HDPE injection molding has become a game-changing technology in modern manufacturing, changing how many goods are made. This article gives a brief overview of HDPE molding. It talks about how precise, efficient, and essential it is to many different businesses.
What is HDPE?
High-density polyethylene (HDPE) is a highly crystalline non-polar thermoplastic resin with a milky white appearance and some clarity in thin sections. It’s natural-colored columnar or oblate pellets with outstanding hardness, tensile strength, creep/wear resistance, and chemical stability.
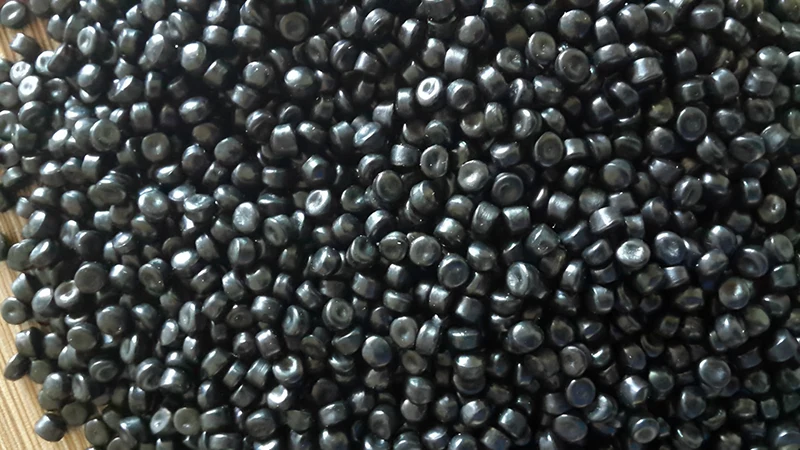
Use-Case of HDPE Molding:
Injection molding using HDPE can make parts of various configurations and dimensions. First, the HDPE plastic is melted into a form that can be molded. After the HDPE resin has achieved the molten condition inside the HDPE máquina de moldagem por injeção, the HDPE is forced into the mold to complete the process.
The mold is made of metal and has two sides: the cavidade on side A and the núcleo on side B. After being injected into the HDPE mold, the plastic resin begins to harden practically immediately after the process. The component will eventually harden into the shape of the mold, at which point the mold will release it, releasing the component.
After then, the HDPE mold is readjusted, and the process begins again.
Leia também: Compreender a bucha de guia no molde de injeção
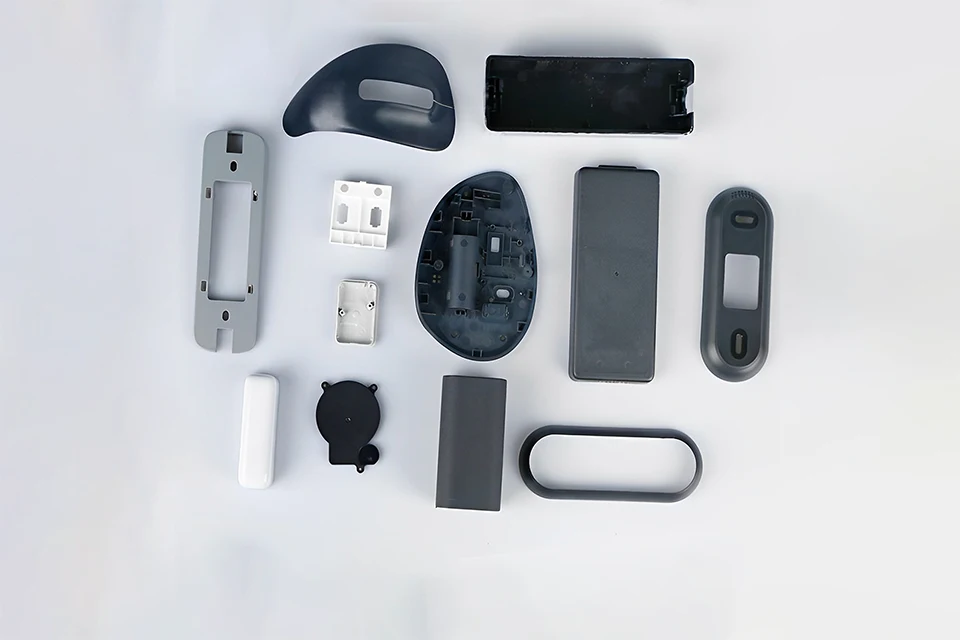
HDPE: A Preferred Material for Injection Molding
Due to its remarkable qualities and versatility, high-density polyethylene molding, often known as HDPE molding, has become one of the most sought-after injection molding options. HDPE stands for High-Density Polyethylene, a thermoplastic polymer known for its remarkable strength, durability, and exceptional resistance to impact, chemicals, and moisture.
Additionally, HDPE is a material that can be recycled. Because of these qualities, it is an excellent option for many industries, including the automotive, construction, consumer products, and packaging industries. In addition, HDPE is easily recyclable, making it compatible with efforts to achieve sustainability goals and production practices that are mindful of the environment.
Advantages of Employing High-Density Polyethylene Molding (HDPE):
● Personalization:
The capacity of HDPE injection molding to produce highly individualized products is one of the most significant benefits offered by this manufacturing method. The procedure starts with designing a customized mold to meet the one-of-a-kind requirements of the object to be produced.
This high level of customization empowers producers to fulfill unique specifications and create complex geometries, which would prove challenging or even unattainable through conventional manufacturing techniques.
● Reduced Costs:
HDPE molding provides cost savings for producers, making it an attractive option for that application. Injection molding is a procedure that often requires much less manual labor than other manufacturing methods due to its high level of automation and reproducibility.
Consequently, labor costs and production efficiency are reduced to their lowest possible levels. Injection molding’s fast cycle times provide a speedy turnaround, further contributing to the process’s low-cost nature.
● Efficiency:
Compared to more conventional molding techniques, high-density polyethylene molding is particularly efficient. Molten HDPE material is injected into the mold cavity while the cavity is pressurized to complete this process.
Production cycles can be completed more quickly because the material quickly cools and hardens within the mold. Productivity can be considerably increased through large increases in the number and variety of pieces produced simultaneously during each molding cycle.
● Higher Volumes:
HDPE injection molding is an excellent choice for high-volume production because of its suitability. Once the mold has been designed and the manufacturing process has been established, manufacturers can promptly make hundreds, or even millions, of components while maintaining a high level of quality control. Because of its scalability, HDPE molding is the method of choice for large-scale projects that demand huge amounts of output.
Leia também: Barril de máquina de moldagem por injeção para fabrico de alta precisão: Fabrico, utilizações e propriedades
Initial Investment vs. Long-Term Benefits of HDPE Injection Molding
It is correct that HDPE injection molding needs an initial investment for the mold’s design and manufacture before it can be done. On the other hand, when creating bigger quantities of parts, economies of scale become more advantageous.
Because of the decrease in cost per part that occurs with increased production volume, HDPE molding offers particularly favorable advantages over the long term. Manufacturers can profit from this cost decrease over time, which is especially beneficial for projects that require a consistent and large production output.
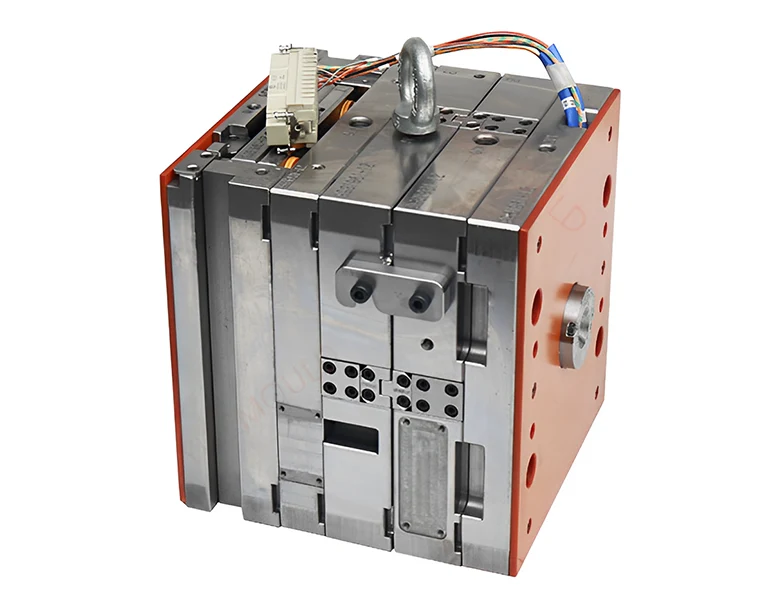
Drawbacks That Come with HDPE Injection Molding:
If you’re new to HDPE injection molding and want to consider it for your next product’s production, you must be familiar with the drawbacks of HDPE injection molding. Some specific disadvantages of opting for such injection molding solution include:
Strategic Choice for High-Volume Projects
Injection molding made of HDPE is a strategic and cost-effective solution for projects requiring the manufacturing of many parts. It is an attractive choice for meeting production demands in various industries due to its mix of high-volume capabilities, efficiency, and ability to customize products.
HDPE molding allows producers to balance precision, speed, and cost-effectiveness in their production processes, whether making components for automobiles or mass-producing consumer goods.
Reshaping Modern Production Processes
Injection molding with HDPE has unquestionably been a driving force behind the transformation of modern manufacturing across many different markets. It is now possible to manufacture highly personalized, long-lasting, and cost-effective parts while operating at a remarkable level of efficiency.
This has fundamentally altered the manufacturing process. Injection molding made of high-density polyethylene (HDPE) is expected to continue to play a pivotal role in precision manufacturing for the foreseeable future. This molding technique will develop novel goods that satisfy industries’ and consumers’ changing requirements.
High Initial Expenditures for Tooling
The substantial initial expenditure necessary for tooling the mold in HDPE injection molding is one of the most prominent disadvantages of this manufacturing method. One of the most important components in injection molding is the mold, normally constructed from high-strength steel to ensure its durability and lifespan.
Because of the precision engineering and skilled craftsmanship required for its development, the price of the tooling can range anywhere from $3,000 to far over $100,000 or even more, depending on the complexity and scale of the product.
This cost might represent a significant financial burden for manufacturing runs that are on the smaller side, and it needs to be carefully considered in light of the eventual total part run.
The Development of Mold Takes a Long Time
Designing and producing the HDPE mold requires a lot of time. To get the required quality of the item while maintaining precision in the engineering, we need to test the mold and make any necessary adjustments.
The amount of time needed to develop a mold might range anywhere from a few weeks to several months, which can delay the manufacturing schedule for new projects or orders that are considered urgent.
Limited Design Changes during Production
Once the mold has been finished and the production process has begun, it is difficult and expensive to make significant design changes to the components of the product. Any changes made to the mold could necessitate considerable retooling and testing, which would result in additional production downtime and costs.
This limitation may provide a problem for producers who want to make prospective design modifications or revisions while producing the product.
Material Wastage and Recycling Challenges
During the manufacturing process, HDPE injection molding results in the loss of some of the material. The production of waste, in the form of scrap or extra material, is a common outcome that must be managed and recycled appropriately.
Even though HDPE can be recycled, the process can be complicated for particular material grades due to the additives and other factors that can come into play. Furthermore, to reduce waste and keep a sustainable approach to production, it is essential to ensure that correct recycling methods are in place for all materials.
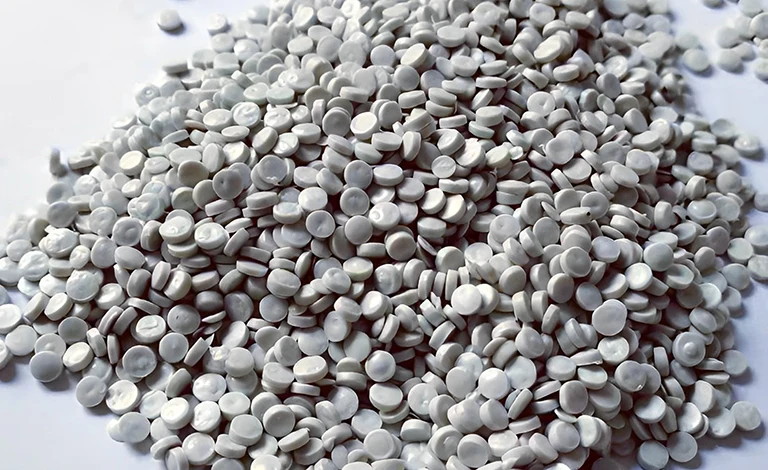
Sugerido: Como funciona uma unidade de injeção numa máquina de moldagem por injeção?
Limited Availability of Compatible Materials for Some Applications
HDPE is a versatile material appropriate for a wide range of applications; nevertheless, it is possible that it is not the best option for specialized industries with very stringent criteria. For instance, the temperature resistance of HDPE may not be adequate for components subjected to intense heat or extremely hostile chemicals.
So if a company wants high-performance materials, they may need to look for engineering plastics that suit the application. Despite these drawbacks, high-density polyethylene molding continues to be an important and commonly used manufacturing method.
To effectively mitigate the initial tooling expenses and harness the benefits of HDPE molding for cost-effective, high-quality part production, fabricantes de moldagem por injeção can effectively mitigate the scope of a project and the projected production volume by strategically assessing the project’s scope and the expected production volume.
—–
Still have questions? Contact our professional injection molding manufacturers at Prototool.com.