The hot runner plate has defied tradition in the plastic Spritzgießen industry since its conception in the 1960s until its acceptance in the 1990s. Hot runners appeal to many who want to diversify their injection molding process due to their enhanced cycle speed and decreased waste.
However, it can be tricky to design and use a hot runner plate if you’re unfamiliar with it already.
Don’t worry; It doesn’t mean you can’t diversify your manufacturing process, as we have you covered with the full knowledge you need to know about a hot runner plate in this blog. So without further ado, let’s dive into the details.
What is a Hot Runner Plate?
To make a plastic product, a Heißkanalsystem distributes liquid plastic to several mold cavities. An Spritzgießen assembly employs a heated manifold to keep the plastic molten. This heated plastic is supplied directly into several cavities from the molding machine’s nozzle via internal passages known as runners.
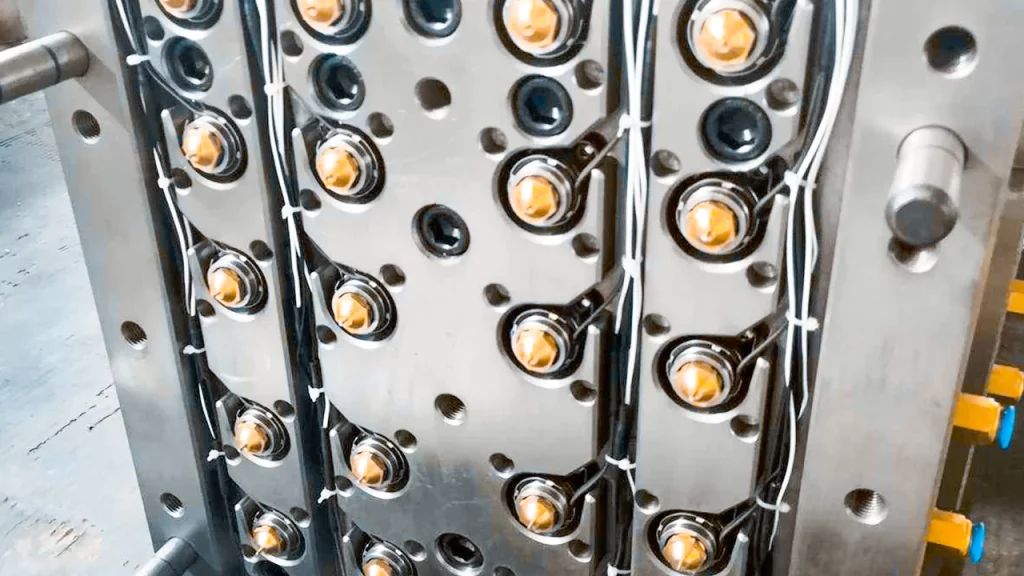
Working Mechanism of a Hot Runner Plate:
A hot runner plate, also known as a hot manifold system, is a component used in injection molding that helps deliver molten plastic material to the mold cavities. It eliminates the need for sprue and runner systems, improving efficiency and reducing material waste. Here’s how a hot runner plate works:
1. Design and Assembly: Die hot runner plate consists of a manifold, a block or plate with channels and heaters, and a set of nozzles connecting to the mold cavities. People usually make The manifold from a thermally conductive material like tool steel or copper alloy. The plate is heated using electric heaters or hot oil circulation systems.
2. Melting and Flow: During the initial stage, we feed the plastic material into a hopper and subsequently transfer it to a heating chamber. The heating chamber melts the plastic, creating a molten resin. The molten resin is maintained at a controlled temperature to ensure its fluidity.
3. Distribution: The molten plastic is injected into the hot runner manifold, distributing it evenly to the individual nozzles connected to each mold cavity. The manifold channels are designed to maintain a consistent temperature throughout, ensuring the molten plastic remains fluid.
4. Gate Opening: The hot runner nozzles are positioned at the gate locations of the mold cavities, where the plastic material enters the cavity. When the injection starts, the nozzle gate opens and enables the molten plastic to flow into the mold cavities.
5. Cooling and Solidification: The cooling phase begins once the molten plastic fills the mold cavities. Cooling channels within the mold, including those near the hot runner plate, help extract heat from the part, promoting solidification and dimensional stability.
6. Part Ejection: After the molded part has sufficiently cooled and solidified, the mold opens, and the part is ejected. The hot runner plate remains in place, ready for the next injection cycle.
Hot Runner Plate vs Cold Runner Plate:
Most plastic injection molding today uses two types of runner plates: hot runner systems and cold runner systems.
Although the two plates have many differences, one of the most significant distinctions is that hot runners have the capability to inject plastic directly into the part cavity. Because the sprue and runners remain hot during the injection process, the part is the only component removed each cycle. As a result, the mold can be cycled swiftly again.
Verwandte Seiten: Spritzgießkanal: Typen und Tipps für die Qualitätsproduktion
Because of the significantly smaller injection point, this characteristic produces better-looking goods by allowing for great detail and smooth surfaces. Hot runner systems are suited for high-volume manufacturing due to their enhanced cycling time and reduced plastic waste.
These advantages are with downsides. Hot runners are generally more expensive than cold runners.
Moreover, the Heißkanalsystem is larger and more sophisticated, which results in a longer setup time and higher installation costs. Understanding the advantages and disadvantages of both systems is crucial, as each system is suited for different products.
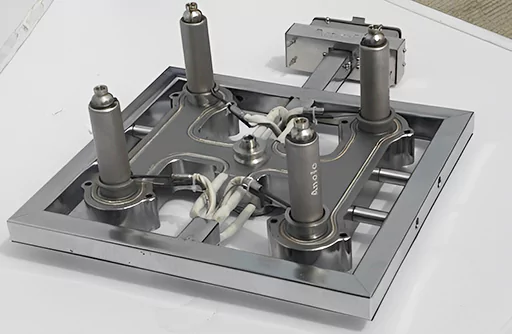
How To Design a Hot Runner Plate?
To guarantee that the Spritzgießen operations are effective and dependable, we’d better carefully consider various issues while designing a hot runner plate. The following is an in-depth tutorial that will assist you in the design of a hot runner plate:
Recognize the Needs of Both the Part and the Mold:
To get started, ensure you completely understand the part’s specifications and the mold. Consider analyzing aspects such as the part’s geometry, the material, the gate locations, the number of cavities, and the injection parameters you want. Think about whatever special criteria there are for the quality of the parts, the cycle time, and the output volume.
Determine the Type of Hot Runner System to Use:
Determine the kind of Heißkanalsystem to use by looking at the part’s specifications and the mold. The valve gate, the thermal gate, and the hot tip systems are examples of common types. Consider the benefits and drawbacks and whether or not they are appropriate for the application you have in mind.
Determine the Number of Drops:
Determining the required number of hot runner drops or nozzles is essential and should be based on the number of mold cavities and the preferred gating options. When making decisions regarding the number and placement of drops, it is important to take into account various aspects, such as the complexity of the part, its balance, and the size of the shot.
Determine Nozzle Size and Configuration:
Determine the nozzle size and configuration depending on the amount of material being processed, the part’s design, and the processing parameters. Think about things like the style of the nozzle tip, the diameter of the sprue, the diameter of the melt channel, and the length of the nozzle. The nozzle and the gate of the mold chamber must be aligned correctly.
Design the Manifold Layout:
When designing the various layout within the hot runner plate, it is important to consider multiple criteria, including temperature uniformity, simplicity of maintenance, and material flow balancing. The channel widths, lengths, and flow pathways should be optimized so that all drops have equal flow and minimal pressure losses.
Incorporate Heating Elements:
To keep the temperature within the manifold at your chosen level, integrate heating elements such as electric heaters or conduits to circulate hot oil into the hot runner plate. It is important to strategically position the heaters or channels to ensure that the plate is heated evenly and to prevent temperature changes.
Design the Cooling System:
Incorporate cooling channels inzu the design of the cooling system for the hot runner plate to facilitate heat dissipation and maintain the desired operating temperature. Getting the design of the cooling channel accurately is crucial to ensure efficient heat removal without interfering with the flow channels and nozzles.
Auswahl der Materialien:
When selecting a material for the hot runner plate, you should go for one with high thermal conductivity, corrosion resistance, and mechanical strength. Tool steel and copper alloys are two common materials, although the type of material used depends on the application’s specific requirements.
Design and Geometry of Gates:
The first step in gate design is to determine the geometry of the gates that will connect the hot runner nozzles to the mold cavities. You should also consider the gate size, the type of gate it is (for example, an edge gate or a tunnel gate), its position, and its geometry. Ensure the gate is properly filled, reduce the amount of gate remnant, and improve the overall part quality by optimizing the gate design.
Thermal Management:
We should optimize the thermal management of the hot runner plate for optimal performance to guarantee consistent heating and cooling. Incorporating thermocouples or temperature sensors may be beneficial to achieve more accurate temperature management and monitoring.
Collaboration and Validation:
Throughout the design phase, work closely with mold designers, manufacturers of hot runner systems, and seasoned toolmakers to collaborate and validate your designs. Furthermore, make sure to use your knowledge and experience, and do simulations or mold flow analyses to evaluate the design of the hot runner plate and improve its performance.
Lesen Sie auch: Wichtige Komponenten von Spritzgießwerkzeugen, mit denen Sie vertraut sein sollten
Schlussfolgerung:
Overall, a hot runner plate is important in Spritzgießen processes, providing several advantages that boost production and efficiency. Reducing runner waste is a significant advantage, as the hot runner method ensures that molten plastic is fed directly to the mold cavities without the need for runners to be cooled and discarded.
As a result, understanding hot runner plate technology is critical for injection molders.
Molders can obtain high-quality, reproducible results by monitoring and controlling the temperature and flow of molten plastic within the Heißkanalsystem, maximizing the overall success of the Spritzgießen Prozess.
Have more questions about the hot runner plate? Fragen Sie unsere Experten unter Prototool.de.