En règle générale, la décision de choisir un moule d'injection dépend du type de produit, de sa conception, du volume de production et du budget. Cependant, même après avoir fait le tri, comment savoir quel est le meilleur moule ? Moule à 2 assiettes ou à 3 assiettes?
Ce guide détaillé vous aidera à comprendre l'utilisation, les avantages, les inconvénients et les différences des deux moules.
À la fin de ce blog, vous serez mieux à même de choisir entre Moule à 2 assiettes ou à 3 assiettes pour vos besoins de production. Poursuivez votre lecture !
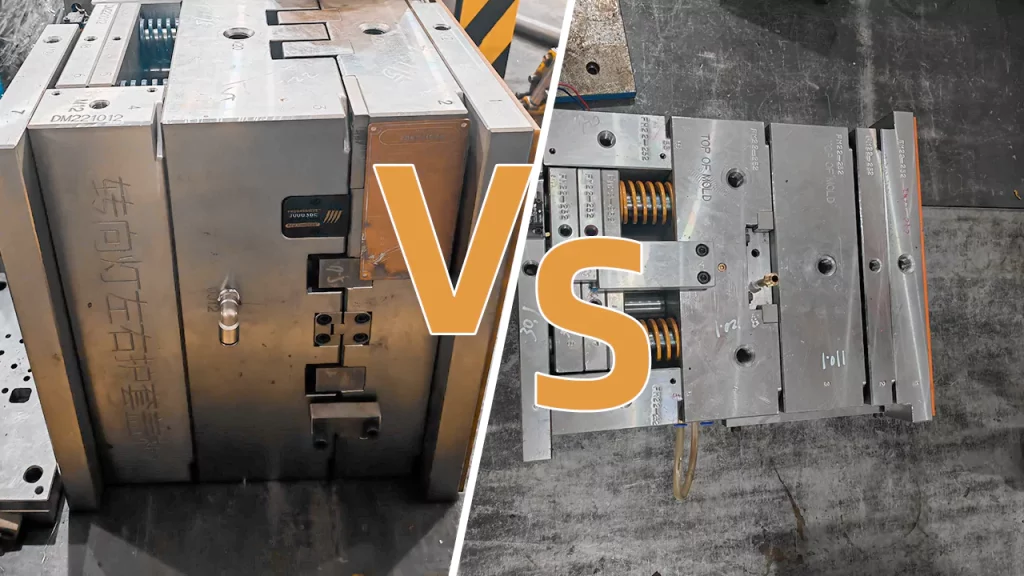
Qu'est-ce qu'un moule à 2 plaques ?
Il s'agit du type de moule le plus fondamental, fréquemment utilisé pour produire des articles en plastique bon marché. Il comporte une cavité, un noyau et deux spits au niveau de la ligne de séparation. Il part dans l'espace en une seule étape. Les coureur et porte doit être positionné près de la ligne de démarcation à l'aide d'un moule à deux plaques.
Par conséquent, lors de l'utilisation du couloir, il est important d'évacuer la pièce et il est nécessaire de la décomposer individuellement. Cependant, il ne faut pas utiliser le moulage à deux plaques, même s'il s'agit d'une alternative plus simple et moins coûteuse qui permet de produire des biens de haute qualité.
Lire aussi : Les types de services et de processus d'usinage les plus courants
Comment cela fonctionne-t-il ?
Lorsque l'on compare les Moule à 2 assiettes ou à 3 assiettesIl est important de comprendre le fonctionnement de ces deux moules.
Aujourd'hui, le moule à deux plaques est un choix courant pour la production de composants en plastique bon marché. Il comporte une cavité et un noyau, séparés au niveau du plan de joint, et il s'ouvre en une seule étape du processus.
C'est pourquoi, en ce qui concerne la structure de ce moule, il est important d'aligner la porte et la glissière sur la ligne de séparation. Cela permet à la coulisse de sortir lors de l'éjection d'une pièce, alors qu'une procédure distincte est nécessaire pour la casser.
Après le moulage, le produit moulé par injection et le patin restent du côté qui se déplace. Par conséquent, le produit et le système d'éjection seront éloignés de la même surface de séparation.
Ensuite, lorsque le moule s'ouvre, les produits sont poussés hors du moule par le côté mobile du moule qui contient le système d'éjection. Le moule à deux plaques étant simple et économique, il n'est pas recommandé de l'utiliser pour fabriquer un produit de haute précision.

Avantages :
L'utilisation d'une procédure appelée "moulage par injection à deux plaques" présente plusieurs avantages, dont les suivants :
- Les moules à deux plaques peuvent être construits pour traiter différentes conceptions et tailles de pièces et peuvent fonctionner aussi bien pour le développement que pour les séries de production. Les moules à deux plaques disposent donc d'une grande marge de manœuvre en termes d'applications.
- La conception et la construction d'un moule à deux plaques sont assez simples, ce qui permet de réduire au minimum les coûts initiaux du moule et les coûts de maintenance ultérieurs.
- Les moules à deux plaques sont souvent moins coûteux à construire que les moules à plusieurs plaques, et leur entretien est également moins onéreux. Ces avantages contribuent à leur rentabilité.
Lire aussi: Comment réduire le coût des pièces CNC ?
- Les temps de cycle sont généralement beaucoup plus courts que ceux d'un moule à trois plaques parce que la plaque B n'a pas besoin de tourner pour faire de la place pour le retrait de la pièce. Le temps de cycle de ce type de moule est donc généralement beaucoup plus court que celui d'un moule à trois plaques.
- Les moules à 2 plaques sont un excellent choix pour la production de petites pièces avec des contre-dépouilles minimales ou des géométries complexes. Ces moules peuvent s'adapter à une large gamme de tailles de pièces.
- En raison de la nature simple de la conception, il est plus facile d'adapter le moule à de nouvelles conceptions ou à des ajustements dans le processus de fabrication.
- Le système d'éjection est simple et permet d'extraire facilement les composants du moule.
Inconvénients :
Bien que l'utilisation d'une méthode de moulage par injection à deux plaques présente de nombreux avantages, il convient de prendre en compte certains inconvénients, notamment les suivants :
- Il peut y avoir un flash lors de l'utilisation de moules à deux plaques, car la pression d'injection est plus élevée entre les deux plaques (plan de joint). S'il y a plus de cavités dans le moule et que l'ajustement entre les deux plaques n'est pas exact, un surplus de plastique peut s'échapper du moule, ce que l'on appelle communément la bavure.
- L'extraction du noyau nécessite une opération supplémentaire, ce qui augmente la durée totale du cycle et peut faire grimper les prix. Les noyaux complexes nécessitent ce processus supplémentaire.
- Lorsque l'on compare les Moules à 2 assiettes ou moules à 3 assiettesles moules à deux plaques ont une conception plus simple et moins de caractéristiques, ce qui peut se traduire par une durée de vie plus courte. Cela peut limiter le nombre de fois où vous pouvez utiliser le moule.
- Parce qu'ils ne peuvent accueillir qu'un seul plan de séparation, les moules à deux plaques ne sont pas idéaux pour la conception de pièces comportant des contre-dépouilles ou d'autres géométries complexes. En effet, les moules ne peuvent accueillir qu'un seul plan de séparation.
- Vous pouvez être confronté à des restrictions en ce qui concerne l'emplacement du portillon et les options de conception, car les moules à deux plaques n'ont souvent qu'un seul emplacement pour le portillon, ce qui réduit le nombre de possibilités disponibles.
- Les moules à deux plaques ont une capacité limitée à contrôler le temps de refroidissement du produit, ce qui peut avoir un impact sur la qualité globale du produit fini.
- Les moules à deux plaques ne sont pas adaptés à une cavitation élevée, car la plaque B doit être ouverte à chaque fois qu'elle expulse une pièce. Cela peut ralentir le processus de production.
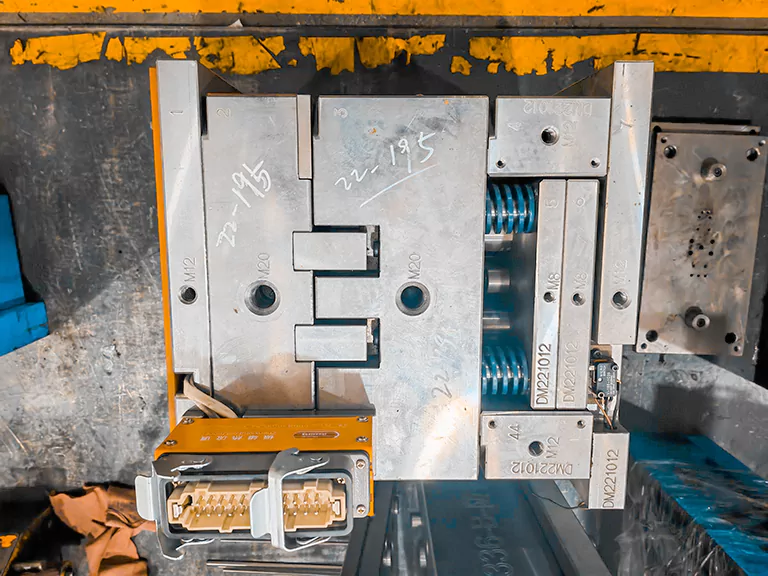
Qu'est-ce qu'un moule à 3 plaques ?
La différence la plus fondamentale entre un Moule à 2 plaques et moule à 3 plaques est que ce dernier type contient une plaque de coulissage supplémentaire. Il maintient donc le patin à l'intérieur de la plaque de patin, et vous êtes libre de positionner le patin où bon vous semble.
La position de la porte offre également l'avantage de pouvoir la placer n'importe où. Le moule se démonte en deux étapes distinctes. Bien que le coût du moule augmente avec la présence d'une plaque de coulée, les moules à trois plaques constituent la meilleure option pour la production de pièces de précision de haute qualité.
Comment cela fonctionne-t-il ?
Initialement, le noyau et la cavité d'un moule à trois plaques ne seront pas distincts lors de l'ouverture du moule. C'est pourquoi la plaque de démoulage et la plaque de la cavité doivent être séparées l'une de l'autre. La plaque de démoulage séparera le produit moulé du matériau de la porte au cours de la deuxième étape du processus.
Finalement, le noyau et la cavité se désengagent l'un de l'autre pour faciliter l'expulsion du produit. L'injection, le refroidissement et le retrait des produits sont les phases du processus de moulage par injection de plastique qui se déroulent dans une machine à trois plateaux.
Deux lignes de séparation et trois séquences d'ouverture sont présentes dans la conception du moule d'injection à trois plaques. Ces séquences d'ouverture comprennent l'ouverture du canal, l'ouverture du produit et l'ouverture de la plaque de démoulage du canal. En outre, ce moule particulier comporte deux lignes de séparation ; l'une est utilisée pour retirer le produit, tandis que l'autre permet de retirer un canal de coulée.
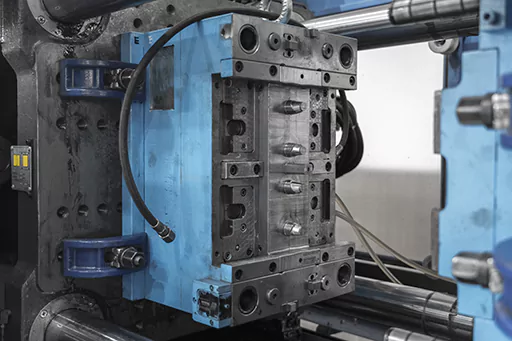
Avantages :
L'utilisation d'un moule à trois plaques présente les avantages suivants :
- Les patins et les portes peuvent être expulsés du processus d'ouverture du moule grâce à leurs plaques de démoulage uniques. Vous n'aurez donc pas à effectuer la tâche laborieuse consistant à retirer les barrières des composants.
- La conception des trois portillons permet de les placer sur le dessus ou le dessous de la pièce à n'importe quel endroit de la surface, ce qui permet de produire des pièces avec des finitions de qualité supérieure.
- Comme le plastique fondu peut s'écouler si facilement, il n'y aura pas de problème de court-circuit avec votre composant.
Inconvénients :
Les inconvénients courants de ce type de moule sont les suivants :
- Par rapport aux moules à deux plaques, le coût de fabrication est plus élevé, le coût d'usinage est plus élevé, le poids du moule augmente et le délai d'exécution est plus long.
- Un gaspillage de résine en raison de la longueur de la coulisse ;
- La conception des moules est un processus plus complexe.
Conclusion : Quel est le meilleur moule ?
En résumé, la distinction essentielle entre un Moule à 2 plaques et moule à 3 plaques est que, dans le premier cas, le patin est situé sur la plaque A ou B, qui se trouve sur la couche du plan de joint. Elle est également éjectée par les systèmes d'éjection en même temps que la pièce.
En revanche, dans le moule à trois plaques, le patin adhère à la plaque C (plaque de patin), puis est éjecté par le poussoir. Ce type de moule est plus complexe et plus coûteux que le moule à deux plaques.
En outre, le moule à deux plaques est beaucoup plus simple et moins coûteux. En revanche, les professionnels proposent rarement des moules à trois plaques, car ils présentent plusieurs inconvénients et leur structure est nettement plus complexe, avec un taux de rebut plus élevé.
Lorsqu'il s'agit de choisir entre Moule à 2 assiettes ou à 3 assiettesEn revanche, ce dernier manque de stabilité en raison d'un mécanisme complexe et nécessite un temps de cycle plus long. Vous aurez également besoin d'une machine de moulage par injection plus grande pour utiliser ces moules, car la distance de passage est plus longue qu'avec un moule à deux plaques.
Pour plus de détails et de questions, contactez nos professionnels à Prototool.com.