Plastics are everywhere, and different techniques are used to make plastic products. One of these methods that are used a lot is injection molding. Also, manufacturers use this process because it helps them make high-quality parts cheaply. But what does injection molding make the products? Injection molding is utilized in various items and sectors, including manufacturing toys, bottle caps, surgical instruments, jewel boxes, and vehicle components such as dashboards. In this article, we will look at several examples of products made by injection molding, their applications, and their advantages.
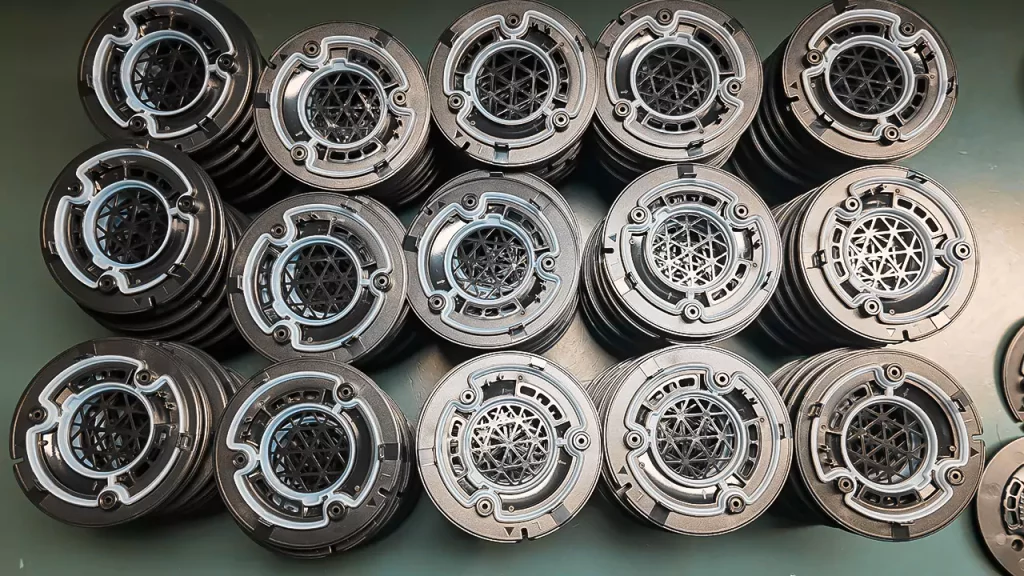
Example of Popular Products Made by Injection Molding:
Among the wide list of plastic products used today, most of them are manufactured using the injection molding method. Some examples of such products made by injection molding include:
Living Hinges:
Among the endless production solutions, injection molding is probably the best and most cost-effective way to manufacture living hinges. Why is that? The volume is a consideration mainly because in this process and product both. For several reasons, injection molding is the method of choice for producing live hinge manufacturers. These reasons can include the following:
- The brisk turnaround time is one of the most important advantages.
- Compared to creating plastic using any other method, producing living hinges utilizing this method is significantly quicker.
- Additionally, the final quality of living hinges made using this method is superior to those made using CNC machining, which is another reason why this method is preferred.
Snap Fits:
Today, plastic parts are a common application because manufacturers use them to preserve the aesthetic consistency of a design. They are considering that another one of the standard products made by injection molding includes injection-molded snap fittings. These fittings are made with plastic injection. They are more flexible and can easily withstand the rigors of parts’ assembly and disassembly processes.
Using injection molding to create snap fittings makes it easier for the design to return to its original, unstressed state once it has been engaged with its mating part.
On the other hand, if returning to a not stressed position is physically impossible, an injection-molded snap fit can continue to function while stressed. During the plastic injection molding, this stress must be lower than the maximum stress the design material can tolerate, i.e., fifty percent of the material’s elastic limit.
Using injection molding, engineers can build snap fits that quickly snap together and pull apart with a simple push or pull movement. These snap fits can be readily assembled and disassembled.
Threads:
Threads illustrate moldeo por inyección de plástico well because you can frequently see them on the neck of plastic containers and bottles. Manufacturers utilize injection molding to produce both internal and exterior threads.
Using injection molding to create external threads requires the creation of a mold tool that incorporates a portion of the thread into both the center of the plastic and the cavity of the part. Also, because of this, it is simpler to remove the molded plastic from the tool. On the thread, there should be a thin joining line that serves as a visible indicator of the point at which the two sides of the molding tool come together.
To get internal threads, on the other hand, you have to go through a separate procedure. The method used in this situation entails the utilization of a threaded core or cavity that can be removed. In addition, the producer will insert this threaded core into the mold tool before injecting the polymer used in the procedure into the mold tool. After that, the injected polymer hardens, forming the thread.
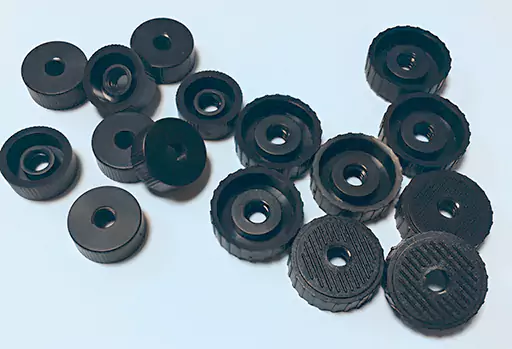
Living Caps:
Another example of a product made by injection molding is a living cap. A cap created from an extension of the parent material is called a residing cap. The living caps that are produced through the method of injection molding have a very long lifespan. They can bend through an angle of one hundred and eighty degrees or more than one million times without breaking.
In addition, putting together a living cap does not require separate components because it is one continuous piece. Four primary categories of hats are available here:
- Child-safe
- Straight or flat
- Double or triple
- Butterfly
- And double or triple.
Threaded Inserts:
Threaded Inserts are another example of an injection molded product. These inserts help provide reusable threads and are used in various applications. Another advantage is that it maintains the structural integrity of bolted joints throughout the application. In addition, they prevent the threads from being stripped by allowing the correct amount of torque to be applied to the screw during installation.
Engineers commonly use two types of plastics for threaded insert installations thermoplastics and thermosets.
Thermosets:
Thermosets comprise various materials, such as polyester resins, urea, epoxies, and Bakelite. In addition to that, the polymers that fall into this category are both heat-resistant and durable. As soon as they are formed, it is difficult to reform them by applying pressure and heat since the chemical change that occurs is irreversible. Inserts that are press-in, molded-in, and self-tapping can all be manufactured using this sort of plastic with great success.
Thermoplastics:
On the other hand, thermoplastics have a solid state at ambient temperature but can be molten when heated above a certain degree. Plastics such as ABS, polyamide, polycarbonate, and polyvinyl chloride are examples of the prevalent types of plastics that fall under this category. Thermoplastics are utilized by engineers in the production of heat/ultrasonic inserts, press-ins, as well as molded and self-tapping inserts.
Equipment Housings:
Injection molding is also one of the most cost-effective methods for producing housing for electronic equipment compared to the other methods of making plastic. This is especially true when manufacturers intend to create housing for the equipment in large quantities. In addition, manufacturers utilize this method to produce housing for equipment in various industries, including computer electronics, medical equipment, and other healthcare-related fields.
In addition, one aspect that distinguishes injection-molded equipment housing from other housing types is that it is simple to disassemble, making it easier to access the product contained within the housing.
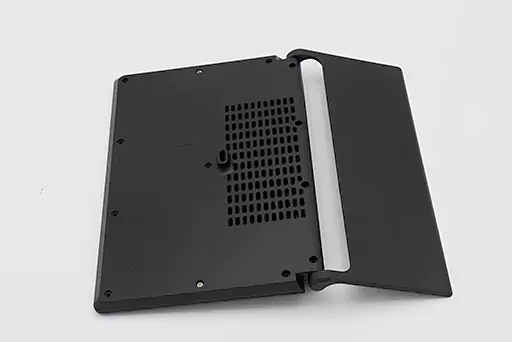
Deck Fasteners:
Injection molds used by makers of deck fasteners cover the inserts of stainless steel screws with resilient polymer compounds such as polypropylene and polyethylene. In addition, the combination makes the deck fasteners resistant to UV rays, making them exceptionally long-lasting regardless of the prevailing weather conditions in a particular location.
Injection-molded deck fasteners provide several benefits, one of which is that they permit the deck wood to expand and contract without restriction.
Insulators:
Adding more to our list of examples of products made by injection molding, insulators are also produced with the injection molding process, which also finds use in producing other insulators. In electronics, this is frequently the function of injection-molded parts. Insulators, these components help effectively isolate electrical conductors, preventing current flow through the system.
One example would be using plastics such as PC and ABS to produce electronic casings, light switches, and other electrical components.
Dashboards:
Lastly, we have dashboards in our list of examples of products made by injection molding. A dashboard is one of the components of an automobile that is used the most frequently. The use of injection molding streamlines the manufacturing process for this component. Structures such as an airbag frame, interior trim panel, windpipe, portable ashtray, sub-instrument panel body, and dashboard lower body are more straightforward.
In manufacturing automobile dashboards, several distinct injection molding processes are utilized, including gas-assisted injection molding, sequence valve injection, and composite injection. Furthermore, instrument panel insert injection, moldeo por inyección bicolor, and double injection of the instrument panel are other techniques that can be performed.
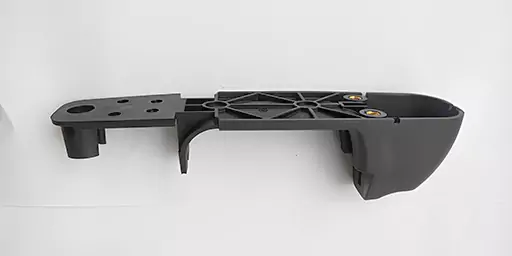
Conclusión:
Apart from all these widely used, common, and popular industrial products manufactured through the injection molding process, there are many more products made by injection molding, including industrial products like press fittings, lifestyle products like phone covers, and much more.
All in all, there are endless products made by injection molding used in different industries today, including sports, food, home, toys, medical, residential, commercial, automotive, and even the 3d products industry.