Moldeo por inyección de polipropileno es un procedimiento en el que un polímero termoplástico se calienta por encima de su punto de fusión y luego se convierte en un polímero sólido a un fluido fundido. Sin duda, tiene una viscosidad baja. A continuación, este polipropileno fundido se inyecta en moldes para obtener la forma deseada de las piezas. La finalidad del moldeo es producir formas más complejas de productos de polipropilenoen su forma original.
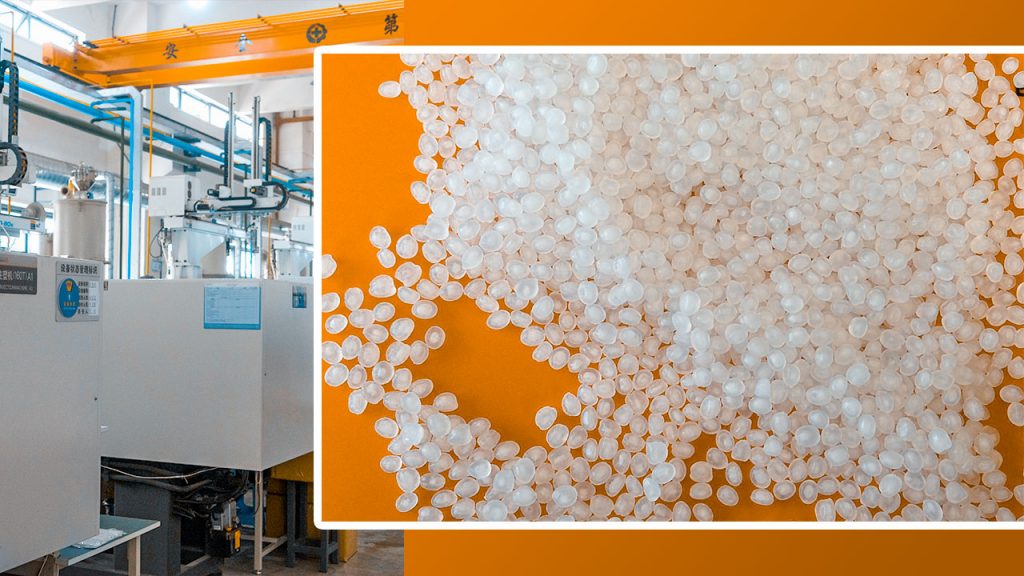
Puede producir miles o incluso millones de piezas idénticas repitiendo este proceso si es necesario. Así, moldeo por inyección de polipropileno permite a los fabricantes producir tantas piezas de plástico como deseen utilizando un solo molde.
Ahora se estará preguntando qué es el polipropileno. ¿Qué es en realidad? ¿Y para qué se utiliza? Sin más dilación, profundicemos en los detalles.
En este artículo, he tratado los principales aspectos del polipropileno, sus ventajas y cómo puede utilizarse el polipropileno para moldeo por inyección.
¿Qué es el polipropileno?
Polipropileno se abrevia como PP. Es un termoplástico en el que los monómeros de propileno están unidos a una cadena mediante polimerización. Este tipo de polímero plástico es reconocido por sus propiedades resistentes y flexibles.
Importancia del uso del polipropileno para el moldeo por inyección
PP es el plástico de mejor calidad utilizado para moldeo por inyección. Suele presentarse en forma de gránulos.
- Su baja viscosidad de fusión le permite tener una consistencia suave y fluida. A pesar de su naturaleza semicristalina, puede moldearse fácilmente y adoptar cualquier forma. Esta propiedad mejora significativamente el grado en que se puede llenar un molde con el material. Por ello, sigue considerándose la opción de material más popular para la fabricación en PP moldeo por inyección.
- Su superficie extremadamente viscosa lo convierte en un excelente sustituto de otros plásticos en zonas donde se requiere menos fricción.
- El polipropileno y el polietileno tienen características casi similares. La única diferencia es que el PP es ligeramente más firme y más resistente a la temperatura.
- Es extremadamente resistente a la erosión, el óxido y las fugas químicas. Esta propiedad lo hace perfecto para almacenar disolventes, bases y ácidos.
- El PP es de fácil acceso, bajo coste y actúa como gran aislante eléctrico.
Un dato interesante sobre plástico polipropileno es que muchos fabricantes de la industria del plástico lo llaman acero. La razón es que lo personalizamos de varias formas para fabricar diversos productos.
Aquí te ayudaría si estuvieras confundido sobre la diferencia entre plástico y polipropileno. ¿Se parecen?
Piensa, piensa.
Un polímero con una masa molecular elevada es plástico. Polipropileno es una ilustración de un polímero plástico. Polipropileno y plástico difieren en la forma de utilizar el polipropileno para crear completamente materiales transparentesmientras que los materiales plásticos suelen ser opacos.
Usos del moldeo por inyección de polipropileno
Se utiliza para fabricar piezas de plástico para diversos productos de distintas industrias, entre las que se incluyen:
- Envases para productos de consumo, como envases alimentarios de yogur, queso fresco, productos de mantequilla, etc.
- Piezas de plástico para la industria del automóvil
- Dispositivos especiales como bisagras vivas
- Instrumental médico
- Materiales textiles
- Juguetes infantiles
Pasos del proceso de moldeo por inyección de polipropileno
Alimentación
Los gránulos de plástico se introducen en la tolva y luego caen en el barril.
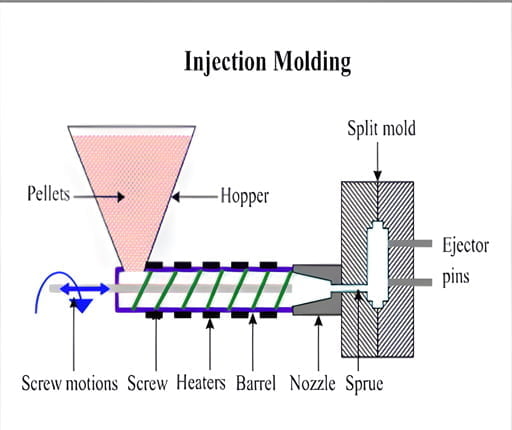
Plastificación
El tornillo giratorio dentro del barril desplaza el perdigón hacia delante. Los gránulos de plástico se calientan gracias a la banda calefactora que rodea el cañón. El tornillo giratorio impulsa los gránulos hacia delante, fundiéndolos progresivamente hasta que están completamente fundidos cuando llegan a la parte delantera del barril. Entre una temperatura de 450 y 500 F es el rango ideal para que se produzca el proceso de moldeo. Para ello, debe fundirse.
Inyección
Cuando hay una cantidad suficiente de plástico fundido delante del tornillo, éste lo introduce en la cavidad del molde a través del sistema de bebederos y canales del molde.
Mantenimiento de la presión
El tornillo forzará constantemente el plástico fundido en el molde para su sustitución. El plástico fundido se contrae dentro del molde a medida que se enfría hasta que se transforma totalmente en un producto completamente estructurado. Para mantener la temperatura del molde dentro del rango prescrito, el controlador de temperatura del molde inyecta agua o aceite en el sistema de refrigeración.
Refrigeración
Al enfriarse, el plástico fundido se convierte en sólido en pocos segundos.
Expulsión
La varilla de expulsión empuja hacia delante los pasadores de expulsión a medida que se desbloquea el molde. La pieza y el canal se dejan caer al exterior y se recogen en un contenedor. A continuación, el procedimiento se repite con frecuencia para fabricar más artículos de plástico.
Normalmente se utiliza una velocidad rápida para mantener las tensiones internas lo más bajas posible durante el Proceso de moldeo por inyección de polipropileno. Sin embargo, es preferible utilizar una velocidad más lenta a temperaturas más altas cuando las imperfecciones superficiales y defectos ocurrir. Se recomienda encarecidamente la utilización de maquinaria capaz de proporcionar una velocidad perfilada.
Puertas y Corredores para el Polipropileno proceso de moldeo por inyección
Un paso crucial en el moldeo por inyección de PP es el uso de compuertas y canales. La compuerta que conduce a la cavidad del molde se encuentra en el extremo del canal. La porción tiene una imperfección superficial causada por la compuerta. Debido a su pequeño tamaño, está destinada a congelarse antes de que se congelen la pieza, el canal o el bebedero. Para evitar marcas de hundimiento (superficies hundidas) durante el enfriamiento, la cavidad se mantiene llena.
Sistema de compuerta para moldeo por inyección de PP
Colada
Cada molde tiene un punto de contacto que conecta la máquina con un Molde de bebedero. Su base esférica hueca permite al Punta de boquilla Para acoplar a la máquina de moldeo. La punta de la boquilla y la base del bebedero necesitan un radio idéntico e igual. Si No Se Unen Con Precisión, El Material Se Fugará Y Producirá Piezas Inconsistentes. A continuación, el polipropileno fundido se desplaza por el bebedero y llega a la base de la boquilla. Corredor.
Corredor
El canal recibe el PP. Es una vía que empuja el líquido fundido directamente a la entrada de cada pieza. En el caso de una sola cavidad de Molde de Inyección, se requiere una rama para el canal. Si tiene múltiples cavidades, introducirá múltiples ramales para garantizar un equilibrio real de flujo para obtener una proporción igual de material.
Cuando se diseña un canal, es necesario diseñar un conducto frío en cada punto de la rama. Esto se debe a que hay un desplazamiento definido entre cada rama. Cuando el plástico fundido en caliente deriva a través del sistema de canalización, se enfría. El canal frío protege el plástico de polipropileno frío de ser vertido en la compuerta. Los tamaños más utilizados para los moldes de canal frío oscilan entre 4 y 7 mm.
Puerta
En la etapa final, el plástico penetra en la compuerta. En este punto, el proceso de moldeo por inyección de PP se enfrenta a muchos problemas de compuertas. Aunque el diseño de las compuertas puede suponer un reto, conocer a fondo su función puede ayudar a producir una compuerta adecuada para piezas moldeadas por inyección de plástico.
El plástico entra por la puerta al final. Es donde se producen muchos problemas en la Proceso de moldeo por inyección de PP. Las compuertas pueden ser complicadas, pero entender su propósito puede ayudar a diseñar una compuerta adecuada para piezas moldeadas por inyección de plástico.
Cuanto más grande sea la puerta, mejor será conseguir la material de moldeo por inyección en la cavidad. Se pueden emplear todo tipo de compuertas. El diámetro de las compuertas de pasador suele fijarse entre 1 y 1,5 mm; sin embargo, también pueden tener diámetros tan pequeños como 0,7 mm.
Compuerta apta para moldeo por inyección de plástico
El tamaño pequeño de la compuerta se recomienda porque una compuerta de aterrizaje grande provocará la degradación del material debido a la excesiva fricción producida por el calor. Se pueden conseguir compuertas más pequeñas disminuyendo el tamaño del terreno de la compuerta. La mayoría de las empresas cometen este error porque el plástico se congela inmediatamente al llegar a la compuerta si el terreno es demasiado grande. Normalmente, la anchura de la tierra no debe ser superior a 0,006″.
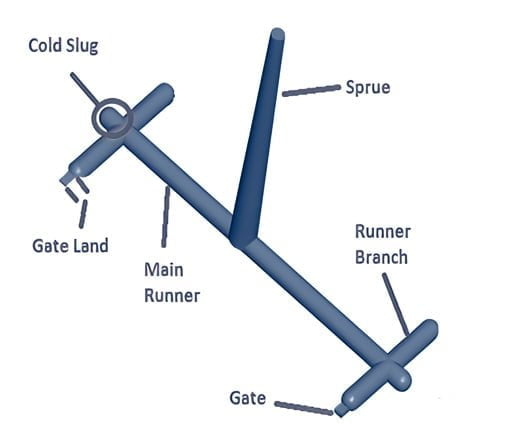
Colocación de la puerta
La compuerta debe colocarse donde se encuentre la pared más gruesa. Es fundamental observar cómo se desplaza el plástico desde la compuerta hacia la cavidad. Es preferible colocar una compuerta antes de un núcleo parado.
El segmento de pared más grueso suele ser donde debe colocarse la compuerta en una pieza determinada. Sin embargo, es fundamental poder observar cómo se desplaza el plástico desde la compuerta hasta la cavidad. Es preferible colocar una compuerta antes de un núcleo parado en la herramienta.
Aunque el moldeo por inyección de PP se inventó hace mucho tiempo, es el método más contemporáneo de producir plástico. Se realiza mediante una máquina conocida como máquina de moldeo por inyección de polipropileno.
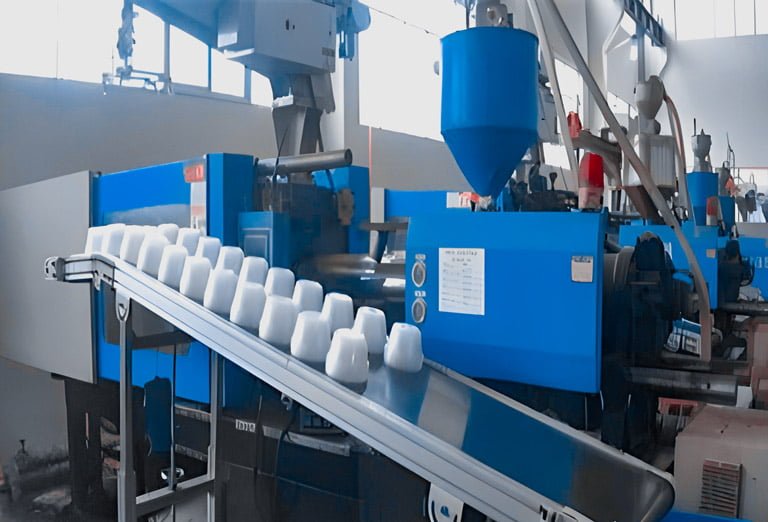
Grande, industrial máquina de moldeo por inyección de polipropilenos son muy costosos: más de $200.000. A esto hay que añadir los costes de contratación y formación de personal cualificado, su mantenimiento, vigilancia e incluso el cumplimiento de la legislación del sector.
Dado que los productos de plástico proceso de moldeo por inyección de polipropileno suelen ser más detallados y pequeños que los producidos por rotomoldeo, requieren naturalmente más tiempo y mano de obra, lo que puede elevar el coste final. Pero no se preocupe. Puede recurrir a los servicios de Moldeo por inyección de PP ofrecido por Prototool.