Since its inception, the plastic injection molding market has advanced significantly. It has advanced significantly in terms of productivity, cost-effectiveness, and new and creative approaches to product manufacturing. Two-shot injection molding is one of these creative methods. Multi-material injection molding, two-color injection molding, two-k injection molding, or double-shot injection molding are other names for this procedure.
People inject two separate materials into the same mold to create the product in two-shot injection molding. These substances are administered sequentially rather than simultaneously. The product is not discharged from the mold between the two shoots but is produced in a single step.
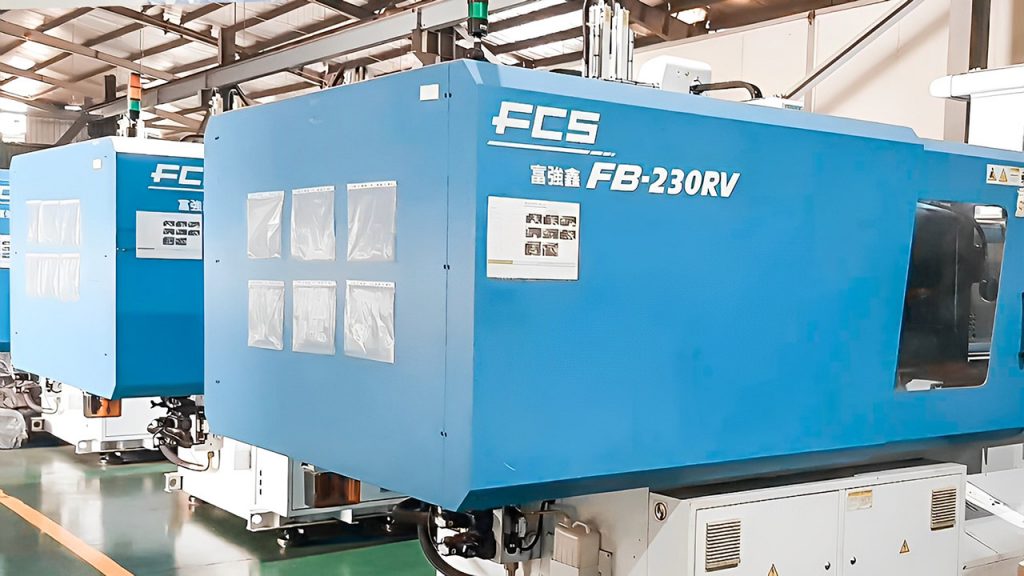
Because two-shot injection molding does not require several production stages, it gives designers more freedom. It offers molding manufacturers a number of benefits, including reduced manufacturing costs, improved ergonomics and aesthetics, superior mechanical bonding, and quicker production times. This process can produce a wide range of goods, including toys, vehicle components, medical equipment, containers, and toiletries.
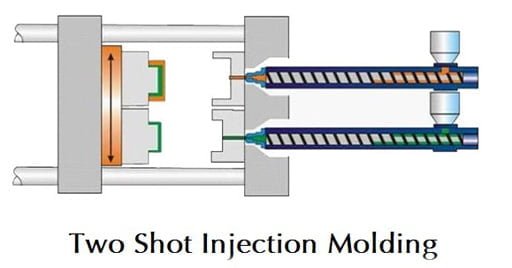
Process of two-shot injection molding
As the name implies, two injection shots are used in this method instead of simply one, as in traditional injection molding. This procedure makes use of a unique mold that meets the needs of these two injections. The mold and the systems that support it are made to produce two shots without requiring the removal of the half-finished product between them.
As with regular injection molding, the procedure begins with mold sealing to create the first cavity. In this initial configuration, the secondary step’s runner is sealed off while the runner for the first cavity is aligned with the base material’s sprue. The first substance is then injected into the opening, filling it.
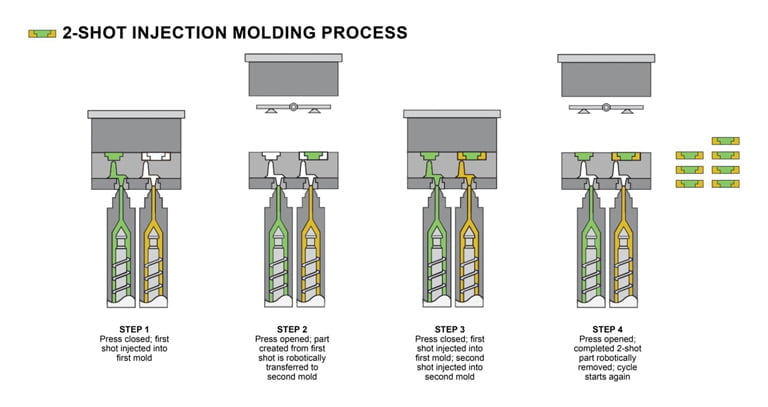
Following the first stage, the mold opens, allowing the platen holding the finished product to rotate 180 degrees on a horizontal axis and line up with the sprue of the following stage. The first cavity is isolated from any injection in this stage. The second shot now starts molding the remaining portion of the product since the sprue of the second material is now in line with the runner for the second cavity.
Never once during this procedure is the product taken out of the mold or moved about in the mold. With the exception of any post-process defects brought on by factors like uneven cooling, the finished product is therefore made with the same precision as the mold itself.
Examples of two-shot injection molding
Toys
Toys made of plastic are beneficial in this procedure. We may sculpt the object in many hues and textures.
Garden equipment
Due to plastic’s advantageous characteristics in a water environment, two-shot injection molding works well in this situation. Softer seal surfaces can be coupled with durable foundation sections.
Toiletries
With two-shot molding, items like toothbrushes may be accurately shaped. It can combine a rigid base plastic with a softer rubber second shot for improved grip and coloring.
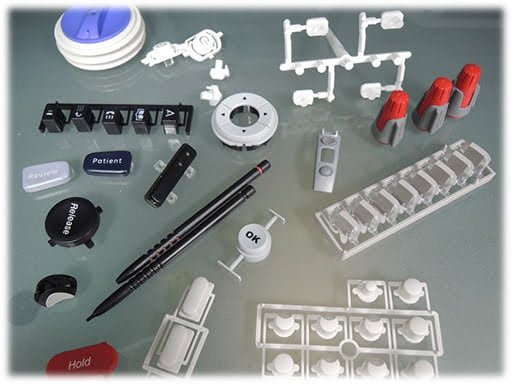
Containers
With this method, you may produce plastic storage containers. Along with rubberized edges to secure lids and soft container surfaces to safeguard contents, other colors can be incorporated.
Electrical goods
Two-shot molding may be used to make plastic electrical items with built-in LEDs efficiently. A transparent insert can be sculpted into the design to distribute or color the LED light.
Medical supplies
Utilizing two-shot molding, you may produce medical equipment such as bone saws. Rubber grips have a crucial role in how well this equipment works. Compared to conventionally constructed things, two-shot molded objects improve cleanliness since there are fewer fissures where sub-parts contact.
Two-shot injection molding benefits
Physical connection
Two-shot injection molded products have excellent mechanical characteristics. Given the excellent material selection, the product’s various levels combine molecularly throughout the molding process. This bond is frequently more durable than traditional molding and assembly and even more durable than other cutting-edge techniques like over- and insert molding.
Aesthetics
Products created using a two-shot method can maintain the necessary structural characteristics while still having a very appealing appearance. The load-bearing structural component can be molded in the first phase of this procedure, and the finishing touches can be applied in the second step using a more attractive material.
Ergonomics
Two-shot injection molding is a procedure that is ideal for producing goods that are ergonomically designed. It is simple to cover or add to structural plastic with materials that are more suitable for human contact. Because it offers a more excellent grip and a gentler touch, soft, rubbery material is more suited for human hands.
Production period
The reduction in manufacturing time is a crucial advantage of two-shot injection molding. There is frequently no need to do secondary assembly of the item since it can add many product tiers during this operation. With the advent of mixed molding, traditional injection molding would have required a whole secondary stage in manufacturing.
Unit price
Two-shot injection molding excels in this situation. Thanks to two-shot molding, A production line can now produce more complicated goods with fewer stages than ever. Think about the standard injection molding procedure: Two distinct materials would have needed to be molded separately in two different molds, followed by a manual assembly phase, if a certain object was made of those materials. In two-shot injection molding, these two components are fused and formed in a single mold configuration, eliminating the need for any assembly.
Precision
Double-shot injection molding offers exact production compared to conventional molding and assembly or even more contemporary techniques like insert molding. There is no possibility of material misalignment because the semi-finished product does not need to be withdrawn from the mold between phases. The finished product can be just as precise as the mold if thermal impacts are appropriately managed through effective product design.
Efficient use of resources
The designer can combine the most outstanding qualities of many injection molding materials via two-shot injection molding. Engineering plastics may have a wide range of beneficial yet quite distinctive qualities. To precisely accomplish the necessary outcomes, the designer can blend the solid structural qualities of hard plastic with the supple and attractive attributes of another material.
Design of 2-shot injection molds and products
In 2-shot molding, several tool sets are employed to create the molds. The tools in a rotating platen configuration have the same cores but different cavities. The runners must be built such that they may be turned off during the inactive molding processes.
- The wall thickness of a part should be carefully considered while designing it for a number of reasons.
- The substrate walls need to be thick enough to bear the stresses from the second step’s molding pressure without collapsing.
- Wall should not be thicker than recommended to prevent the consequences of uneven cooling.
- Wall thickness should not be less than a predetermined minimum to enable accurate and complete material flow into all areas of the cavity.
Ideally, materials should be injected in a certain order while taking the following into account:
- The tougher of the two plastics should be used for the initial shot.
- When using opaque and transparent materials, inject the transparent substance first.
- Typically, inject the material with the higher molding temperature first.
Designing the mold base and inserts:
- Make sure the mold can rotate 180 degrees.
- Any inserts ought to be balanced.
- A return spring should keep the push rod plate and ejector pin steady to prevent damage during mold rotation.
- The cooling system must provide enough performance for both the first and second shots.
Compatibility of materials
The chemistry of the materials must be taken into consideration while choosing ones for double shot injection molding. Some materials may establish a compelling molecular connection even when they may not all link correctly. The table below shows compatibility with adhesion.

Before starting a two-shot injection molding process where adhesion combinations are unknown, an adhesion test must be performed. Undercuts, shoulders, or grooves may be added to the design to lock the two components together when the intrinsic bonding capacity is insufficient.
Factors to take into account before employing two-shot molding
- Before building a mold, run a flow simulation study to ensure the desired design is correct.
- Make sure the design’s structural component is produced in the first instance.
- Before mold construction, find any potential flaws in the process and fix them.
- Think about how much both materials will shrink. Typically, the first (or innermost) shot’s substance determines the shrinkage.
- Remember that the sub gate needs to allow the appropriate runners to be turned off at specific points in the operation.
- The design may permit a slight oversizing of the first shot component, thus taking into account the position of any molded-in logos to prevent damage to them during any stage of the process.
- This guarantees more pressure for the second shot, which results in stronger bonding.
- Make sure the injection setup’s settings deliver the necessary pressure, flow rate, and cooling capabilities.
- Check whether the first shot’s structural durability can resist the second shot’s injection pressure.
Budgets for designing and developing new products may be constrained during a period of constrained resources and cost-cutting. In certain businesses, the tools and expertise required to effectively finish an LSR molding operation are also scarce. As a top supplier of LSR 2-Shot injection molding services, Prototool can assist you in effectively, affordably, and promptly finishing such tasks. For more information on how Prototool can assist you with your LSR 2-Shot injection molding needs, get in touch with us right now.