Typically, the decision to choose an injection mold depends on the type of product, its design, production volume, and budget. However, even after you have all this sorted, how do you know which mold is better: 2 plate mold or 3 plate mold?
Don’t worry if you’re confused; this detailed guide will help you understand both molds’ usage, advantages, disadvantages, and differences.
By the end of this blog, you can better choose between 2 plate mold or 3 plate mold for your production needs. So keep reading!
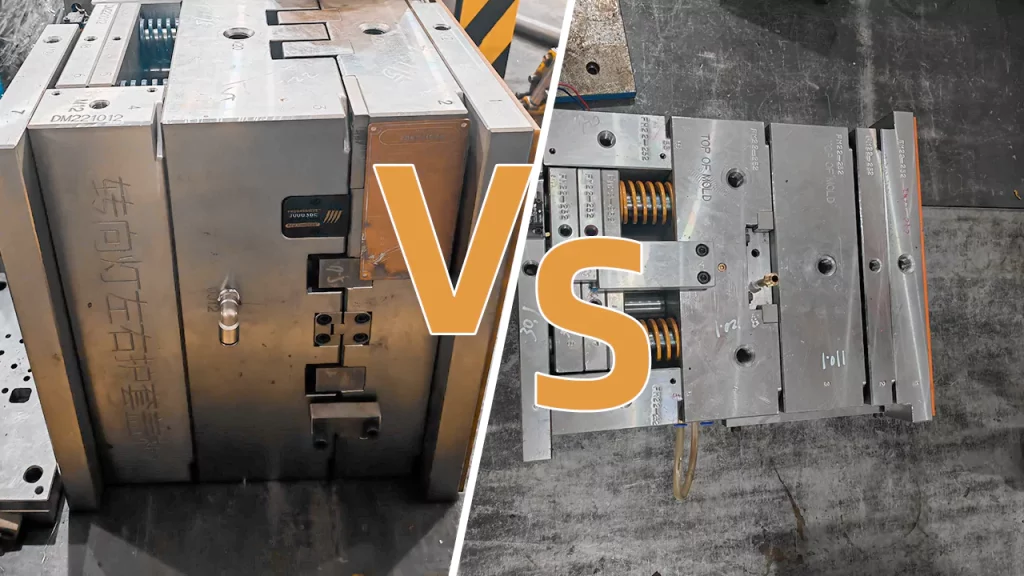
What is a 2 Plate Mold?
This is the most fundamental mold type, frequently used to produce inexpensive plastic goods. It has a cavity, a core, and two spits at the dividing line. It goes off into space in a single stage. The runner and gate must be positioned near the dividing line using a two-plate mold.
Consequently, when using the runner, it is important to evacuate the part, and it is necessary to break it apart individually. However, you should not use two-plate molding, even if it is a simpler and less expensive alternative that can produce high-quality goods.
Also Read: The Most Common Types of Machining Services and Processes
How Does It Work?
When comparing 2 plate mold or 3 plate mold, it’s important to understand how both these molds work.
Now the two-plate mold is a common choice for producing inexpensive plastic components. It has a cavity and a core, separated at the parting line, and it opens using only one stage of the process.
Hence, when it comes to the structure of this mold, it is important to align the gate and the runner at the separating line. This allows the runner to come out when you eject a part while necessitating a separate procedure to break it.
After molding, the injection-molded product and the runner stay on the side that is moving. As a result, it will propel the product and the ejection system away from the same parting surface.
Later, once the mold opens, the goods are pushed away from the mold by the moveable mold side that contains the ejection system. Since a two-plate mold is straightforward and economical, you should not consider using it to make a high-precision product.

Advantages:
Using a procedure called “two plate injection molding” has several benefits, including the following:
- Two-plate molds may be constructed to handle various part designs and sizes and can work for both development and production runs. This gives two-plate molds a lot of leeway in terms of their applications.
- Designing and constructing a two-plate mold is quite straightforward, which helps keep the initial mold and subsequent maintenance costs to a minimum.
- Two-plate molds are often less expensive to build than multi-plate molds, and they also require less money to maintain. These advantages contribute to their cost effectiveness.
Also Read: How to Reduce the CNC Parts Cost?
- Cycle Times Are Typically Much Shorter Than Those of a Three-Plate Mold Because the B plate does not need to spin to make room for the removal of the part. Hence, the cycle time for this type of mold is typically much shorter than that of a three-plate mold.
- 2 plate molds are an excellent choice for producing small parts with minimal undercuts or complex geometries. These molds can accommodate a wide range of part sizes.
- Because of the straightforward nature of the design, it is easier to adapt the mold to new designs or adjustments in the manufacturing process.
- The ejection system is straightforward, allowing you to easily extract the components from the mold.
Disadvantages:
Although there are many benefits to employing a two-plate injection molding method, there are also certain drawbacks that you should consider, including the following:
- There can be a flash when using two-plate molds because there will be higher injection pressure between the two plates (parting line). If there are more cavities in the mold and the fit between the two plates is not exact, surplus plastic can seep out of the mold, commonly referred to as flash.
- Pulling the core requires an additional operation, which adds to the total cycle time and can drive up prices. Complex cores necessitate this additional process.
- When comparing 2 plate molds or 3 plate molds, two-plate molds have a simpler design and fewer features, which can result in a shorter lifespan. This can limit the number of times you can use the mold.
- Because they can only accommodate a single plane of separation, two-plate molds are not ideal for the design of parts that include undercuts or other complex geometries. It is because the molds can only accommodate a single plane of separation.
- You may face restrictions in gate placement and design options because two-plate molds often only have a single spot for the gate, reducing the number of possibilities available.
- Two-plate molds have a restricted ability to control the amount of time the product is allowed to cool, which can impact the overall quality of the finished good.
- Two-plate molds are inappropriate for high cavitation because the B plate requires an opening every time it expels a part. This can cause the production process to move more slowly.
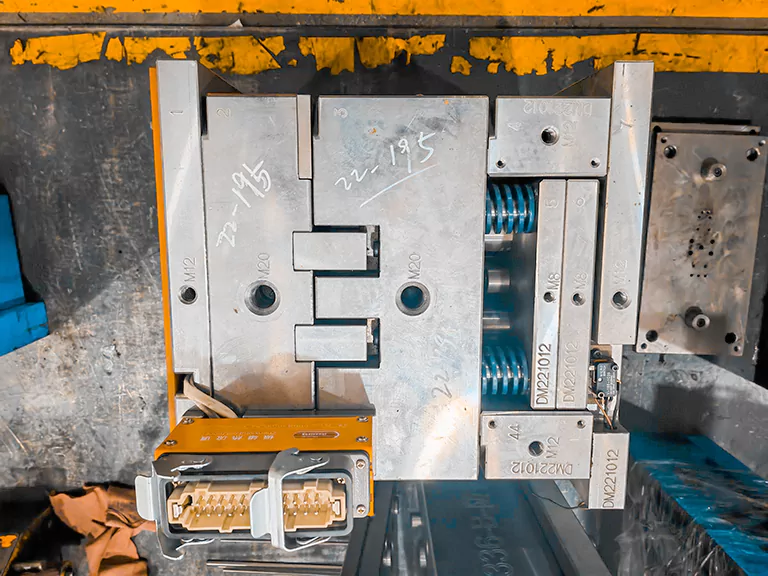
What is a 3 Plate Mold?
The most fundamental difference between a 2 plate mold and 3 plate mold is that the latter type contains an additional runner plate. Therefore, it keeps the runner within the runner plate, and you will be free to position the runner wherever you see fit.
The position of the gate also provides the advantage of being able to place it wherever. The mold breaks apart in two distinct stages. Although the cost of the mold will increase with the presence of a runner plate, three-plate molds are the greatest option for producing precision parts of a high grade.
How Does It Work?
Initially, the core and cavity of a mold with three plates won’t become distinct when the mold opens. Therefore, the stripper plate and cavity plate should separate from one another. The stripper plate will separate the molded product from the gate material during the second step of the process.
Eventually, the core and cavity will disengage from one another to facilitate the product’s expulsion. Injection, cooling, and removal of products are the phases of the plastic injection molding process that occur in a machine with three plates.
Two separation lines and three opening sequences are present in the three-plate injection mold’s design. These opening sequences include a runner opening, a product opening, and a runner stripper plate opening. In addition, this particular mold has two separation lines; one is used to remove the product, while the other helps to remove a runner.
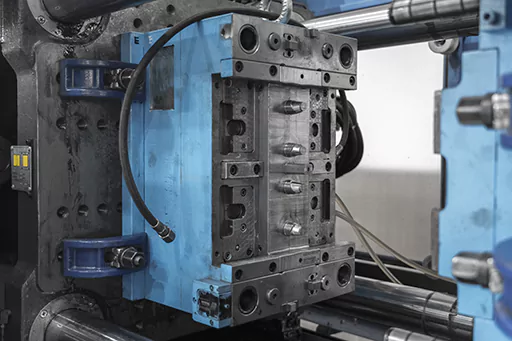
Advantages:
The benefits of using a three-plate mold include the following:
- Runner and gates could be expelled from the mold opening process by their unique stripper plates. As a result, you would not have to do the laborious task of removing gates from the components.
- Because the design of the three gates allows the gates to be set on either the top or bottom of the component at any point on the surface, you can produce parts with superior finishes.
- Because the molten plastic can flow so readily, there won’t be an issue of a short shot with your component.
Disadvantages:
Common disadvantages of using this type of mold include:
- Compared to two-plate molds, the cost of manufacturing is higher; the cost of machining is higher, the weight of the mold increases, and the lead time is longer.
- A waste of resin due to the length of the runner;
- Designing molds is a more complicated process.
Conclusion: Which Mold is Better?
To sum up, the key distinction between a 2 plate mold and a 3 plate mold is that in the former, the runner is located on either the A or B plate, which is situated on the parting line layer. You will also find it eject out by the ejector systems with the part together.
In contrast, in the three-plate mold, the runner will stick with the C plate (runner plate), and later one will be ejected by the pusher and is more complex and expensive than the two-plate mold.
Furthermore, the two-plate mold is far simpler and less expensive. On the other hand, professionals rarely propose three plate molds because they have several downsides and are significantly more complex in structure, with a greater scrap rate.
When deciding between 2 plate mold or 3 plate mold, remember that the latter lacks stability due to a complex mechanism and requires a longer cycle time. You’ll also need a larger injection molding machine to use these molds because the run distance is longer than with a two-plate mold.
For more details and queries, contact our professionals at Prototool.com.