Die Kunststoff-Spritzguss barrel is a cylindrical component that is integral to the Spritzgießmaschine. It is located between the plasticizing screw and the Formhohlraum. It serves as a chamber for melting and processing Kunststoffmaterialien.
The barrel is typically made of heat-resistant materials, such as hardened steel or bimetallic alloys, to withstand the molten plastics’ high temperatures and abrasive nature.
In this article, we will explore the types, importance, and working of a plastic injection molding barrel, which is one of the key components of an injection molding machine.
Related: Wichtige Komponenten von Spritzgießwerkzeugen, mit denen Sie vertraut sein sollten
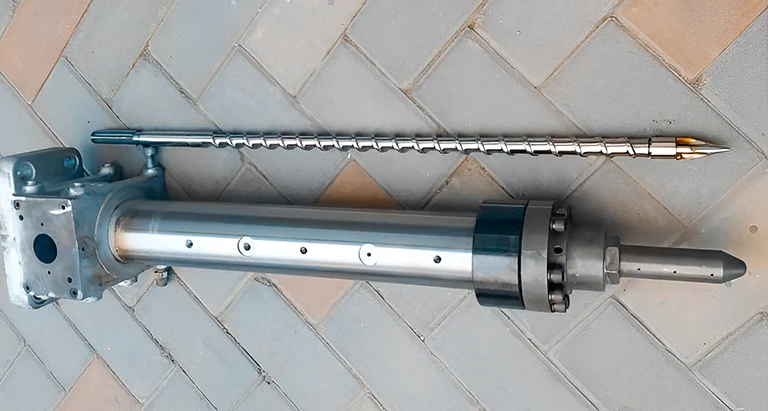
Importance of Plastic Injection Molding Barrel:
Since the plastic injection molding barrel combines with the screw to make up the extrusion system, this key component contributes to the following:
● Melting and Homogenization of Plastic Materials:
The primary function of the injection molding barrel is to melt and homogenize the plastic materials. As the plasticizing screw rotates within the barrel, it generates heat through friction, melting the solid plastic pellets or granules.
The barrel’s internal heating elements provide additional heat as needed, ensuring complete melting and homogenization of the plastic material and eliminating any inconsistencies or unmelted particles.
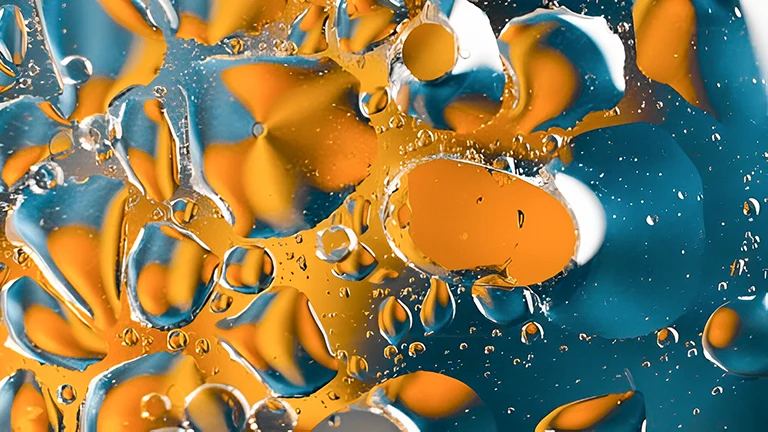
● Mixing and Dispersion of Additives:
In addition to melting the base plastic material, the injection molding barrel facilitates the mixing and dispersion of various additives. Additives such as colorants, reinforcing agents, flame retardants, and lubricants are often incorporated into the plastic material to enhance specific properties.
The barrel’s design and internal geometry, along with the rotation of the screw, promote thorough mixing and dispersion of these additives, ensuring uniform distribution within the melted plastic.
● Temperature Control and Stability:
The plastic injection molding barrel features precise temperature control mechanisms. Heating elements embedded in the barrel maintain the desired temperature profile for effectively melting and processing the plastic material.
Proper temperature control is crucial for preventing overheating or underheating, as it directly affects the viscosity, flow, and quality of the molten plastic. Stable and consistent temperature control within the plastic injection molding barrel ensures reliable processing and optimized part quality.
● Abrasion and Corrosion Resistance:
The plasticizing screw inside the barrel is subjected to significant wear due to the abrasive nature of plastic materials. In order to counteract this, manufacturers use durable, wear-resistant materials to construct the barrel, enabling it to withstand repeated friction and contact with the plasticizing screw.
Hardened steel or bimetallic alloys enhance the barrel’s resistance to abrasion, extending its lifespan and reducing the need for frequent replacements or maintenance.
Properties of a Plastic Injection Molding Barrel:
The barrel in plastic injection molding machines serves multiple functions and properties that enhance overall production. These properties include:
Processing on the Overall Blank:
A plastic injection molding barrel works on the overall blank. This construction is simple to assure high manufacturing and assembly precision. It simplifies assembly, facilitates heating and cooling system setup, installation, and disassembly, while ensuring reasonably uniform heat distribution along the axial direction.
Naturally, this type of barrel necessitates more stringent processing and manufacturing conditions.
A Single Barrel Made of Barrel Combinations:
It denotes that a barrel is made up of numerous barrel pieces. Multipurpose combo barrel with experimental extruder and vented extruder. The former is used to make it easier to change the length of the barrel to accommodate a screw with a different aspect ratio, and the latter is used to configure the exhaust section.
Combining barrels promotes local material acquisition and processing, which benefits small and medium-sized industries. However, the merged plastic injection molding barrel necessitates precise machining.
The combined barrel’s barrel halves are joined together via flange bolts. This reduces barrel heating uniformity and increases heat loss. Setting up and maintaining the heating and cooling system is also inconvenient.
Barrels Are Also Processed To Be Bimetallic:
Many barrels are inlaid with an alloy steel bushing inside the base of regular carbon steel or cast steel to not only meet the material requirements of the barrel but also to conserve valuable materials.
When a bushing wears out, it can be removed and replaced. The bushing and the barrel should be perfectly matched to ensure that heat conduction over the entire barrel wall is not compromised; there should be no relative movement between the barrel and the bushing, and they should be easily removed. This necessitates selecting the right fit accuracy.
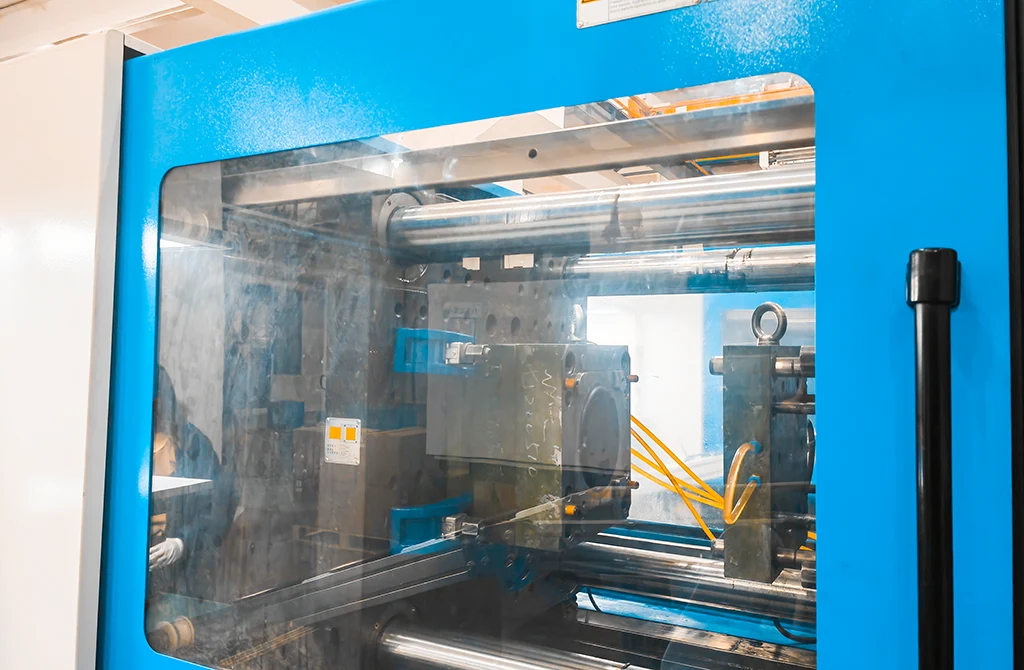
Usage of an IKV Plastic Injection Molding Barrel for Conveying More Solids:
● Using The Longitudinal Grooves In The Barrel’s Feeding Section’s Inner Wall:
According to solid conveying theory, one method for increasing the solid conveying rate is to increase the friction coefficient of the barrel’s surface. Another method is to increase the area of the material at the feeding port passing through the cross-section perpendicular to the screw axis.
The embodiments of these two methods are opening a longitudinal groove on the inner wall of the barrel’s feeding section and forming the inner wall of a feeding section near the feeding port into a cone.
Moreover, the specific structure of opening longitudinal grooves or processing tapers at the barrel’s feeding portion is as follows:
- In normal conditions, the taper length can be (3-5) D (D is the inner diameter of the barrel).
- When working with powder, the taper can be extended to (6-10) D.
- The tapered size is determined by the diameter of the material particles and the screw diameter.
- When the screw diameter rises, the taper should be reduced (and the length of the feeding section should be increased proportionately).
- Longitudinal grooves can only be opened on the barrel portion before the material solidifies or melts. With a taper, the groove length is approximately (3-5) D.
The number of grooves is proportional to the screw diameter. According to IKV, it is approximately one-tenth of the screw’s diameter (cm). If there are too many grooves, the material will flow back and restrict the conveying capacity.
Another thing to note is that the slot of such barrels can be rectangular, triangular, or any other shape. The width and depth of the rectangular cross-section groove are proportional to the screw diameter.
● Using the Forced Cooling Feeding Portion of the Barrel:
Using this second approach, it is easier to cool the feeding section barrel to keep the temperature of the conveyed material below the softening or melting point, avoid the formation of a molten layer, and maintain the material’s solid friction qualities.
The conveying efficiency increases from 0.3 to 0.6 after using the abovementioned approach. Furthermore, the amount of extrusion is less susceptible to changes in head pressure.
However, this system has the following drawbacks: Strong cooling will result in significant energy loss; due to the extremely high pressure (some as high as 800-1500 kg/cm2) near the end of the barrel’s feeding section, there are groove damages.
Now the risk of a thin-walled barrel, increased screw wear, and a greater reliance on raw material performance. Furthermore, the usage of this construction on small extruders is restricted.
Influence of the Barrel’s Feeding Port Shape and Location:
The feeding port’s design and location on the plastic injection molding barrel significantly impact feeding performance. The feeding port should allow material to be supplied freely and efficiently to the barrel without bridging.
The design should also examine if the feeding port is suitable for mounting a feeding device, whether it is easy to clean, and whether a cooling system can be installed in this part.
The feeding port (top view) might be round, square, or rectangular. Typically, a rectangle is utilized, with the long side parallel to the axis of the barrel and the length 1.5-2 times the diameter of the screw.
Choosing a Material for Plastic Injection Molding Barrel:
Like the screw, the barrel must be built of high-quality, high-temperature, wear-resistant, corrosion-resistant, and high-strength materials to meet the functional requirements.
These materials should also be accessible to machines with suitable heat treatment characteristics. The barrel can be made of cast steel oder ductile iron, in addition to 45# steel, 40Cr, and 38CrMoAL. High-quality cast iron can be used for the lined feed portion.
In the last few years, the advancement of high-speed extrusion and engineering plastics has led to an increased focus on the wear and corrosion resistance of the barrel, especially when extruding glass fiber-reinforced plastics and plastics containing inorganic fillers.
Furthermore, the plastic injection molding barrel rotates at high speeds. The massive centrifugal force generated by the molten Xaloy causes it to be cast with a thickness of roughly 2 mm on the inner wall of the red-hot barrel.
Lesen Sie auch: Aluminiumformen vs. Stahlformen: Was ist der Unterschied?
Schlussfolgerung:
In conclusion, the plastic injection molding barrel is a vital component in the injection molding process, facilitating the melting, mixing, and processing of plastic materials.
Its functions of melting and homogenization, mixing and dispersion of additives, temperature control, and abrasion resistance contribute to the overall efficiency and quality of the injection molding process.
The proper design, material selection, and maintenance of the plastic injection molding barrel are crucial to ensure consistent and reliable production of high-quality plastic parts.
Lesen Sie auch: Silikon-Spritzgießen: Alles, was Sie wissen müssen