Electric vehicles, a cornerstone of the new energy automotive industry, rely heavily on injection molded parts. These components are integral to various vehicle systems, enhancing functionality and design. In this article, we’ll explore the most common injection molded parts found in electric vehicles.
1. Dashboard Components
The dashboard is not just a display panel; it’s the control hub of an electric vehicle. Modern dashboards use advanced materials like Polycarbonate (PC) or Polymethyl Methacrylate (PMMA) to achieve a user-friendly and aesthetically pleasing design. They house critical electronic components, including display screens and control systems, which are protected by their durable, transparent, and heat-resistant nature.
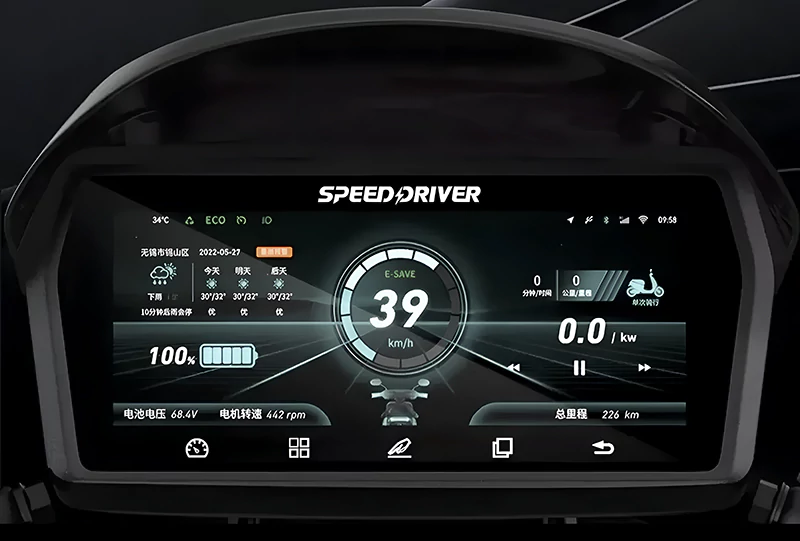
2. Seating Components
Comfort and safety are paramount in vehicle design, and seating plays a crucial role. Injection molded seats made from Polyurethane (PU) or Polyethylene (PE) offer ergonomic support, adapting to the contours of the body. These materials also contribute to the lightweight design of EVs, aiding in energy efficiency. Advanced molding techniques have enabled the integration of smart features like heating and automated adjustments into these components.
3. Bumpers
Bumpers are the first line of defense in a vehicle, designed to absorb impact during collisions. The use of Polypropylene (PP) or Polyamide (PA) in injection molding creates bumpers that are not only strong and impact-resistant but also contribute to the overall aesthetic appeal of the vehicle. Manufacturers can mold these materials into complex shapes and designs, enabling aerodynamic improvements and brand-specific styling.
4. Door Components
Vehicle doors are critical for safety, comfort, and the vehicle’s overall structural integrity. Injection molded doors, made from materials like Polyurethane or Polypropylene, offer enhanced strength-to-weight ratios. This is crucial for EVs, where weight reduction is directly linked to increased range and efficiency. Additionally, these materials provide excellent insulation properties, contributing to noise reduction and thermal management within the vehicle.
5. Engine Covers
In electric vehicles, engine covers serve not only as protective components but also as integral parts of the vehicle’s thermal management system. Materials like Polycarbonate or Polyamide are selected for their high-temperature resistance and durability. These covers also play a role in reducing noise and vibrations, contributing to a quieter and smoother driving experience.
6. Battery Boxes and Modules
The heart of an electric vehicle is its battery system. Battery boxes and modules, often made from ABS or PC, protect the battery cells from environmental factors and mechanical impacts. Manufacturers choose these materials for their strength, thermal stability, and electrical insulation properties. Advanced molding techniques allow for the creation of complex shapes and integrated cooling systems, essential for battery performance and longevity.
7. Controller Boxes
Controller boxes house the electronic brain of the EV. Made from materials like PA66 or PC, these boxes protect sensitive electronic components from heat, cold, and electromagnetic interference. The precision of injection molding is crucial here, as it ensures the exact fit and protection needed for these sophisticated electronic systems.
8. Motor Casings
Motor casings in EVs are not just protective shells; they are integral to the motor’s performance. While traditionally made from metals like aluminum alloy or cast iron, advancements in plastics technology have led to the use of injection molded plastics in some applications. These materials offer a reduction in weight, which is vital for the efficiency and performance of electric vehicles.
9. Charging Ports
Charging ports are the lifelines of EVs. Injection molded from durable plastics, these ports are designed to withstand repeated use and exposure to environmental elements. The design and manufacturing of these ports are critical, as they must ensure a secure and stable connection for fast and efficient charging.
10. Radiator Grilles
Radiator grilles in EVs, while not used for engine cooling, play a vital role in aerodynamics and protecting the vehicle’s battery and electronic systems. Manufacturers use injection molded plastics to make these grilles, designing them for optimal airflow to contribute to the vehicle’s overall efficiency and performance.
11. Interior Trim
The interior trim of an EV, including the dashboard, control panels, and door panels, is often made from high-quality injection molded plastics. Manufacturers select these materials for their durability, aesthetic appeal, and the ability to mold them into complex, ergonomic shapes. They also play a role in the vehicle’s acoustic design, helping to create a quiet and comfortable interior environment.
12. Seat Components
Seat components such as adjusters, brackets, and knobs are crucial for the functionality and comfort of vehicle seats. Injection molding allows for the precise and durable production of these parts, ensuring smooth operation and long-lasting performance.
13. Air Conditioning Vents
Manufacturers precisely make air conditioning vents, essential for passenger comfort, through injection molding. This process allows for the creation of vents that can effectively direct airflow while blending seamlessly into the vehicle’s interior design.
14. Storage Boxes, Cup Holders, and Bags
Storage solutions in EVs, including boxes, cup holders (also check the cup overmolding process), and bags, are typically made using injection molding. This process allows for the creation of durable, functional, and aesthetically pleasing storage options that enhance the usability of the vehicle’s interior.
Conclusion
In summary, electric vehicles utilize a wide range of injection molded parts, from dashboards to storage solutions. These components undergo precise mold manufacturing, injection molding, surface treatment, and quality testing to meet stringent quality and performance standards. As the electric vehicle industry evolves, the role of injection molding in manufacturing these essential parts continues to grow, highlighting its significance in modern automotive production.