For the manufacture of tiny, medium, and large-sized plastic parts, molds for plastic injection is the most often utilized manufacturing technique. An injection molding machine, unprocessed plastic, and a mold are all used in the procedure. After being heated to molten plastic in the machine, the plastic will be injected into the cavity, where it cools and hardens to form the finished product.
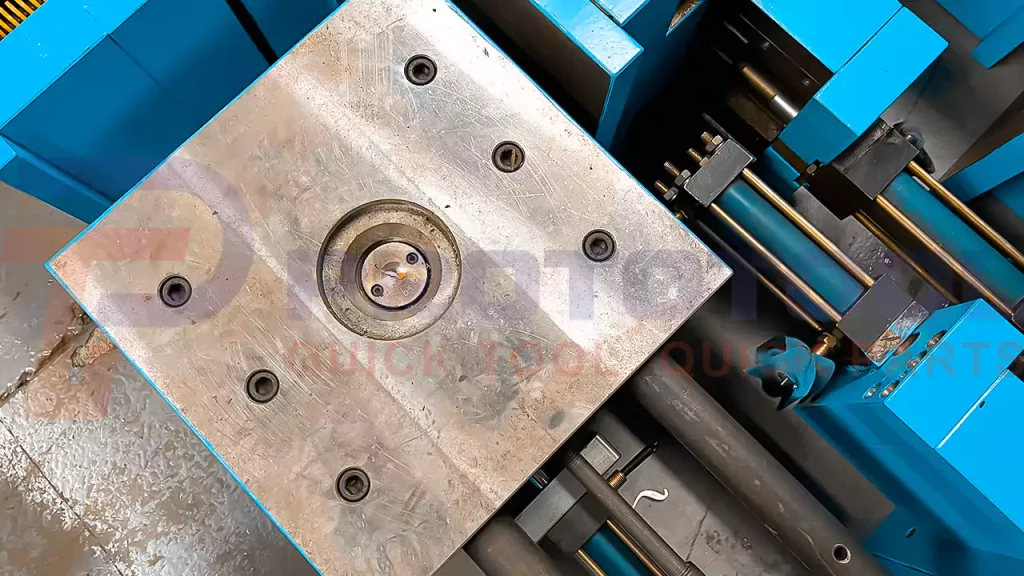
Nearly all industries, including the automotive, medical, small engine, plumbing, industrial, agricultural, and others, use plastic parts in their products. Manufacturers can make ultra-high-quality plastic components at the fastest possible rate and with the highest degree of accuracy by utilizing the most recent molds for plastic injection technology and manufacturing techniques.
What varieties of plastic injection molding are there?
Plastic injection molding is not a universal technique. To attain various end goals, we can apply several strategies.
- Standard molding:
This straightforward method produces the item using just one color and material. This type of mold for plastic injection is frequently employed in producing toys, auto parts, and everything from drinks containers to caps.
A curved handle with a soft outer substance that makes it easy to grip is an example of an object that can be produced using this two-step method and requires two distinct types of plastic. A thermoplastic is then molded over the created substrate once the substrate portion is first made. Following this, each part is transferred individually to different molds for plastic injection. Mechanics or chemistry can be used to bind the two materials together.
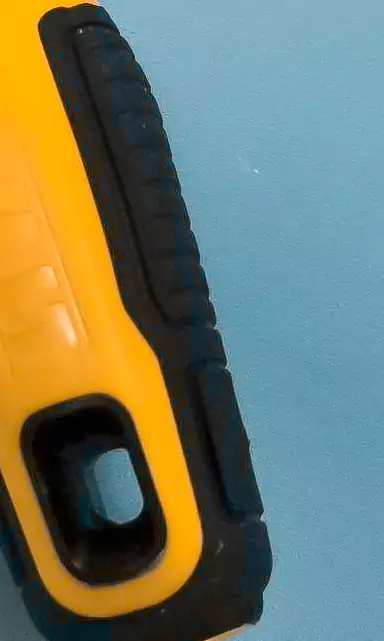
- Insert Molding:
When insert molding is utilized, a premade part serves as the substrate. A substance other than plastic might be used to create this substrate. Examples of insert molding include dials and knobs that have a plastic shell covering a metal interior. Plastic is first injected onto the substrate after it has been placed into the mold. As the overmolding substance, thermoplastic resin is typically used in this technique.
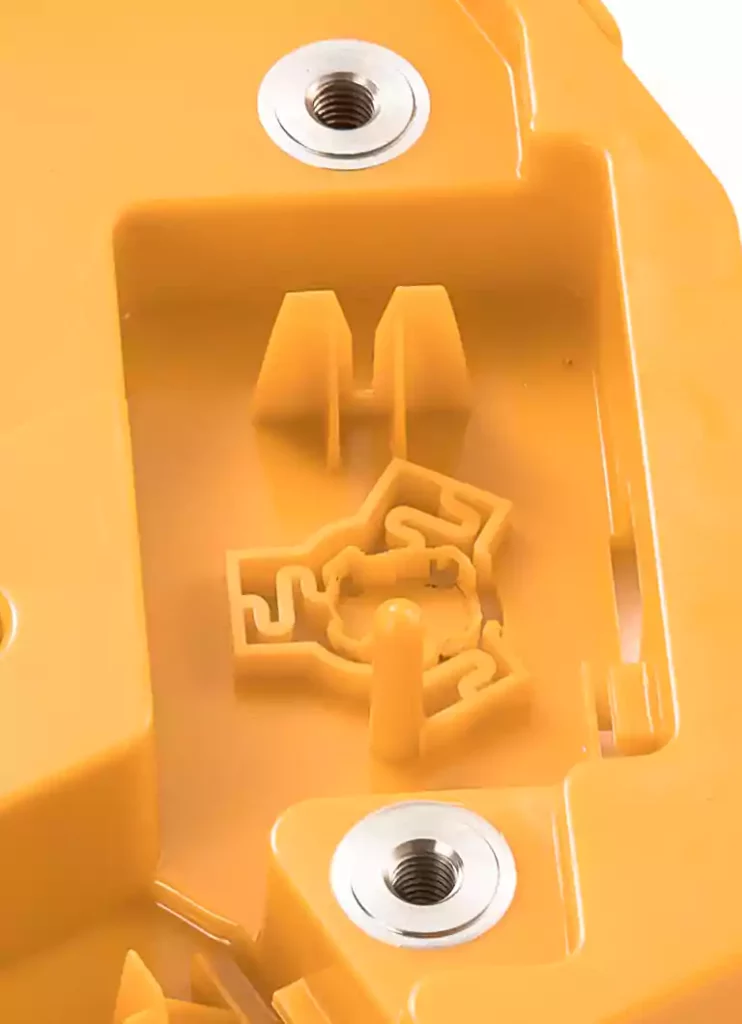
- Molding in two shots (dual shots):
This technique is carried out in a single molding press. It enables you to concurrently make a part or product utilizing a variety of colors and plastic kinds without needing to employ a multi-stage assembly procedure.
As an illustration, you should design a power tool housing with a handle that matches your brand. By use of the primary press barrel, a substrate is first introduced. The second injection unit then molds the second shot after the mold steel has been replaced. Both chemical and mechanical bonds can be present between the materials.
The components of an injection molding machine:
A material hopper, a barrel, an injection ram or spinning screw, a heating element, a changeable pattern, ejectors, and a mold inside the mold cavity make up molds for plastic injection machines. Machines typically operate horizontally. A die’s opening and die’s closing, as well as the ejection of pieces, are functions of the clamping unit. There are two different kinds of clamping techniques: the toggle type that is displayed and the straight-hydraulic type that enables a mold to open and close directly using a hydraulic cylinder.
An electric motor powers a hydraulic rotating screw, which is situated at one end of the barrel. Plastic added from the hopper is twisted by the screw to melt it. The molds procedure begins once the necessary volume of molten plastic has been gathered. An attached mold is located on the barrel’s opposite side.
The molds in injection machines regulate the screw’s speed as molten plastic flows through the mold (or the injection speed). In addition, it regulates pressure as plastic is used to fill the voids. The speed control and pressure control are set where the screw position and injection pressure reach a certain value.
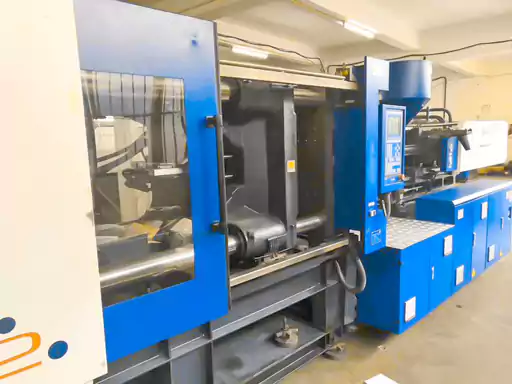
An injection mold’s composition:
The high-strength metal parts that are machined in half form the mold for plastic injection. Through the use of runners, gates, and a sprue, molten plastic pours into a mold and fills any openings. After the cooling process, the mold is opened, and the moldings are ejected using the ejector rod and plate of the injection molding machine.
When it comes to functioning efficiently throughout the molds for the plastic injection process, an injection mold’s composition is important. Even though molds typically have two halves—a cavity side and a core side—each half is frequently made up of numerous precise features.
What steps comprise the process of plastic injection molding
Usually lasting between six seconds and two minutes, the injection molding manufacturing cycle is extremely brief. The procedure is divided into the following steps:
Clamping
The two parts of the mold must first be tightly closed by the clamping mechanism before the heated plastic material is injected into the mold. The mold’s two sides are pushed together by the clamping unit’s powerful force, which also maintains the mold shut and securely closed while the material is injected. The machine’s size and the size of its apertures will determine how long it takes to close and clamp the mold. Larger machines take longer.
Injection
The injection unit feeds the molds for the plastic injection machine with raw plastic material, which is typically in the form of tiny pellets that are then augered or transported towards the mold. The plastic substance warms up as the screw drives the plastic pellets through hot sections of the machine barrel, owing to temperature and compression.
A precise fraction of the molten plastic that is transferred to the screw’s face before injection will turn into the finished product. Once the machine is fully clamped, the material is injected into the mold in a quantity known as the shot. Shot volume, injection pressure, and part shape are all factors that can be used to predict injection time.
Cooling
Upon coming into contact with the internal surfaces of the molds, the molten plastic inside begins to cool. The freshly molded plastic object becomes more hard and solid in shape throughout the cooling process. It’s vital to remember that portion shrinkage could happen as the material cools.
It is only possible to open the mold after the required cooling period has passed. Every plastic-molded item has cooling requirements, which are determined by the thermodynamic characteristics of the plastic, the part’s wall thickness, and the finished part’s dimensional specifications.
- Ejection:
It is possible to use the ejection mechanism to remove the part from the mold after it has cooled inside it. The part is ejected from the mold with the vital force thanks to the mechanical components of molds for the plastic injection machines. When the part is expelled, the mold is prepared for the next part. Throughout this procedure, the machine has been preparing a fresh plastic shot.
What takes place during post-processing for plastic injection molding?
Frequently, post-processing applications are needed after the injection molding procedure. This could involve additional procedures used for decoration or practicality. There are six typical types of post-processing applications for injection molding.
- Gate edging
- Painting
- Utilizing a laser
- Printing on pads
- Fire staking
- Sonic wave welding
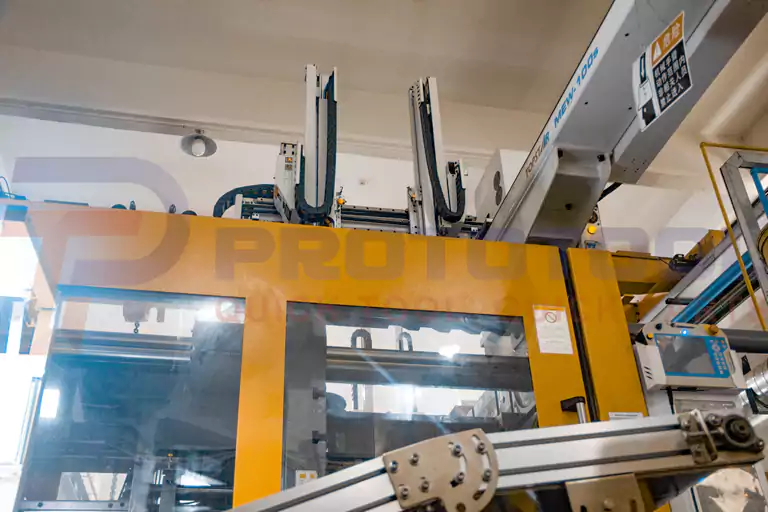
What benefits does plastic injection molding offer?
Molds for plastic injection are a fantastic option for producing a huge variety of parts and goods due to their aesthetic and functional adaptability. The following are important benefits:
Higher Standard:
Precision and consistency are produced in pieces produced via injection molding. In reality, when compared to other methods of producing plastics, injection-molded parts have very good dimensional consistency. Additionally, there are a lot of data-driven injection molding techniques and tools that support a part’s overall quality.
Compatible design:
Computer-aided design (CAD), computer-aided manufacturing (CAM), and SolidWorks are all easily integrated with injection molding. As a result, while using this procedure to create simple objects is a smart idea, it is also useful for creating intricate or very complex parts and when a component’s precise criteria must be satisfied.
Various color options:
To create almost any shade or visual impact, colorant producers have access to a wide variety of hues.
Adaptable product characteristics:
Plastics come in more than 15,000 different varieties on the market to produce the necessary functional outcomes. Additionally, fillers like glass fibers are added to boost strength, and UV protection can be added to objects that will be exposed to the sun to increase their durability.
Compliance:
Resins that abide by FDA, NSF, REACH, and RoHS regulations are readily available when needed.
Sustainability:
Because molds are so precise and effective, it generates very little waste, and any extra material can frequently be recycled.
Cost-effectiveness and speed:
It is particularly effective since injection molding is a fairly straightforward technique that is also highly automatable. This shortens the production process, which could increase profits while also saving money.
Lightweight:
Despite being much lighter than metal or other materials used for typical parts, plastic is a robust substance. Due to this, many manufacturers think that switching out metal or steel parts for plastic ones through metal-to-plastic conversion is a good idea.
PROTOTOOL is your finest option if you’re searching for a high-quality mold for a plastic injection supplier. They provide the greatest solutions while ensuring that all of your needs are addressed with pleasure.