A CNC or Computer Numerical Control is a machining method. In the CNC machining method, the CNC machining tolerances play a vital role in determining how the machine variables can be changed per different production demands. Typically, a Máquina CNC comprising computer programming and electromechanical devices automates metal and non-metal parts as per those parts’ automation and production demands. Additionally, these machines ideally conduct all the operations involved in the metal and non-metal products production/automation as per the program and its parameter tolerances to create a final and usable product.
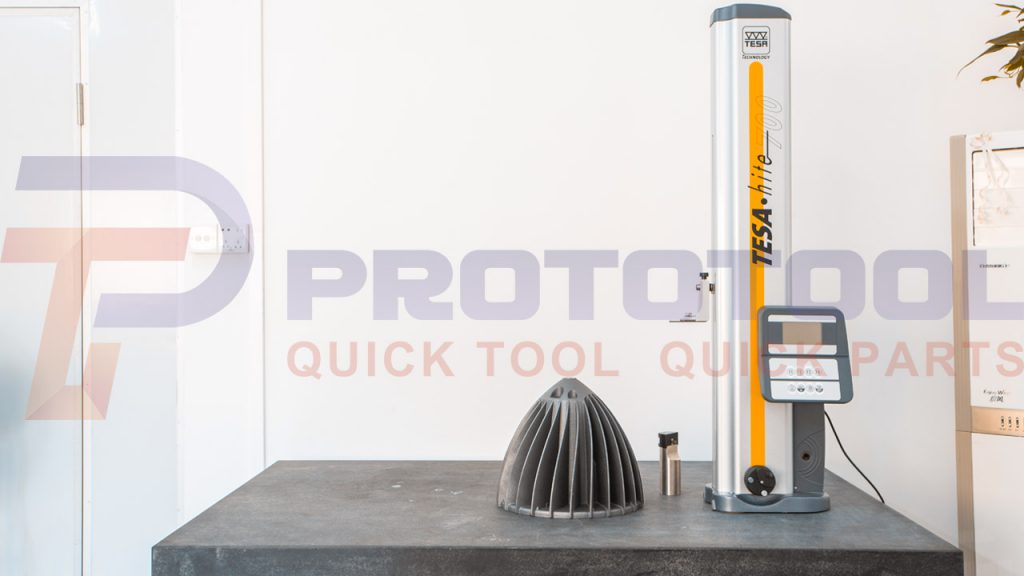
Utilizar um Máquina CNC is common in today’s industrial and manufacturing industries. However, it’s crucial to understand the CNC machining tolerances standards and their practical usage to create ideal end products per the user’s demands. This guide will cover everything you need to know to understand CNC machining tolerances deeply.
Guide to CNC Machining Tolerances:
What are Machining Tolerances?
Machines and machining processes have become exceptionally accurate in the contemporary world. However, maintaining precise precision isn’t always possible for machines, even with great accuracy. Whether it be due to the machining process being used or various factors of the part material, like the size, etc., variances can prevent machines from maintaining a definite precision. Engineers, as a result, maintain the precision of the machining process and the result of the product by assigning machining tolerances standards to the machine parts during their design phase. The typical machining tolerances set on the machine parts ensure that the parts cannot process a product if it doesn’t meet the tolerance requirements. The same design infrastructure is utilized for the CNC machining tolerances.
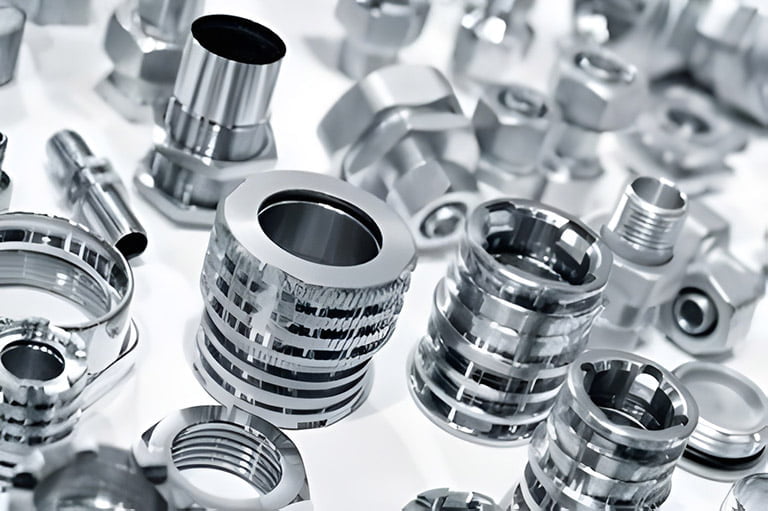
Speaking of which, when it comes to fabricating components and parts, Maquinação CNC has surpassed all others in terms of popularity. Today, the usage of these machines is widespread in all industries. Furthermore, due to technological advancements, these machines have significantly improved in several respects, including their ability to perform automated procedures, their level of precision, and their ability to achieve extremely close tolerances.
O length, width, heighte bend radius, among many other factors for most industrial applications, have a tolerance or acceptance range for the parts or components that must be machined or automated. This specific acceptance range allows the result of machined products to be precisely similar to their structural and usage demands, making them more efficient. Due to this specific reason, minimal variation in these parameters is tolerated when machining metal and non-metal parts, making machining tolerances or CNC machining tolerances highly essential for the efficient management of production and automation industries.
Why are CNC Machining Tolerances Important?
While standard tolerances are always present to handle machining for non-tolerance dimensions, having machining tolerance for different machine parts can be important in many ways. A few of the factors that make CNC machining tolerances necessary in both cases are:
Minimized Production Costs and Improved Turnaround Time:
When you provide a Maquinação CNC tolerance to your trusted manufacturer, it can be easier for the manufacturer to get behind with the automation of the product immediately. In this situation, there is also no need to go through the CNC machining tolerances chart. With just the provided tolerances, your manufacturer can start the work as soon as they receive the product design and dimensional limitations per the product’s usage. As a result, the cost of production is automatically minimized while allowing you to receive the product in a limited time.
Limited Retooling Costs:
The thing about having specific CNC machining tolerances is that it helps limit errors and the need for retooling the automated products. Usually, manufacturers refuse to work on a product or part without receiving specific machining tolerance standards from the customer themselves. As a result, emphasizing the tolerances preferred by the customer for using a Máquina CNC helps reduce the reworking and retooling costs for the manufacturer and the customer. In addition, it saves time and ensures limited retooling on the product or part errors due to the processing of a part by engineers using the wrong tolerances.
Lengthy Processing Time Affecting the Customer’s Business:
Where provided CNC machining tolerance plays a massive role in making the entire process faster and budget-friendly for the customer, the absence of tolerances can do the opposite. When running a product designing or supplying business, it is essential to provide parts in less time, or at least at the time you further promise to deliver to your client/company.
In such situations, when you do not share CNC machining tolerance with the manufacturer/engineers, they tend to use a CNC machining tolerances chart with different tolerances values, which typically doesn’t work well with all kinds of the products’ machining process. Following the wrong tolerances means automation or machining a product with the wrong size, width, length, or any other parameter. In addition, the wrong parameters of a product affect its ability to fit in the shaft/machine during its usage.
It leads to the need for retooling the product, making the engineers go through the process from the beginning. And if there is no complete CNC machining tolerance chart that specifies the exact parameters of the product, it may repeat this retooling phase a few times. Not only does this exceed the budget of the product machining, but it also makes the production more time-taking, impacting the designer’s or supplier’s business turnover rate.
Factors that Impact Machining Tolerances:
Do you ever ask yourself why CNC machining tolerances differ for different products? If machining tolerance standards exist, why is it essential to consider specific parameter tolerance during any metal or non-metal products? Here’s the answer: every product and its properties are different. These properties of the product affect its usage demands and efficiency – making the production and machining followed by different tolerance.
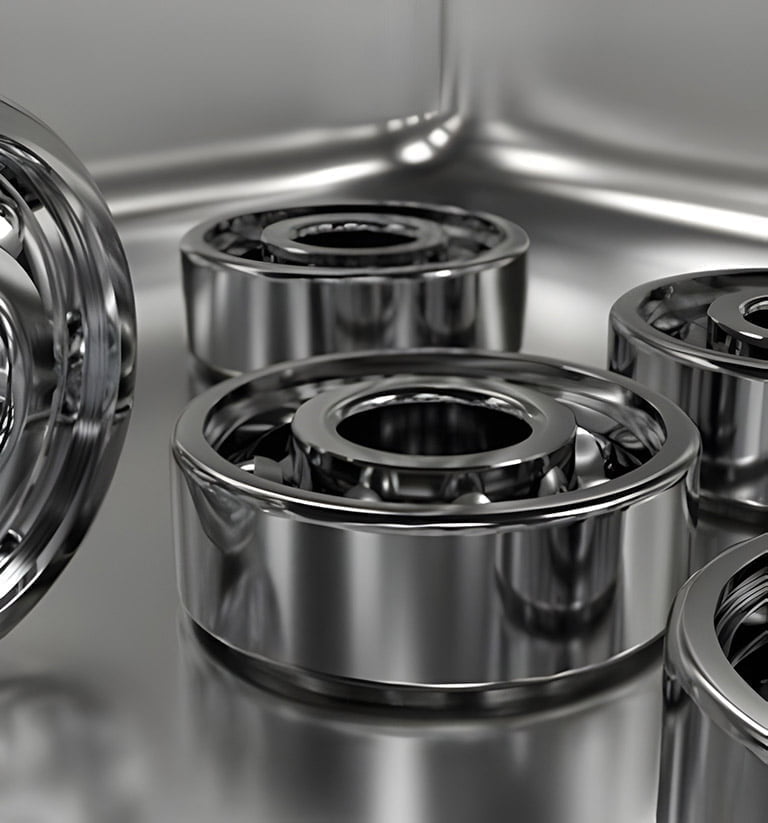
As a result, the typical machining tolerances do not work ideally for every product’s manufacturing and automation. Likewise, when determining the tolerance of a product or part, you should consider multiple factors to create an effective CNC machining tolerances chart. Some such factors to consider include the following:
Materiais:
Every CNC material has a different reaction under production and automation stress. Some materials are easier to work with as compared to other complicated materials. What helps differentiate these materials and choose the easy-to-work ones is their properties. Considering the properties of the materials you should plan to make use of helps better determine which material you should proceed with using for machining. Additionally, the material properties, once you finalize a particular material, also help determine the behavioral structure of the material under stress – allowing you to list down practical and usable machining tolerances standards accordingly.
Type of Machining:
With a Máquina CNC advancing over time, the working and performance structure is no more basic and limited to a specific machining type in this machine. Instead, Maquinação CNC allows you to choose the machining method per the finished product/part tolerance. It is because some processes involved in machining are more processes than others, impacting the finished part tolerances for every product. So it is also essential to choose the proper machining process per the requirements and final product.
Plating and Finishing Phase:
When creating the CNC machining tolerances chart for the specific part that needs processing, you must also consider the plating or finishing process. Any plating or finishing process you wish for the product to go through will affect the product’s dimensions and intolerance. Hence, considering them beforehand is essential to finalize how the entire process should proceed for an ideal product result. However, what makes plating and finishing most important is the small number of materials they add to the surface of a part. This small amount of materials further changes the dimensions of the final product, making it different from the result you want if you do not take this process into account post-production.
Custo:
Lastly, if all goes well, the final thing you should not miss to consider when noting down the CNC machining tolerances for your product is the cost. Simply put, the tolerances you finalize for the product processing shouldn’t be too tight. While tighter tolerance may become challenging to achieve at most, they also double your expenses. The best way to avoid this issue when finalizing the typical machining tolerances for your product is to be precise to exclude extra costs on tighter tolerance that may not be wanted in the first place.
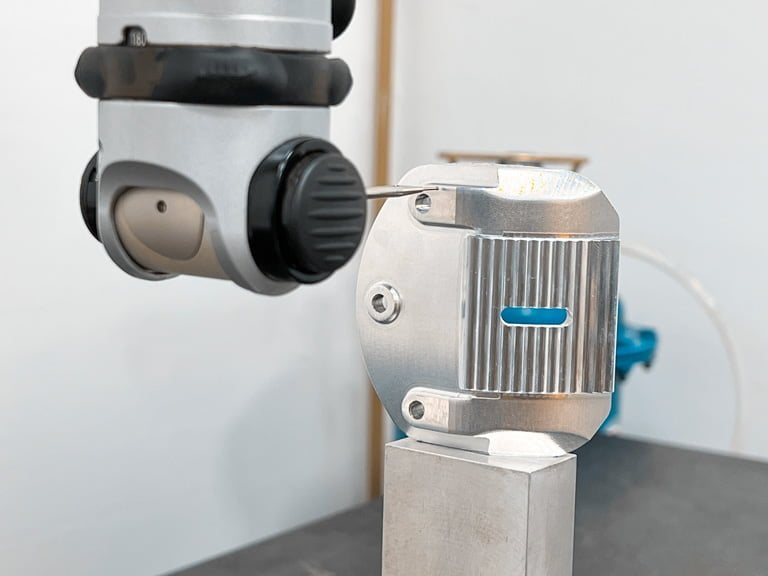
Conclusão
Educating yourself about CNC machines and CNC machining tolerances standards before proceeding with product automation can help a lot. Not only can you better judge and finalize reliable manufacturing services and engineers that know what to do, but you also achieve a final product that fulfills your design and usage requirements.
Frequently Asked Questions (FAQs)
What are the standard tolerances for machining?
More often than usual, when you invest in product machining and automation by manufacturing companies, they require you to give specific machining tolerances standards to proceed with the machining accordingly. But if that’s not the case, the standard tolerance for machining, especially for Serviço de maquinagem CNC, is usually about ±0.005 inches (±0.127 mm). Although the naked eye may not be able to detect this slight discrepancy, it may affect how your finished product fits together.