CNC demolding is the automated approach to getting parts out of an Spritzgussform. This makes it easier for technicians to conduct the machining process effectively.
While many technicians don’t have a detailed understanding of CNC demolding and how it works, a lack of understanding can lead to issues in the production process. As professionals in CNC machining, we here at Prototool will help you understand demolding in detail.
So keep reading to learn all about this demolding approach.
Lesen Sie auch: Vorteile und Anwendungen der CNC-Bearbeitung in der medizinischen Industrie

A Brief Overview of CNC Demolding:
CNC demolding, also known as CNC unmolding or CNC release, is a process used in manufacturing to remove a part or component from a mold or casting. This process is typically automated and performed by a CNC machine, which utilizes computer-controlled movements to precisely and efficiently release the part from the mold.
This demolding process involves several key steps. First, the mold containing the part is securely positioned within the CNC machine. The machine is then programmed with the necessary instructions for the demolding process. These instructions include the specific movements, angles, and forces required to safely and effectively remove the part from the mold.
Once the program is set, the CNC machine begins the demolding process. It uses its mechanical arms, clamps, or other specialized tools to grip and hold the mold or part carefully. The machine then applies controlled forces and movements to release the part from the mold. This can involve tilting, rotating, or sliding motions, depending on the shape and complexity of the part.
During the demolding process, it is essential to ensure the part is released smoothly without any damage or distortion. CNC machines are designed to provide precise and controlled movements, minimizing the risk of part deformation or breakage. The machine’s computerized control system allows for precise positioning and adjustment, ensuring accurate demolding results.
Advantages of CNC Demolding
CNC demolding offers several advantages in the manufacturing industry. It enables faster and more efficient production by automating the demolding process, reducing the need for manual labor, and increasing overall productivity. The precision and repeatability of CNC machines ensure consistent demolding results, leading to higher-quality parts and reduced scrap rates.
Additionally, demolding allows for the demolding of complex and intricate parts that may be difficult or impossible to remove manually. The computer-controlled movements and specialized tools of CNC machines can handle intricate shapes, undercuts, and delicate features, ensuring successful demolding without damage to the part or mold.
Lesen Sie auch: 5-Achsen-CNC-Bearbeitung: Die umfassendste Einführung
The Process of CNC Demolding:
CNC demolding comprises a series of steps and procedures, all carried out by the CNC machine. The following is an in-depth explanation of how demolding normally functions:
Setting up the mold or casting that holds the component that has to be demolded is the first step in the preparation process for the CNC machine. During the process of demolding, the stability of the mold is ensured by the machine’s careful positioning of the mold within the machine.
● Programming:
The CNC machine has been given very particular programming instructions to perform the demolding operation. These instructions provide the motions, angles, and forces that must be used to remove the component from the mold without damaging it. The programming is accomplished through the use of specialized software or code languages that are unique to CNC machines.
● Gripping and Fixturing:
The CNC machine employs mechanical arms, clamps, or specialized fixtures to securely grip and hold the mold or item while it is machined. The demolding process immobilizes the component to avoid damage from movement or displacement.
● Computer-Directed Movements:
The computerized control system of the CNC machine takes over and carries out the instructions that were programmed into it. It is responsible for controlling the motions of the machine, including the placement, rotation, and tilting of the mold or component. Carefully planned movements ensure a smooth demolding process with no component distortion or damage.
● Forces That Are Under Control:
The CNC machine uses forces under control to remove the item from the mold. Depending on the particular design of the CNC machine, these forces may be applied in the form of hydraulic or pneumatic pressure, mechanical actuation, or some other method.
Forces are controlled to ensure smooth demolding without excessive stress or strain on the part.
● High Levels of Precision and Repeatability:
CNC machines can perform motions with a high level of precision and repeatability. Furthermore, they can position and alter the mold or part with such precision that the outcomes of the demolding process are reliable and constant. This precision helps to preserve the part’s integrity and guarantees that it satisfies the requirements outlined in the specification document.
● Checks for Quality:
It is possible to conduct quality checks at various points in the demolding process to ensure that the part retains its structural integrity. This can include visual inspections, measurements, or other quality assurance measures to determine that the demolding was adequate and that the part satisfies the requirements.
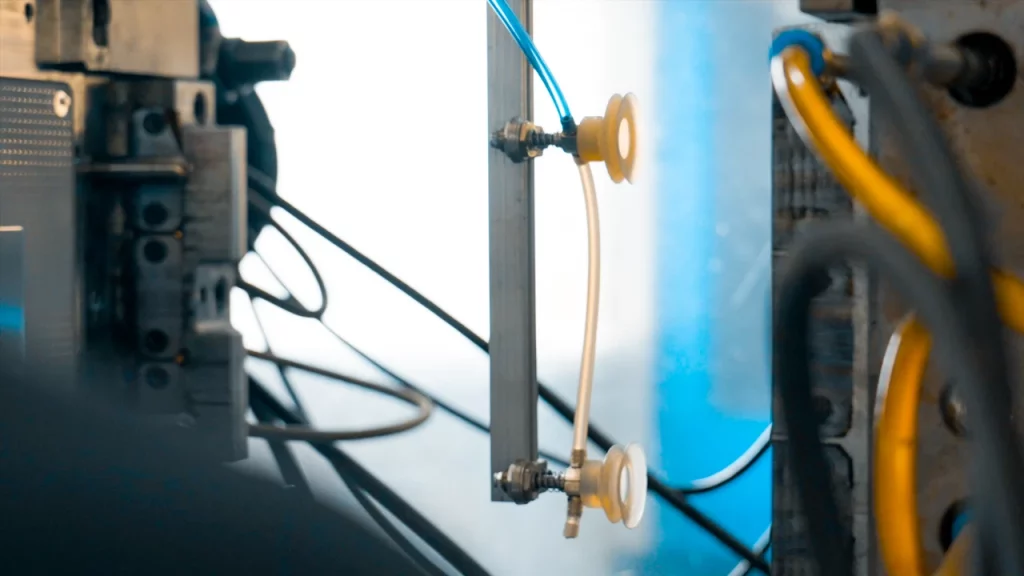
CNC Demolding vs Manual Demolding: The Difference
Both computer numerical control (CNC) demolding and manual demolding are two distinct methods for extracting parts from molds. Let’s get into more depth about these different approaches:
Efficiency and Speed:
CNC demolding is more efficient and faster than traditional methods because the machines follow precisely the instructions that have been put into them. They can quickly remove parts from molds, reducing the time required for demolding. On the other hand, manual demolding involves human labor, which might result in a slower process overall, mainly when dealing with complicated molds or parts.
Precision and Consistency:
Higher levels of both precision and uniformity can be achieved through the use of CNC demolding. How exactly? During the demolding process, CNC machines’ movements controlled by a computer guarantee perfect positioning and consistent force distribution.
Because of this, the quality of the parts is maintained. When manual demolding is performed, the output quality depends on the operators’ knowledge and expertise, which can vary and lead to inconsistencies.
Complexity and Geometric Flexibility:
CNC demolding is excellent at working with intricate geometries and complex part designs. CNC machines can handle difficult designs with ease and excellent accuracy. Some examples of such designs include undercuts, complex curves, and internal elements.
In contrast, the manual demolding process may struggle with elaborate patterns, requiring additional effort and carrying the danger of harming either the item or the mold.
Labor Intensity and Operator Skills:
The labor intensity required for demolding is reduced since the demolding process is automated once the machine has been programmed and set up. The operator skills required for CNC demolding are also reduced.
Having said that, it takes only a small amount of intervention from the operator. The manual demolding process requires more expertise and labor because it depends on the operators’ talents and physical effort.

Safety and Ergonomics:
CNC demolding improves both aspects of workplace safety and ergonomics. It reduces the risk of physical strain and injuries resulting from repetitive hand motions involved in demolding.
Using CNC machines reduces the likelihood of an accident or injury due to manual handling because these machines are built with safety and dependability in mind.
Scalability and Production Volume:
CNC demolding is appropriate for high-volume production as it is very scalable. Once the CNC machine has been set up, it is capable of demolding huge amounts of parts consistently and efficiently.
In comparison, manual demolding may be better suited for low-volume or prototype production, where flexibility and adaptability are critical.
Kosten:
CNC demolding demands higher upfront investment due to costly CNC machine acquisition and maintenance. The manual demolding process has lower prices for the equipment required, but it may have higher costs for the labor required, particularly for production on a big scale.
Verwandte Seiten: Angebot für CNC-Bearbeitung: Was sind die einflussreichen Faktoren
Schlussfolgerung:
In the end, CNC demolding offers several advantages over manual demolding methods. It provides faster and more efficient production, increased precision and repeatability, and the ability to handle complex part geometries. By automating the demolding process, CNC machines reduce the reliance on manual labor and improve overall productivity while maintaining high-quality standards.
Even so, CNC demolding is a precise and controlled process that utilizes computerized movements and controlled forces to safely and efficiently separate a part from its mold or casting. Its accuracy, repeatability, and ability to handle complex part shapes make it an indispensable technique in modern manufacturing processes.