Injection molding is a highly efficient and widely used process for manufacturing complex plastic parts. Professionals inject molten plastic into a mold cavity in this process, which cools and solidifies into the desired shape. To ensure a successful molding process, it is essential to carefully consider the design and placement of the sprue. The sprue in injection molding is a passage that allows molten plastic to enter the mold chamber. Typically, you should set it at the thickest section of the part, where it can effectively fill the cavity and minimize the risk of defects such as voids, sink marks, and warpage. However, the sprue’s location and design can also significantly impact the quality of the finished part and the efficiency of the molding process.
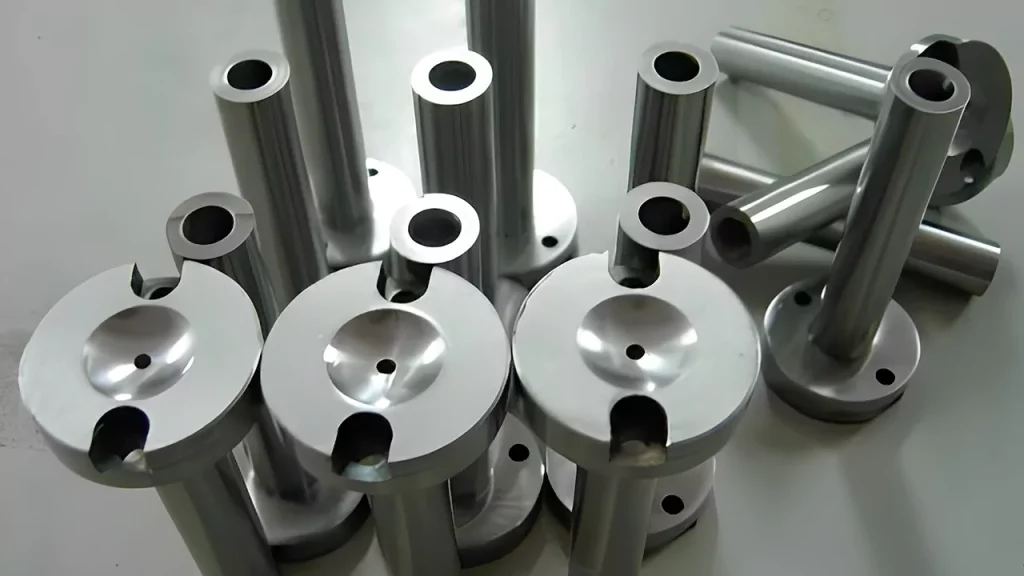
Now let’s go ahead and discuss the importance of sprue location in injection molding and some key considerations when designing and using sprues.
Sprue Definition
The sprue is an essential component of the injection molding process. It is a channel that connects the injection unit of the molding machine to the cavity in the mold. The sprue in injection molding is where the molten material enters the mold.
Eventually, you can trim off excess material after forming the part. The design of these sprues is in various shapes and sizes, depending on the mold’s specific requirements and the part you are producing.
Why is Sprue Location Important?
The location of the sprue is critical for ensuring that the molten plastic flows evenly into the mold cavity, filling all of the features and details of the part. If the sprue is too far from the thickest section of the part, the plastic may not flow evenly, resulting in incomplete filling and potential defects such as voids and sink marks.
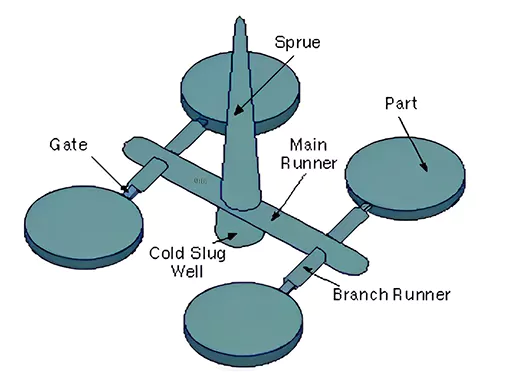
Conversely, if you set the sprue too close to the thickest section of the part, the plastic may cool too quickly, leading to warpage and other issues.
The plastic flow is an essential factor when selecting the sprue location. In general, plastic flows from the thickest section of the part towards the thinnest area. Therefore, locate the sprue at the thickest section of the part, which can effectively fill the cavity and prevent defects.
In addition, one should position the sprue so that the plastic flows evenly throughout the part without creating areas of high stress or excessive shear.
Another critical consideration when selecting the sprue location is the ejection of the part from the mold. The sprue in injection molding is typically attached to the part during the molding process. Once you eject the part from the mold, you should remove the sprue.
Therefore, the sprue location should be selected to not interfere with the ejection of the part or create areas of stress that could affect the part’s strength or durability.
Basics of Designing and Using Sprues
When designing and using sprues, you should consider several important factors to achieve optimal performance and efficiency in the injection molding process.
One key factor is the size and shape of the sprue. Make sure to design the sprue in injection molding to accommodate the molten plastic’s volume and flow rate while minimizing the pressure drop and turbulence in the flow. The sprue should generally be tapered and smooth, gradually transitioning from the runner to the cavity. This helps to reduce shear and pressure and ensures even flow throughout the part.
Another important consideration is the number and placement of the sprues. Sometimes, a single sprue may be sufficient to fill the mold cavity and produce a high-quality part. However, in more complex parts with multiple features and details, various sprues may be necessary to ensure even filling and prevent defects.
Having said that, it is crucial to carefully select the placement of the sprues to avoid areas of high stress or excessive shear while also ensuring even flow throughout the part.
The material used for the sprue is also an essential factor to consider. Make the sprue in injection molding out of a material compatible with molten plastic that can endure the injection molding process’s high temperatures and pressures. In addition, the sprue design should minimize heat loss and ensure even heating throughout the part to prevent warpage and other defects.
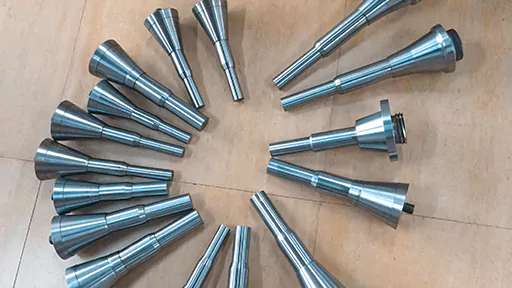
Technical Considerations for Designing Sprue in Injection Molding:
Sprue Design
The design of the sprue is also critical to the success of the injection molding process. The design of the sprue must allow the molten material to flow smoothly and evenly into the mold cavity without causing any defects in the finished part. Moreover, the design of the sprue must also allow the excess material to be trimmed off easily without leaving any marks or blemishes on the finished part.
One important consideration when designing the sprue is the diameter of the channel. The diameter of the sprue in injection molding should be large enough to allow the molten material to flow easily but not so large that it causes turbulence or other flow-related issues. The diameter of the sprue may need to be adjusted depending on the viscosity of the material you are using.
Another consideration when designing the sprue is the shape of the channel. The channel design should allow the molten material to flow smoothly and evenly into the mold cavity. The shape of the channel may need to be adjusted depending on the specific geometry of the part you are producing.
Sprue Material
The material used to make the sprue is also important. The sprue material must resist the high temperatures and pressures generated during the injection molding process. The material must also withstand wear and tear from the molten material and the trimming process.
The most common materials used to make sprues are metals such as steel or aluminum. These materials are solid, long-lasting, and can survive the injection molding process’s high temperatures and pressures.
The Exact Method of Utilizing Sprue in Injection Molding:
Many phases are involved in the injection molding process, and using a sprue is crucial to ensure that the molten material is accurately injected into the mold cavity. This section will explore using a sprue in the injection molding process.
Step 1: Preparation
Before the injection molding process can begin, you must prepare the mold. This includes ensuring that the mold is clean and free from any debris and that the mold is aligned correctly and clamped in place. The sprue must also be attached to the mold in the correct position.
Step 2: Injection
Once you prepare the mold, the injection molding process can begin. Here, you must inject molten material into the mold cavity through the sprue in injection molding. The injection unit of the molding machine pushes the molten material through the sprue and into the mold cavity under high pressure and temperature. The molten material fills the mold cavity and takes the shape of the part you are producing.
Step 3: Cooling
After filling the mold cavity with molten material, the mold must cool down. The cooling process allows the material to solidify and take on the desired shape. Varying on the size and complexity of the device, the amount of time that must pass before the system cools could take a few seconds to several minutes.
Step 4: Ejection
Once the material has cooled and solidified, opening the mold and ejecting the finished part is essential. The excess material, including the sprue, must be trimmed off the part before it is ready for usage. The sprue in injection molding is typically located at the edge of the finished part and quickly trimmed off using a cutting tool.
Step 5: Cleanup
After you eject the finished part from the mold, the mold must be cleaned and prepared for the next injection molding cycle. This includes removing any excess material or debris from the mold and ensuring proper positioning of the sprue for the next injection cycle.
Conclusion
Using sprue is critical to the success of the injection molding process. The sprue in injection molding allows the molten material to be injected into the mold cavity correctly while trimming off the excess material from the finished part.
You should carefully consider the sprue’s location, design, and material to ensure that the injection molding process produces high-quality parts with minimal defects. Manufacturers can make high-quality parts efficiently and effectively by following the proper procedure for using a sprue in the injection molding process.