qualified injection-moulded material. It can be heated, poured into a mold, and cooled. Due to its enduring and outstanding properties, it is widely employed in numerous plastic injection molded applications.
Tips: When PVC material is in the injection heating process, if you can not control the temperature, there is a probability of degradation and release of harmful gases, so there are high requirements for injection molding processing.
Runners and Gates
During the PVC injection molding process, we can use all the conventional gates. The runner facilitates the molten PVC resin to pass from the sprue to the gate cavity, and the gate consists of three channels that further the material to be ejected into the part cavity.
If we are fabricating small parts, then a needle-type or submarine gate is recommended. For thicker products, the minimum diameter of a needle-type gate or submarine gate should be 1mm, keeping fan gate thickness at least 1mm.
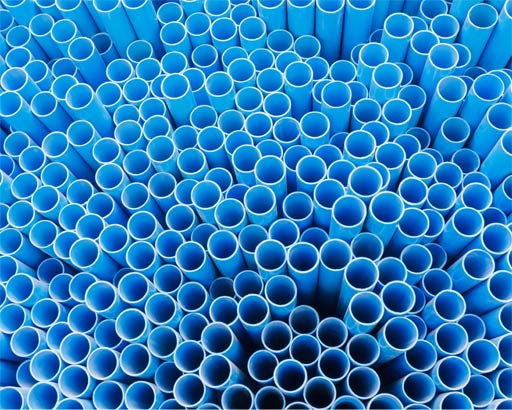
PVC Injection Molding Process Guide
There are many factors to be taken into account to get optimal quality PVC injection molding products. These include mould design and temperature, injection speed and pressure, screw geometry, and many others. These factors and key operational tips are all discussed next in the PVC injection molding process guide.
Moreover, the machinist should check the machine’s condition for excellent and flawless processing. Below is given a complete PVC injection molding processing sequence and important parameters that are particularly discussed for each phase separately.
Drying of PVC
Injection-moulded PVC can absorb a tiny amount of moisture and needs to be dried up. We can heat it for a duration between 1.5 – 2.5 hours under 75 – 90℃. PVC absorbs moisture due to the presence of chlorine ions in it.
Include Additives or Plasticizers
Polyvinyl chloride possesses lower heat stability, and if provided with too much temperature or shear force, it can lead to decomposition. In order to avoid material decomposition, different additives or plasticizers are mixed into PVC during the injection molding process to induce high heat stability. Otherwise, decomposition may bring about some severe hazards to the operator and end-user.
Injection moulded PVC offers serious resistance to strong acids, oxidants, and reducing agents. However, it can be abrasion when it comes in contact with oxidizing acids (e.g., H2SO4).
Screw Length to Diameter Ratio (L/D)
The L/D ratio, in simple terms, is the ratio of the flighted length of the screw to its outside or nominal diameter. Generally, most injection molding machine manufacturers offer an L/D ratio ranging from 19, 20, or 21:1. But some others offer optimized machines with an L/D ratio from 24 to 26:1.
Screw Cushion
The residue PVC in the barrel, which is in front of the screw that cannot pass into the mould after the complete filling of the mould cavity, is called a cushion. The mark at which the screw extends is referred to as cushion value. The screw cushion should be within the limit of 2-3mm. But it may elevate for larger injection molding machines.
Screw Rotation Speed
The screw rotation speed should be 35-50 rpm in most scenarios. But we can adjust it when we need to.
Screw Back Pressure
Screwback pressure is generally selected as mentioned by the manufacturer in the machine specifications. But typically, it is in the range of 60-100 psi.
Injection Capacity
The injection capacity, volume, or shot capacity represents the maximum amount of material the screw can inject in one molding cycle. It is measured in ounces for general applications.
Barrel Temperature
The barrel is the vessel used for material plasticization. It consists of different zones. It supplies pressure and heat when required. A plastic injection molding machine generally has four primary barrel zones, i.e., feed, rear, middle, and front. But the number of barrel zones may increase.
Keep in mind that every material requires different temperatures for barrel zones, and check the specification sheet of the material too. The temperatures for mold, front, mid, and feed barrel zones can be 30-60 °C, 160-180 °C, 150-170 °C, and 140-160 °C, respectively.
Both mold and barrel temperatures are equally vital for efficient working. The mould temperature should be lower than the barrel temperature for the fast cooling of the product.
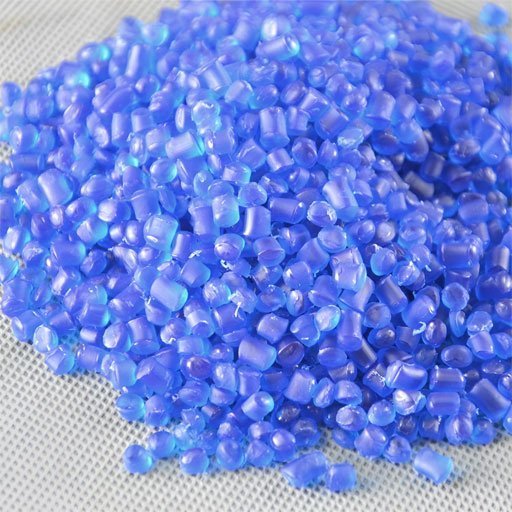
Mold Temperature
Please select Mold temperature carefully. It is recommended to be 70-100 °F for inlet water, and for the ejector side, the temperature should be 10-20 °F less.
Stock Temperature
Stock temperature is regulated with the help of screw speed, screw back pressure, and heater band. Check the specs sheet for exact readings. Heater band settings adjust the barrel temperature to 20 degrees less than the stock temperature mentioned. The nozzle temperature will also be less than recommended stock temperature by 10 degrees.
Injection Speed
Initially, the injection speed should be kept slow to medium to avoid the degradation of injection moulded PVC and increase it further for full-scale productions. For products demanding sheer, thick walls, increase the speed from slow to higher speeds subsequently.
Injection Pressure
Injection pressure depends on the size and shape of the product and also on the size of the gate opening. It assists in pushing molten material into the mold through force applied to the reciprocating screw. About 20-40 percent of the maximum available will produce the ideal consistency.
You can produce quality products by following this PVC injection molding process guide. Please see the manufacturer’s specification sheet for exact readings per your PVC injection molding machine.
Industrial Application of PVC Injection Molding
Chief industries exploiting PVC injection molding are listed below:
- Automotive Sector
- Consumer Goods – Water cups (check the cup overmolding tech), washbasins, and other products that come into direct contact with the human body are prohibited.
- Construction Sector
- Electronics Sector
- Medical Sector
- Industrial Products
- Packaging and Beverage Bottling
The Benefits of Plastic Injection Molding
Injection moulding is the best choice for the plastic industry and businesses producing plastic parts because it offers many benefits. Low-cost production, efficiency, consistency, affordability, and durability are a few to name. Let us look into more details:
Economical Products
In recent years, advancements in plastic polymers and injection mould technology have made it an economical choice for industries and businesses. Revolutionary tooling techniques enable us to create any number of mass-produced products from a single mold and molding process.
Intricate Shaped Parts
One of the most important advantages of plastic mold is that it allows you to work with extremely complex geometrical structures and tight tolerance. A big thanks to plastic injection mold technology. Thus, compared to other mass-production methods, this technology allows you to produce highly complex moulded parts with less hassle precisely.
Huge Materials Options
The next benefit on the list is that the plastic injection molding process offers a wide variety of plastic materials to cater for every requirement of the product at hand. For example, if the plastic part at hand requires strength or it should be flame retardant, then different plastic materials are available to satisfy this need.
Similarly, some materials provide scratch resistance, durability, lubricity, or even optical diffusion as well. In short, plastic mold offers a wide selection of plastic materials to meet different requirements of the products.
High Precision
Another benefit of the injection moulding process is that it offers mass-produced plastic parts with extremely high precision. This technology has become an ideal choice for many applications where precision is paramount because it offers tolerance as tight as +/-0.000015.
Versatile Finishing Methods
Plastic injection molding offers a significant advantage compared to other low-cost mass production processes with many versatile finishing options. These include mirror polish, graphics, exceptional texture, engraving, etc. With the proper finishing of the mold, the finally produced plastic parts won’t need any secondary operation. Thus, versatile finishing is another decisive property of injection molding.
Offers Recyclability and Environment Friendliness
Lastly, plastic injection molding is an environmentally friendly technology that dramatically reduces waste production. Because all or, at least, most scrap plastic is reprocessed, leaving little or no waste. Apart from the environment, it also saves a lot of money. Thus, this technology preserves the environment.
Conclusion
PVC injection molding is an ideal choice for superb economic quality products. Injection-moulded PVC has many physical and chemical properties; most properties are suitable for manufacturing different products.
This article mainly focuses on the PVC injection molding process guide, its different properties, and the benefits of injection moulded PVC.