SMED o Single Minute Exchange of Die es el proceso de minimizar el tiempo de cambio o preparación. Implica identificar y eliminar cualquier aspecto innecesario del proceso de transición. Cuando es necesario sustituir una pieza de un equipo industrial, el tiempo de inactividad puede ser costoso e inesperado. El SMED es esencial para la fabricación ajustada, ya que puede eliminar residuos, aumentar la productividad y reducir costes.
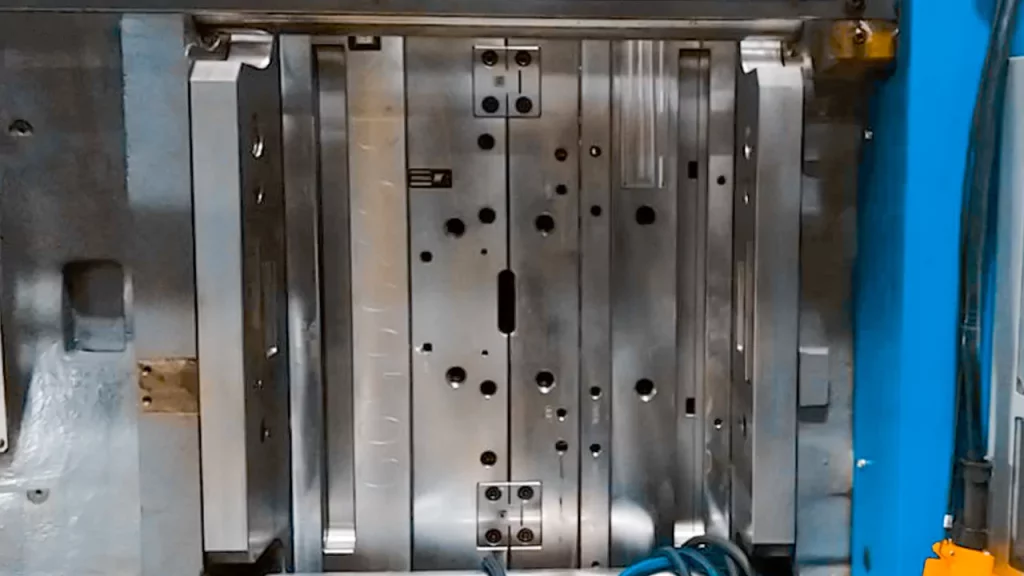
Sin embargo, hay mucho más en lo que esta estrategia es, lo que ofrece, y cómo ofrece que un simple significado de forma completa cuando se trata de adoptarlo. Vamos a repasarlo todo en detalle.
Los fundamentos del intercambio de troqueles en un solo minuto:
El sistema SMED es un principio de fabricación ajustada que consigue más con menos, al tiempo que proporciona el máximo valor al cliente. Su objetivo es acortar el tiempo necesario para completar los cambios en las máquinas de los equipos. Esto incentiva al personal de la planta a completar tantos procesos como sea posible antes del cambio, a tener equipos trabajando en paralelo y a contar con un procedimiento de trabajo estandarizado y optimizado.
El objetivo es acortar el tiempo de cambio de horas a menos de diez minutos, de ahí el Single Minute Exchange of Dies. Los troqueles son herramientas de fabricación especializadas que deben volver a configurarse cuando cambian los modelos de producción, lo que provoca tiempos de inactividad. Shigeo Shigoingeniero industrial japonés, se le atribuye la invención del sistema SMED. Utilizando esta estrategia, redujo en 94% los tiempos de cambio en las empresas con las que trataba. Sólo a veces es posible reducir el tiempo de cambio de maquinaria a menos de 10 minutos, pero en la mayoría de los casos es factible.
¿Por qué es importante el SMED?
La fabricación ajustada busca minimizar los residuos y aumentar la eficiencia siempre que sea posible dentro de un sistema determinado.
Según la metodología Lean, el despilfarro es una de las tres áreas clave que hay que abordar: la pérdida de Muda, Muray Muri. El intercambio de troqueles en un solo minuto es responsable de estos tres tipos de residuos. Sin embargo, la eliminación de mura es el principal problema (desnivel).
A la hora de satisfacer las expectativas de los clientes, cada lote más pequeño debe poder procesarse para establecer un flujo de proceso fluido y predecible. La necesidad constante de actualizar los equipos es el principal impedimento para fabricar volúmenes más reducidos. Estos cambios llevan mucho tiempo y son costosos, y deben amortizarse con un enfoque más práctico para ser rentables.
Dado que el periodo de cambio de algunas piezas de maquinaria puede durar varias horas o incluso días, es necesario maximizar la producción de máquinas específicas en términos de su tiempo productivo ocupado. Al maximizar el tamaño de los lotes, se consigue un uso más eficiente de los recursos disponibles. Sólo cuando es necesario cambiar el proceso se ponen de manifiesto las ineficiencias.
La reducción de los tiempos de preparación para cada cambio es esencial si se quieren producir lotes más pequeños de forma económicamente viable. En consecuencia, la preparación interna debe minimizarse al máximo para que el tiempo de cambio tenga el menor impacto posible en el proceso de fabricación.
Sus componentes:
En SMED o Single Minute Exchange of Dies, los cambios se construyen a través de una serie de procesos conocidos como elementos. Los elementos se clasifican en dos tipos:
- Componentes internos
Estos elementos deben aplicarse o actualizarse después de apagar el dispositivo. Algunos ejemplos son:
- Eliminación de herramientas obsoletas.
- Sustituyéndolos.
- Ajuste del avance del material.
- Modificación de los parámetros del programa.
Considérelo como una parada en boxes de Fórmula Uno. El automóvil entra en boxes, se detiene y los miembros de la tripulación cambian los neumáticos.
- Factores externos
Cuando el gadget está en uso, pueden aplicarse o añadirse elementos externos. La compra de nuevas alimentaciones de material, la adquisición de nuevas herramientas, la devolución de herramientas antiguas o el almacenamiento de herramientas antiguas, la documentación de procesos adecuados o la solicitud de licencias son algunos ejemplos. Mientras el coche está todavía en el circuito, el equipo ya está preparando los neumáticos, preparando las herramientas y colocando a los técnicos. Como resultado, el equipo puede terminar la operación en su totalidad en cuestión de segundos una vez que el automóvil se detiene.
Procedimiento SMED:
El procedimiento SMED (Single Minute Exchange of Dies) consta de varios pasos. Puede aplicar este enfoque LEAN:
1. Mantenga separados los procesos de configuración internos y externos.
Durante este paso se identifican los elementos que intervienen en el proceso de cambio y que pueden gestionarse con pocos o ningún cambio mientras el equipo de producción está en funcionamiento y, a continuación, se llevan a cabo antes o después del cambio. Es habitual que este procedimiento suponga una reducción 50% de los tiempos de cambio.
El equipo debe preguntarse si cada elemento y subproceso puede realizarse mientras el equipo está en funcionamiento. Si la respuesta es verdadera, el elemento es externo.
2. Normalizar los procesos de configuración externa
Todas las fases externas pueden identificarse y normalizarse mediante películas o diagramas de flujo durante esta fase. Esto significa que puede completar dichas tareas mientras el procedimiento está en marcha. Si no se hace con cuidado, puede haber ocasiones en las que haya que recoger las herramientas cuando las máquinas no estén en marcha. Esto alarga el tiempo de cambio más de lo necesario.
3. Cambiar los procesos de configuración internos por procesos de configuración externos
Durante este paso, se examina exhaustivamente el proceso de cambio para convertir en externos tantos elementos internos como sea factible. Durante este paso, el equipo debe considerar si existe una forma de convertir los elementos internos en externos, cuál sería ese enfoque y cómo hacerlo.
El resultado es una lista de elementos que puede llevar más lejos. Esta lista de prioridades es similar a un análisis coste-beneficio en varios aspectos.
4. Mejorar los procesos de comunicación interna
"Sólo la última vuelta del tornillo bloquea la pieza en su sitio". Shigeo Shingo dijo una vez. Lo que queda después de esto es sólo movimiento, y eso se puede descartar.
El concepto es que el perno, por ejemplo, puede sustituirse por abrazaderas más cortas, accionadas por resorte, que sujetan la pieza en su sitio. Ahora se ahorra el tiempo que antes se dedicaba a girar el perno. Varias máquinas o herramientas se modifican para proporcionar tamaños estándar. Además, también se pueden reducir los puntos de montaje para reducir el número de pasos necesarios para completar el trabajo.
5. Mejorar los procedimientos de configuración externa
En esta fase se evalúan los demás elementos externos. La idea es agilizar y simplificar estos procesos para ahorrar tiempo.
Al igual que en los pasos anteriores, el equipo evalúa cómo ejecutar esta parte en menos tiempo. ¿Cómo podemos hacerlo más sencillo? Un análisis coste-beneficio también es beneficioso para evaluar si es lo suficientemente eficiente.
6. Repita SMED varias veces.
Puede ahorrar tiempo regularmente analizando meticulosamente todo el proceso una y otra vez. Por ejemplo, las nuevas tecnologías u otros conocimientos importantes ofrecen posibilidades de optimizar el proceso mediante el análisis de vídeo.
Los beneficios:
Si se utiliza correctamente el método de Cambio de Matrices en un Minuto, se obtienen las siguientes ventajas. Entre todas las ventajas, la más destacable es que el Cambio de Troqueles en un Minuto o SMED ofrece una mayor productividad. Veamos ahora algunas ventajas adicionales:
- Aumento de la productividad: Cuando se reduce el tiempo necesario para los cambios, aumenta el número de mercancías producidas en un periodo acordado, así como el tiempo de trabajo. Se elimina el "Muda" sin valor añadido.
- Es concebible un proceso de fabricación flexibleporque sólo es posible producir una cantidad modesta de bienes y porque el cambio entre distintos tipos de bienes es sencillo.
- Mejora de la satisfacción del cliente: Aumenta la satisfacción del cliente porque sus necesidades se satisfacen a tiempo.
- Mejora de la calidad de los productos: Esto ayuda a reducir el número de mercancías defectuosas generadas durante la puesta a punto de las máquinas.
- Reducir el coste del mantenimiento de inventarios: La producción ajustada, que permite una menor producción y elimina la necesidad de almacenar productos, reduce los gastos asociados a la gestión de inventarios.
- Reducir el coste de mantenimiento: Al ser necesarias menos operaciones manuales, ajustes y apilamientos, se reducen los riesgos de que las matrices se caigan, golpeen o sufran daños físicos.
- Reducción de los accidentes laborales: El número de accidentes laborales a lo largo de este proceso ha disminuido debido a que el proceso de preparación es más fácil y corto.
Conclusión:
El objetivo de la fabricación ajustada digital es eliminar los residuos. Los fabricantes están tomando iniciativas para mejorar los flujos de trabajo de los materiales tras el cambio para conseguir tiempos de puesta en marcha aún más rápidos utilizando SMED o Single Minute Exchange of Dies. Un sistema inteligente y conectado línea de fabricación ofrece a las empresas aún más información sobre el funcionamiento y la eficacia de sus artículos.