Plastic molding quality control is essential in plastic injection molding because it ensures that goods are perfect. It requires careful steps for planning, developing, designing, and making.
The proper mold design method and the correct process planning ensure customers get high-quality plastic products that meet their needs. Precision production control helps stop and eliminate mistakes so quality standards are always met.
In this article, we’ll look at a specific example of water process control to show how complicated quality control in plastic injection molding can be.
Also Read: What is Design for Manufacturability? DFM Principles Explained
The Need for Plastic Molding Inspection: An Example
Plastic molding quality control is crucial in plastic injection molding if you want perfect results. Let’s look at how water is controlled during the process of casting. Using the right amount of water is very important for making high-quality plastic goods. If there isn’t enough water, the plastic structure can weaken, making apparent plastic goods cloudy and ruining their finish.
On the other hand, too much water can cause cracks, a problem for businesses that care a lot about how their products look, like the medical and automotive industries. This is a big problem for some Chinese businesses that make plastic molds.
In the past, dryers were used to reduce the amount of water in plastic particles, but they could not properly measure the amount of water. Advanced moisture monitors have been made in the United States, Europe, and China to deal with this problem.
Before casting, these monitors can accurately measure how much water is in the plastic. This makes it easier to control and improve production. With this kind of cutting-edge technology, the plastic molding industry can improve production efficiency, cut costs, and make high-quality goods that meet the high standards of many industries.
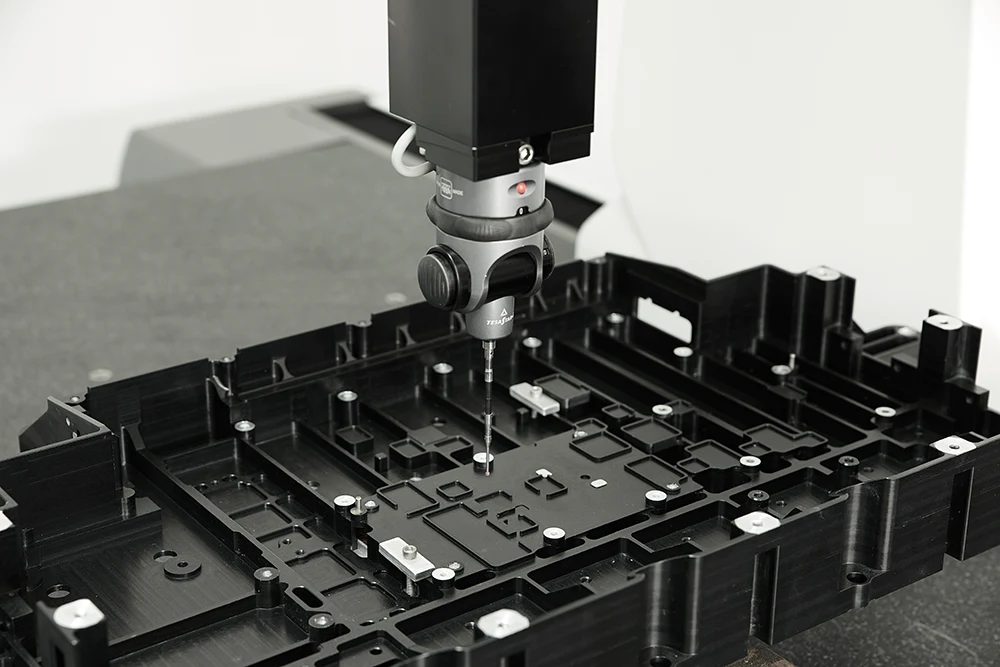
Unfolding Plastic Molding Inspection Process:
In professional manufacturing setups like Prototool, plastic molding inspection consists of four steps. The first step is the planning stage, followed by Mold and Pre-Production Inspection, In-Process Quality Control, and Final Inspection.
Lastly, it’s time for system certification and plastic molding quality control of the process. Now, let’s explore each of these steps below in detail:
Design Review
Design review is the first step in making sure the quality is good. This study should be done with designers and engineers inside and outside the company. This step’s goal is to ensure that all designs are checked to ensure they are correct before production begins.
You can test your idea with 3D printing before investing time and money to make a full-size model. When you use 3D printing, you can see what your product will look like before you buy the tools and materials to make it. Once they’re done, you can also get a good idea of the final production models’ size.
At this stage, you thoroughly plan how your product will be made. The following are parts of the plan:
Making a Product
Your product’s design will tell you how much material you’ll need for each part and how many parts you’ll need for each batch. If your product is made of more than one plastic material, this step also includes figuring out which materials will work best for injection molding.
A few factors that matter when designing a product include:
- Plastic Type: Choose a standard grade of plastic for a similar purpose, or go with what the supplier suggests.
- Draft Position: Choosing the right position for the draft because A draft angle makes it easier to take a finished part out of a mold after it has cooled. Injection casting is impossible without draft angles. Most design engineers say that parts with enough draft should have draft angles of at least 0.5° for the hollow and 1.0° for the core.
- Wall Width: Choosing the right wall width is essential because When the plastic product wall thickness of an injection-molded part from a plastic products provider is correct and the same all the way around, it is less likely to have structural or cosmetic problems. Most plastics have walls that are between them.04 and.150 inches thick. Still, you should talk to an injection molder/design engineer and a plastic manufacturer to find the thickness specs for the material(s) you want to use.
- Ribs: Ribs strengthen the walls of injection-molded parts without making them thicker, making them an essential part of injection-molded parts. Depending on the material, the ribs shouldn’t be more than 2/3 as thick as the wall. WIDE ribs may cause problems with sinking and design. If the height of the ribs is more than three times the thickness of the wall, the part might be too short to be filled. In the early stages of a part’spart’s design, the placement, thickness, and length of its ribs are crucial to figuring out whether or not it will work.
- Gate: Parts made with injection molding have at least one gate, but they often have more than one. The direction of the polymer molecules and how the part shrinks when it cools depend on where the runner and gate are. So, the form and function of your part are affected by where the gate is. If it has to be straight, the gate should be at the end of a long, narrow part. It is best to put a gate in the middle of a part that must be round.
- Ejector Pins: Plastic manufacturers should create and place ejector pins as early as possible. If you aren’t careful, it can leave marks and dents on the object. Depending on the draft, the roughness, the depth, and the type of material, ejector pins are usually at the bottom of the side walls. By looking at the shape, you might be able to tell if the first place you put the ejector pin was right. You may also be able to make more changes to improve how the process goes.
Part Layout
When it’s time to make your product, the part layout is how you put all the parts together. During injection molding, how things are set up can change how fast they are made and what materials are used.
For instance, choosing between two materials to mold various parts can cut production costs by using less material, saving time and money.
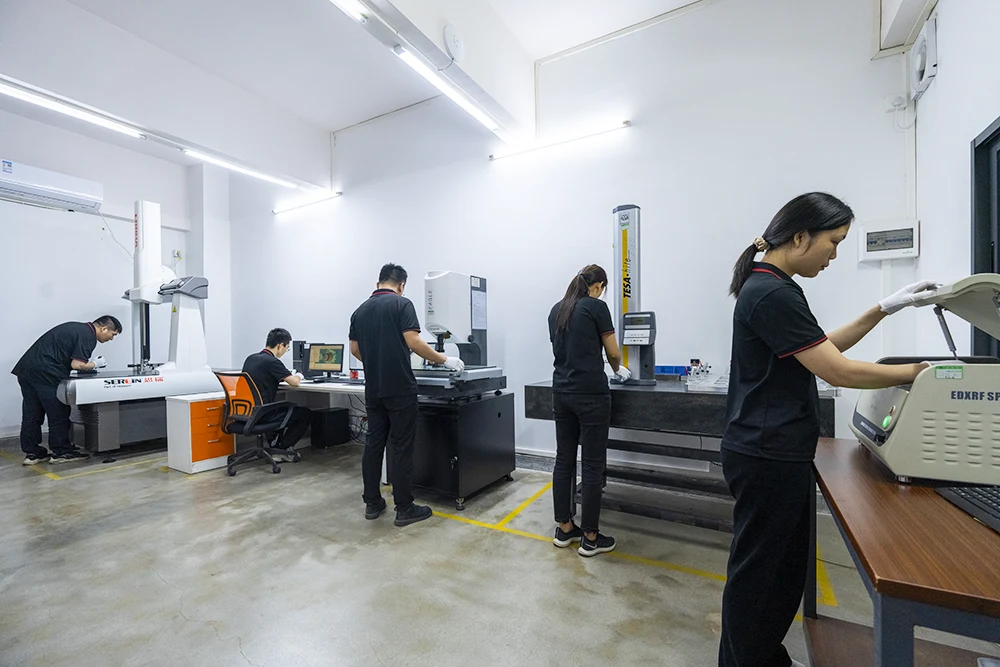
Mold and Pre-Production Inspection
Plastic molding quality control ensures that a product meets all of the standards. It is an integral part of any manufacturing process. This stage can be broken down into four steps:
- Designing the mold
- Inspecting the mold before production
- Inspecting the mold during production
- Inspecting the mold after production
Mold Design
This is where you create the mold that will be used to make your product. This is the first step in getting your product made. Then, you use different materials to make the mold based on what you’re making. For instance, injection molding usually uses molds made of metal or steel alloys, while other processes use ceramic or sandstone molds.
Related: Principles of Selecting and Creating an Effective Mold Base
Pre-Inspection:
During this step, the parts made during the injection-molding process are checked before they are sent out. It can also be called the “first article inspection.” This ensures that each part meets the requirements and that problems are found before reaching customers.
Now, inspectors look at each part visually and use measuring tools to ensure that the sizes, weights, and tolerances are right according to your requirements. They also test how well the parts work by seeing if they fit well.
Another consideration in this regard is the part’s strength. This is because the parts may not always work perfectly right out of the mold. In addition to visual plastic molding inspection and plastic molding testing, inspectors may also use X-rays or other non-destructive testing (NDT) or plastic molding testing methods to ensure that things are safe and work as they should.
When plastic is injected, the most common kinds of mistakes that can happen are:
- Not all the colors and textures are the same
- Misaligned or missing holes
- The sizes of holes, width, and other measurements are wrong.
- Cavities that aren’t filled (flash or short shot)
Also Read: Steps to Consider When Processing CNC Machining Projects
In-Process Quality Control:
Raw materials must be checked before they are used in the injection-molding process to ensure they meet standards. This is the first step in the Plastic molding quality control process.
The second step is to check the temperature, pressure settings, and other parts of the injection-molding machine to ensure they are working properly. This step ensures the material is melted completely before entering the molding machine. This helps eliminate problems like air bubbles or a bad finish on the surface of molded parts.
The next step is to check the molten plastic for any alien particles that could cause problems when injection molding. After the plastic has been cleaned of any small pieces, it can be inserted into a mold.
The last step in quality control is to check molded parts for gaps or other flaws. This ensures that each piece comes out of an injection-molding machine with the right shape and no flaws.
Final Inspection:
Before a part leaves the plant, this is when it is checked for flaws. Before being packed and sent out, each piece is inspected by hand to ensure that only the best ones get to customers. This process ensures that the product is of high quality and has no flaws, such as scratches, bubbles, or other flaws. If there are any problems, they are fixed before the product is packed and sent out.
People with a lot of training do the check and can find any problems with the parts and materials used to make the product. Only perfect products are sent out, so customers only get the best.
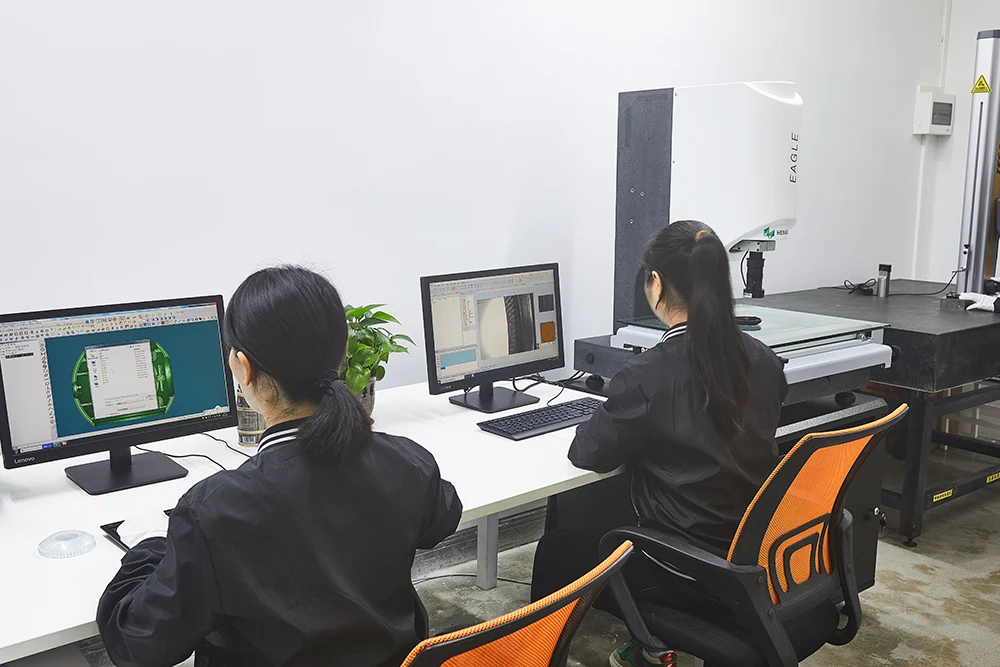
Packaging:
Once the plastic molding inspection is completed, it’s time to pack the part. Here, the package of the part must be strong enough to keep the item from getting broken while it’s being shipped. It should also tell you how to safely set up or use your product if something goes wrong. If you can, use packaging materials that can be reused or recycled. This is better for your world and ours.
Conclusion:
Quality is a word that is often used as a buzzword and in brand phrases, but it can mean different things to different people and groups. With quality in mind, a company needs a way to describe what quality is and how it is measured and managed.
If you need a new strategic partner, you might want to look for one like Prototool, which has an ISO9001:2015 certification. This is important because it shows that a business or organization has a structured focus, clear measurements based on customer needs and rules, and how the structure is used.
This way, you can seek professional assistance to understand what quality is and how to measure it.