A sink mark is a typical injection molding flaw that can appear in the thicker dimensions of a molded part or object. Thankfully, with the right ways, you can prevent the sink mark from occurring in the injection molded parts. Now, if you’re new to exploring sink marks and how to avoid sink marks in injection molding, let’s go ahead and explore everything about it below in detail.
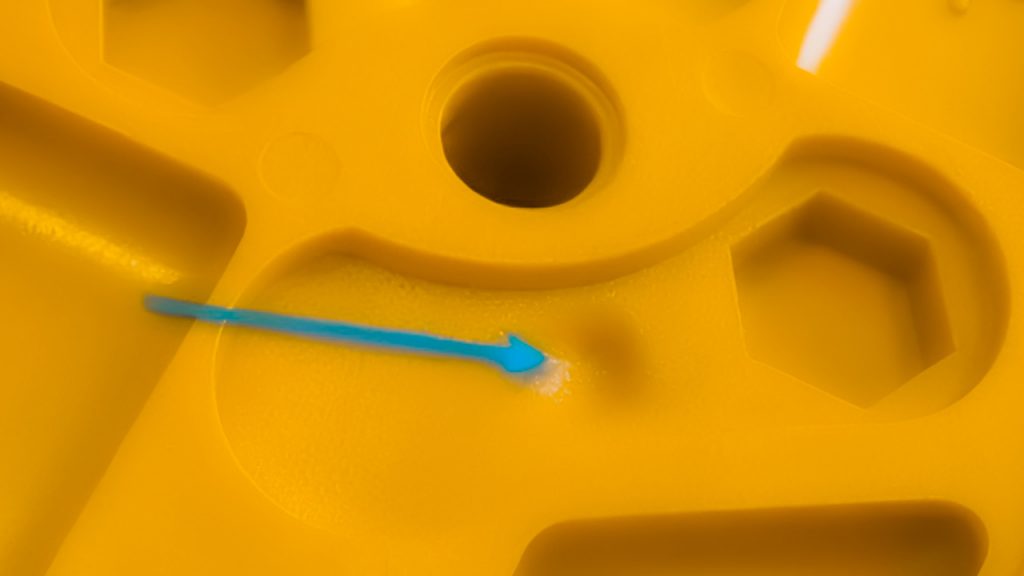
What is Sink Mark?
For beginners or people unfamiliar with the processo de moldagem por injeção, a sink mark e what causes sink marks in injection molded parts can be unfamiliar. But using molded products with sink marks can lead to other manufacturing and product usage defects.
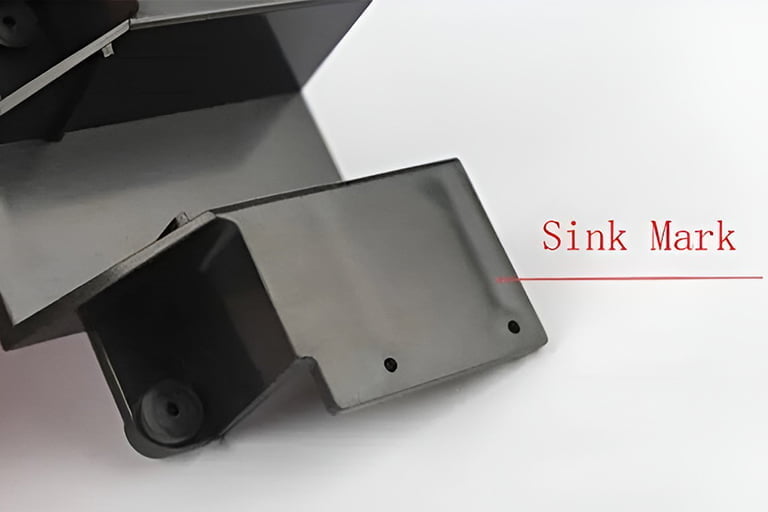
Now a sink mark injection molding is simply depression on the surface of a molded object or part. When it comes to what causes sink marks in injection molded parts, there can be various factors depending on the type or material of the part, i.e., whether it is plastic, metal, etc. Specifically, in injection molded plastic parts, whenever a substance having thick characteristics like chefes or ribs is compressed during the injection molding process, more than the substance present in the abutting wall, sink marks tend to appear.
It is mainly because these characteristics of thick plastic parts lead to a thicker zone that takes more time to cool down than its surrounding dimensions/areas. These distinctive cooling rates create a sink mark in plastic molded objects, which is seen as a dip on the neighboring surface of the object. Such defeitos, known as sink mark injection molding, are especially problematic when developing and molding thin-walled plastic items like TV bezels and screen monitors. Yet, these marks may not be equally visible on all consumer products made with injection molded plastic. For instance, customer electrical parts may not have a visible sink mark, but plastic toys may have such marks on their exterior.
Although the depressions that often occur in the form of sink marks are small, products with these depressions reflect light from different angles. Hence, due to the reflection of light from diverse angles, the sink marks are easy to spot and very obvious in the molded parts. In addition, a sink mark is evident depending on the color and texture of the molded object. Thus depth is only one issue to consider. Even though sink marks do not influence part longevity or performance, they are considered severe quality flaws.
Dicas: For more information about sink marks, please clique aqui
Its Causes:
Besides knowing the basic scenarios that cause a sink mark in injection molding, it is also essential to be well familiar with diverse scenarios of what causes sink marks in injection molded parts. Various factors can result in the occurrence of sink marks, including processing procedures, part shape, material selectione tooling design.
It’s important to understand these scenarios and have detailed know-how of injection molding. It is where your toolmaker or injection molding expert has the power to use various tooling design elements to prevent or alter the sink mark from occurring or affecting the molded part. Ranging from the gate type to the gate size and cooling-channel design, all impact the prevention or occurrence of sink marks. And with the right injection molding experts, it can be easily analyzed and prevented or solved to ensure the quality and outlook of the molded products for further usage.
Yet, before you proceed with considering injection molding experts like Prototool for handling a sink mark occurrence or its prevention in the molded object, let’s go ahead and explore some basic scenarios of what causes sink marks in injection molded parts:
Reasons for a Sink Mark to Appear:
· Extremely High Temperature of the Mold Surface Opposite to the Rib, Resulting in the Shrinkage of Molded Parts:
The mold surface across the rib has a greater temperature than the area close to it. In general, the mold temperature remains high because of the local concentration of molten rubber and the immense heat load. Hence, for the condensation layer to form more quickly, with more stiffness and less likelihood of depression, the mold surface opposite the rib must be cooled down to lower the mold temperature.
· Usage of Very Small Sprue, Runner, and Gate for the Production of Injection Molded Parts:
The flow resistance increases if the abeto, corredor, ou portão is too tiny. In contrast, if the injection pressure is insufficient to produce injection molded parts, the cavity may not be filled, leading to a low melting density and a significant likelihood of denting in the molded parts. This is another reason that can cause a sink mark to appear.
· Improper Location or Amount of Gates Used During the Production of Injection Molded Objects:
Regardless of whether the number or placement of gates is incorrect, the flow length and resistance will be excessive. However, if the injection pressure is insufficient, the cavity cannot be filled, leading to a lower density of molten rubber is low. This lower density leads to a high possibility of denting, which further causes sink mark injection molding.
Sometimes, no matter how the machine is adjusted, the shrinkage of the outer surface of the injection molded item at the cylindrical (cylinder) location is challenging to address owing to a problem in mold manufacture. In such scenarios, even if the issue is resolved, the injection molded component is already a full-body batch front, making shrinkage non-apparent on these parts.
· Limited Cooling Time:
As mentioned earlier, due to insufficient cooling time, the plastic condensation layer is not thick enough to withstand the internal melt glue curing shrinkage caused by stress, resulting in the formation of a dent. This issue can often be prevented with the help of material suppliers’ suggestions on cooling times for various plastics e product thicknesses.
· Extremely High Temperature of Material Tube Leading to a Shrink Mark:
When the material tube’s temperature is too high, the density of the melt glue is low, and as it cools, the melt glue near the cavity’s surface first hardens into a condensation layer (Frozen Layer). As a result, this causes the volume of the plastic to shrink. Now, if you wait until the central melt glue is also gradually hardened, the cavity will be hollowed out, and the cavity wall will be thick with tensile stress. If the condensation layer’s stiffness is insufficient, it will collapse inward and create a depression. In this scenario, lowering the material’s temperature will increase the molten glue’s density and decrease the likelihood that it will sink.
Apart from this, various other scenarios can be linked with different aspects of the injection molding process, like the equipment, injection molding conditions, materiaise o temperature that may also lead to a sink mark.
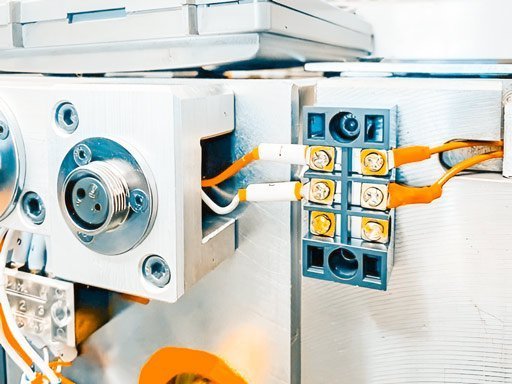
Practical Solutions to Deal with Sink Mark in Injection Molding
Besides exploring what causes sink marks in injection molded parts, it’s also essential to be familiar with the appropriate solutions to deal with them in injection molding parts after they are created. Here are a few practical solutions that can help better handle a sink mark in molded products:
- The cooling time should be kept to a minimum to prevent the deformation of the injection-molded pieces. It is because a higher temperature results in prematurely expelling the injection-molded components.
- Usually, the rising temperature of the mold surface makes cooling insufficient, which leads to sink and concavation issues. Therefore, the injection molded object is adequately chilled to preserve a specific hardness on its surface after prematurely releasing it so that surface sink marks cannot quickly form. However, cooling won’t eliminate the sink markings if the issue with the sink is severe. Hence, to deal with a more severe sink mark, the surface of the molded object must immediately harden to avoid shrinking without excluding the inner shrinkage holes from the product. You can accomplish this by freezing the water.
- Sometimes the sink issue may not be fully resolved by the aforementioned techniques. In such situations, a sufficient amount of an anti-shrinkage chemical should only be used as a last option if surface sink marks absolutely must be eliminated. Transparent components, however, cannot be used in this manner.
Preventing Sink Marks:
Lastly, there is no denying the statement that prevention is better than cure. So before you even end up facing a sink mark issue in your injection molded products or objects, you can use effective injection molding procedures and work in ideal environments to proceed with the molding process without worrying about sinks.
Specifically, emphasizing the manipulation of procedure conditions or designing a component or part to quickly produce more of a particular part without any sink marks – are both ideal approaches to prevent a sink mark in the first place.
Conclusão:
For more details and queries, feel free to contact injection molding experts to help you handle sink mark issues effectively without compromising on the molded parts’ quality, performance, and outlook.